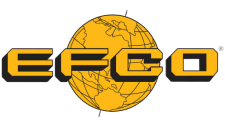
Overview
Seth Bozman, a dedicated quality technician at Efco, shares his journey with Unifize, illustrating the platform's transformative impact on their management of scrap, rework, and data analytics. Efco, known for its manufacturing of steel forms for significant construction projects, faced challenges in tracking these critical metrics effectively. Seth's story highlights how Unifize streamlined these processes, enhancing operational efficiency and data accuracy in a complex manufacturing environment.
Challenge
At Efco, Seth grappled with the cumbersome process of manually tracking scrap and rework data, a crucial aspect of quality control and cost management. Traditional methods relied heavily on physical documentation and fragmented systems, making it difficult to analyze data efficiently and accurately. This not only impeded real-time decision-making but also increased the risk of data inaccuracies and loss.
Solution
Efco's transition to Unifize marked a turning point in addressing these challenges. The platform's tailored functionalities catered to Efco's unique requirements, enabling Seth to monitor and analyze scrap and rework data more effectively. Unifize's integration into Efco's operations facilitated a seamless shift from manual to digital processes, significantly reducing the time and effort required to manage and analyze quality metrics.
Ease of Use
Unifize's user-friendly interface allowed Seth to adapt the platform to Efco's specific operational needs quickly. This adaptability ensured that the shift to digital tracking did not disrupt existing workflows but rather enhanced them, making it easier for Seth and his team to maintain a comprehensive overview of quality metrics without extensive training or adjustment periods.
Communication and Collaboration
The implementation of Unifize revolutionized communication and collaboration within Efco. By centralizing data and discussions related to scrap and rework, the platform ensured that all relevant information was readily accessible to those who needed it. This change eliminated the reliance on inefficient communication methods and fostered a culture of transparency and teamwork in addressing quality issues.
Documentation and Compliance
With Unifize, Efco achieved unprecedented levels of documentation accuracy and compliance efficiency. The platform's robust features supported thorough record-keeping and simplified the audit process, making it easier for Seth and his team to compile and present data for compliance purposes. This not only improved Efco's regulatory adherence but also enhanced its overall quality management practices.
Results
Adopting Unifize led to significant operational improvements at Efco. The time spent on managing and analyzing quality-related data was drastically reduced, allowing Seth and his team to focus more on proactive quality improvement initiatives. The platform's impact extended beyond mere efficiency gains, fostering an environment where data-driven decision-making and continuous improvement became the norm.
Professional Preparedness
The comprehensive and organized data management capabilities of Unifize have empowered Seth with the confidence to handle regulatory inquiries and audits effectively. The platform ensured that Efco stayed ahead of potential compliance issues, reinforcing its commitment to quality and precision in manufacturing processes.
Regulatory Alignment
Unifize supported Efco's adherence to industry standards and regulatory requirements by providing a robust framework for managing and analyzing quality-related data. This alignment was crucial in maintaining the company's reputation for excellence and reliability in the construction industry.
Conclusion
For Seth and Efco, Unifize has proven to be an indispensable tool in enhancing quality management and operational efficiency. The platform's impact on the company's ability to manage scrap, rework, and data analytics effectively is a testament to how technological innovation can coexist with stringent industry standards, leading to significant improvements in operational practices and regulatory compliance.
My name's Seth Bozman. I've been working at Efco for 11 years now. I'm a quality technician.
[00:05 - 00:10]
We build steel forms for concrete companies, bridges, dams, stadiums, stuff like that.
[00:10 - 00:15]
So I'm in charge of keeping track of all scrap and rework, trying to find data analytics for departments.
[00:15 - 00:20]
And yeah, I basically just put the dollar number on reports that people want to see.
[00:20 - 00:36]
Everybody looks at scrap and rework like it's a bad thing, right? It's like we should not have that instead of looking at it as in, say, you have a big sample size of a year or a few months, It's like, why do we keep having these problems with these parts? And so you could trace back rework to an issue, right?
[00:36 - 00:45]
And if you don't log it or you don't care because you're like, let's just keep this under the table and just fix it ourselves. Makes it kind of hard on trying to underlie and find actual problems, right?
[00:45 - 00:55]
Unifize has definitely allowed us to be able to be like, “Hey, we scrapped that out off the laser. It didn't get formed and it didn't get machined. Why is it a $200 part when off the laser it’s $17?”
[00:55 - 00:59]
So we're getting it down finite on the dollar, which is I think, important.
[00:59 - 01:12]
That's a super positive thing for me, being able to get very detailed on what somebody is asking for, you know, because currently there's a lot of people that are using Unifize like supervisors and stuff, but they're not the ones that are asking me for things.
[01:12 - 01:25]
It's somebody that's across the street or they're going to use some kind of information that they might want of laser scrapper or basically it's an infinite amount of possibilities, I guess you can say, with however you want to get that data extracted.
[01:25 - 01:39]
I'd say that that was our priority number one, just making sure that you can load all of our parts and that we could be able to pull data when we needed to and that it would be like live updated and it would keep track of those things without us, fat-fingering something and deleting something on accident and then all of a sudden gone forever and that doesn't happen. So that's nice.
[01:45 - 01:52]
There's a lot of quality audit procedures that we have posted around the plant. It's honestly a lot of it is institutional knowledge, and people just been working here for 30 years.
[01:52 - 01:56]
They teach the other people how to do it, and then it's just kind of like knowledge that's passed on.
[01:56 - 02:03]
But like if it's an operating procedure that's like new, then it seems like it's all hands on deck. On trying to figure out what's the best way to do that process.
[02:03 - 02:12]
We would handwrite every remake card or rework card and they would go down to the floor and then getting it back was always probably the thing that I had to deal with the most.
[02:12 - 02:21]
Just because keeping track of those rework hours and those dollars is completely dependent on this piece of paper that's floating around on the floor somewhere, right. And hopefully it gets turned back in. But there was no guarantee on it.
[02:21 - 02:33]
I can say without a doubt that it's so much easier to keep track of the things that we have on the floor because instead of having it stored in three different places of work, remake cards are out in what they're doing, it's all in one place.
[02:33 - 02:41]
It's just on Unifize. It's just in a conversation. All you have to do is be like, just say three days went by and it's a special and supervisor is like, hey, I really need those parts.
[02:41 - 02:51]
Where are they? You know, it's just in my opinion reduce the amount of confusion of where something could be and it definitely got the piece of paper out of people's hands. You know it's right there.
[02:51 - 02:55]
You most people are sitting at their desk reading emails. It's like Unifize right there. Open it up.
[02:55 - 03:00]
If they're like getting withstanding right, if it's an open form for 11 days for like why is it still open?
[03:00 - 03:11]
Oh it's done. Put the rework time in, you know, and then they put the rework time in. So it's it's a lot more collaborative than I was even expecting, if that makes sense.
[03:11 - 03:21]
Unit material weight (plus) unit material labor (times) the quantity of the part (times) our overhead. So that's the formula, right? To get the total cost of that part that we scrapped.
[03:21 - 03:31]
I won't have to sit at my computer for 3 hours running quality reports because it will automatically run those reports themselves like they're as soon as you enter that part, like the scrap value and everything is already totaled up.
[03:31 - 03:44]
Getting rid of me, having to use Access because there's everything now is just filling out itself because we have our part numbers in there and it's like we don't have to take it out of Unifize to put it into Access to run my quality report anymore. You know what I mean? And it's it's pretty sweet.
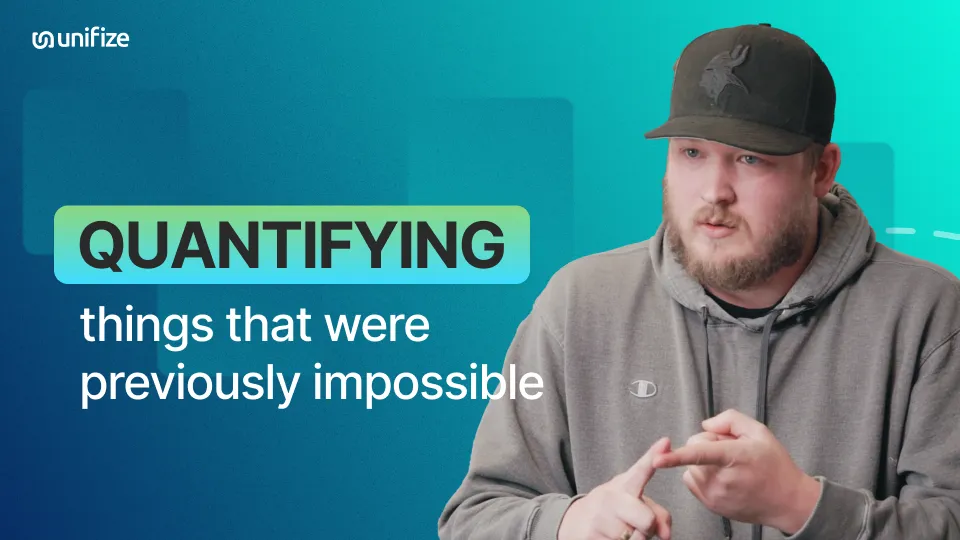

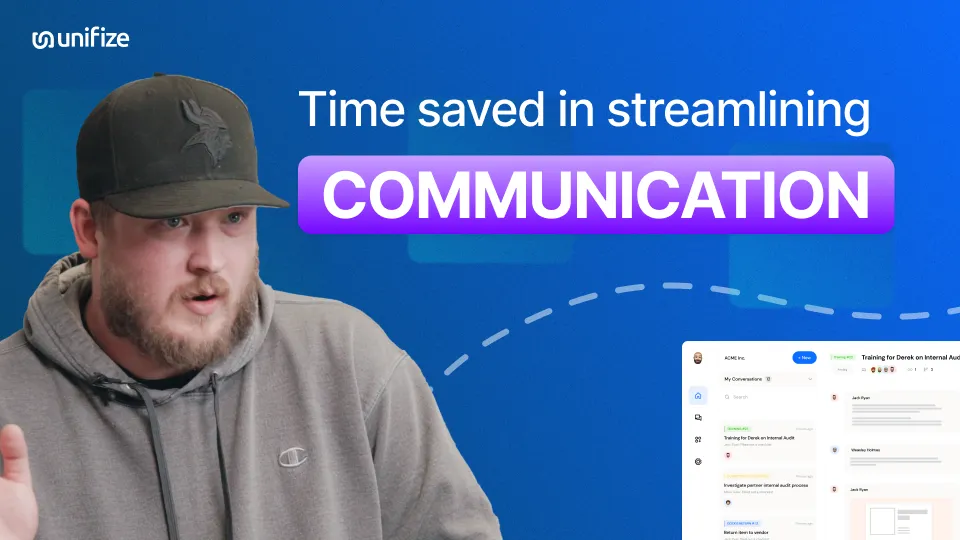

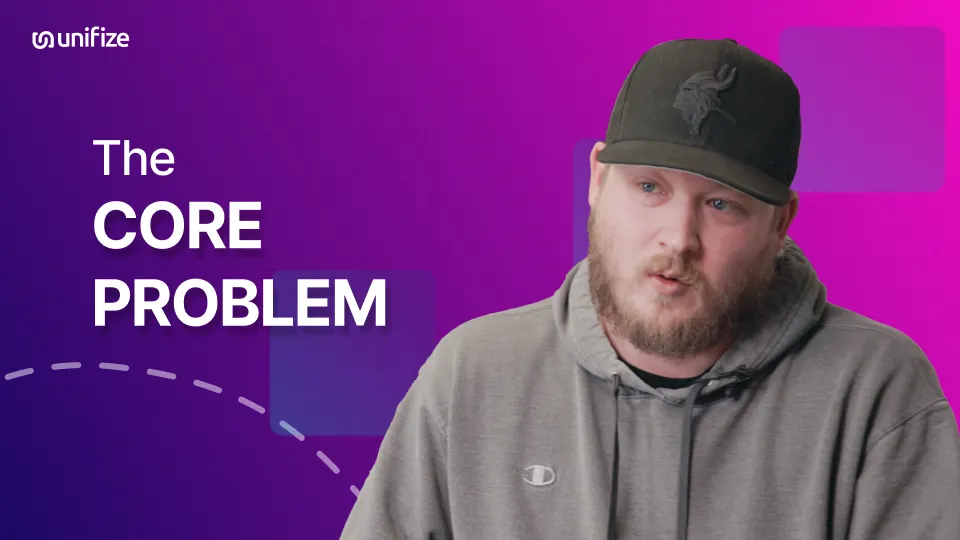

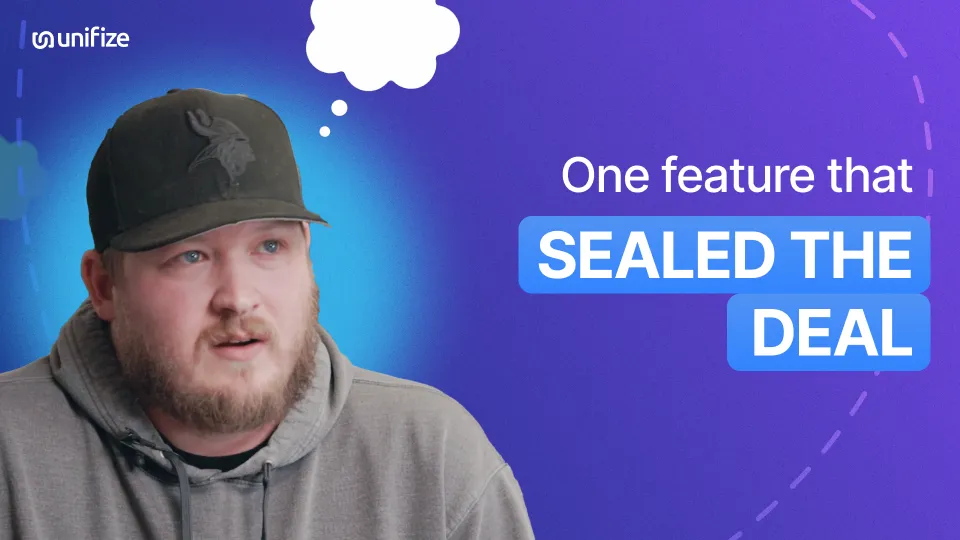

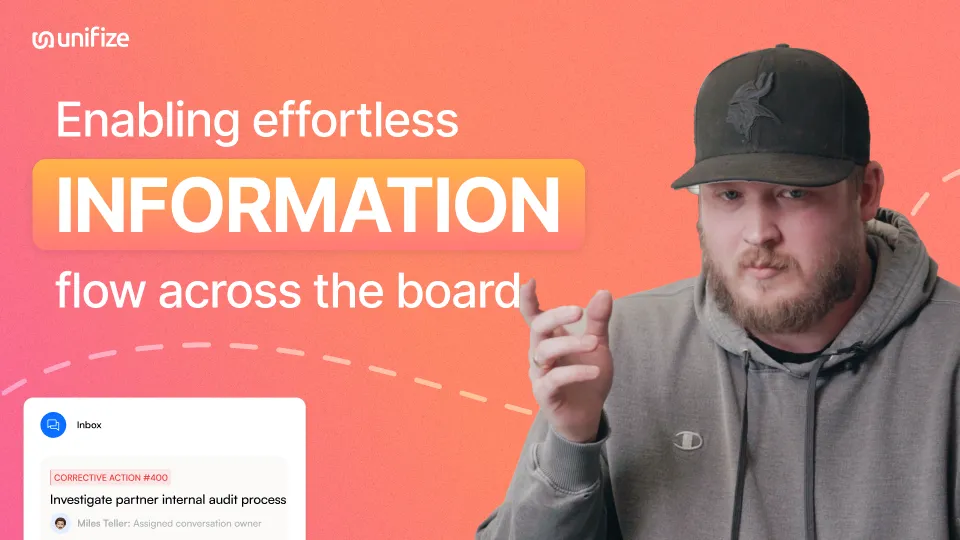

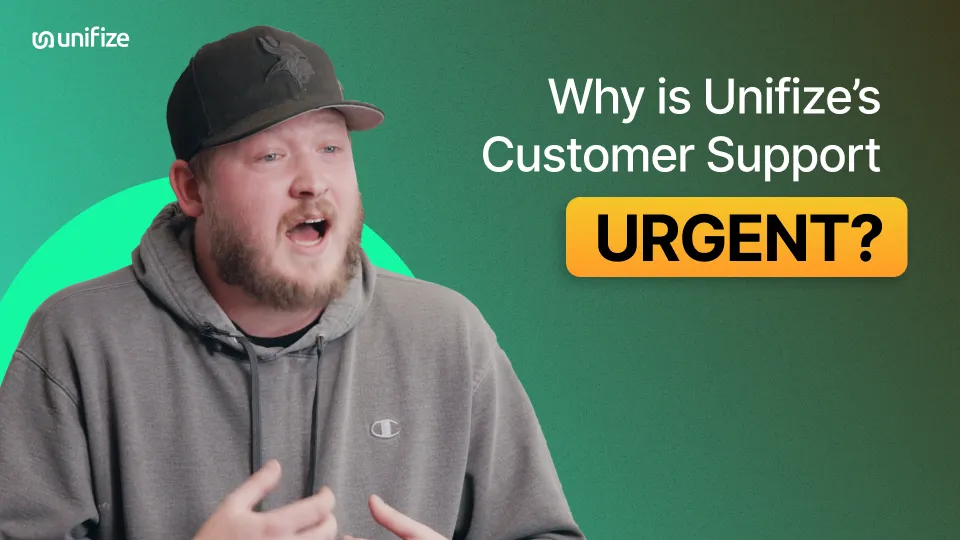

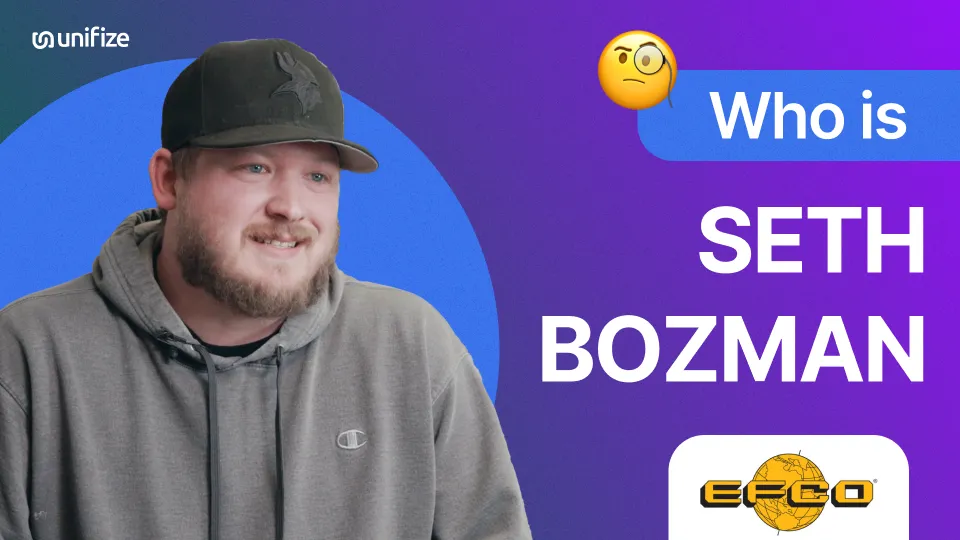

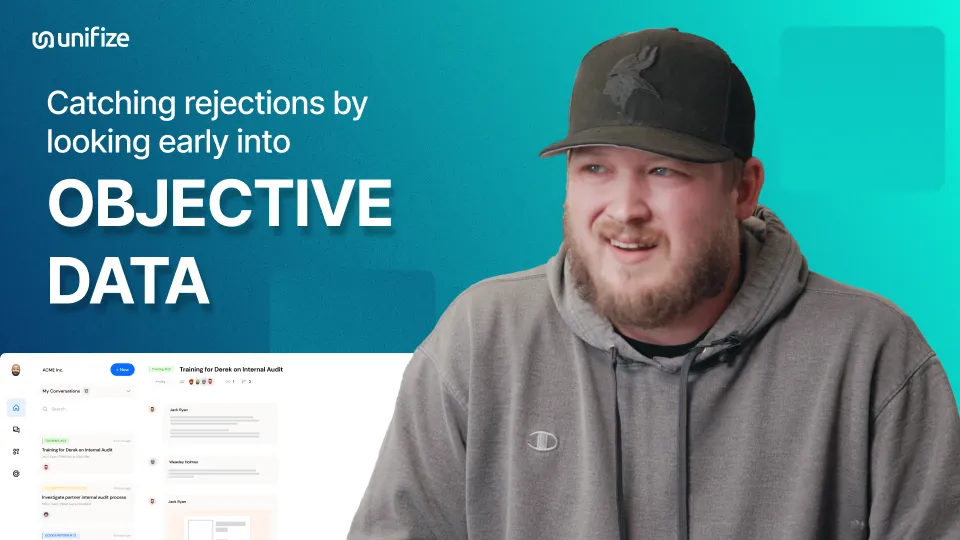

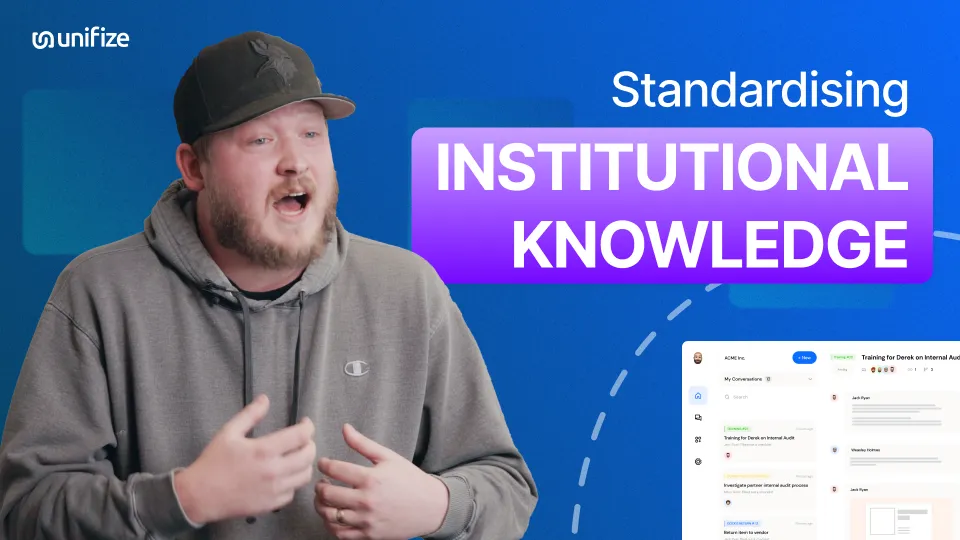

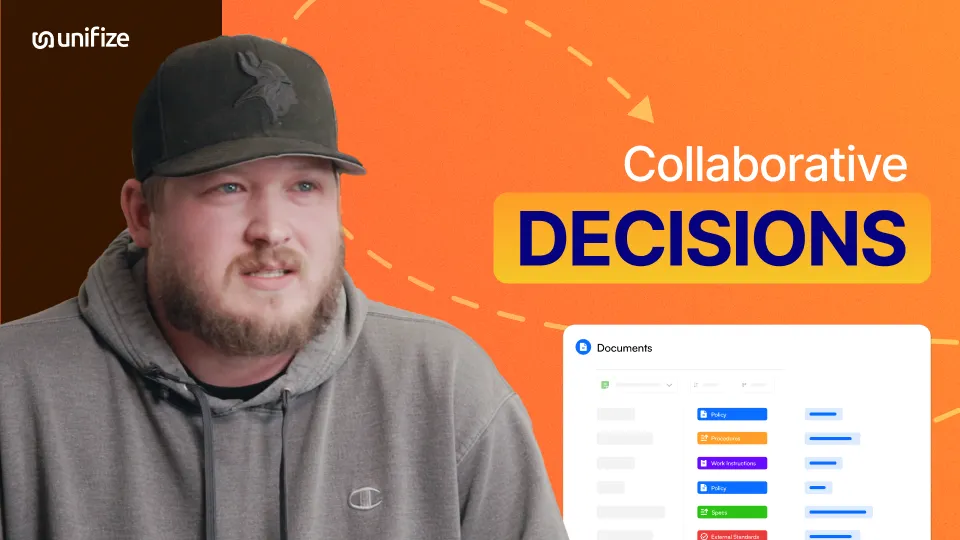

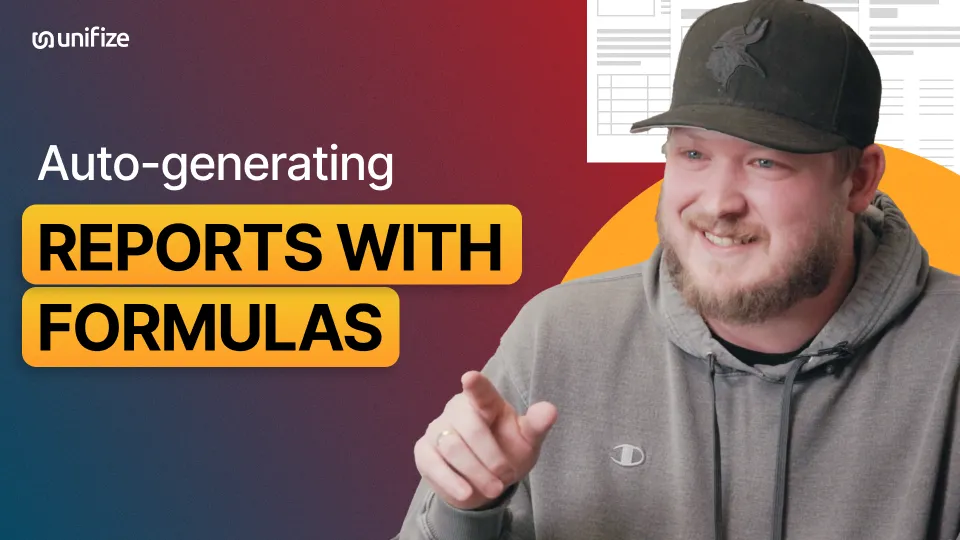

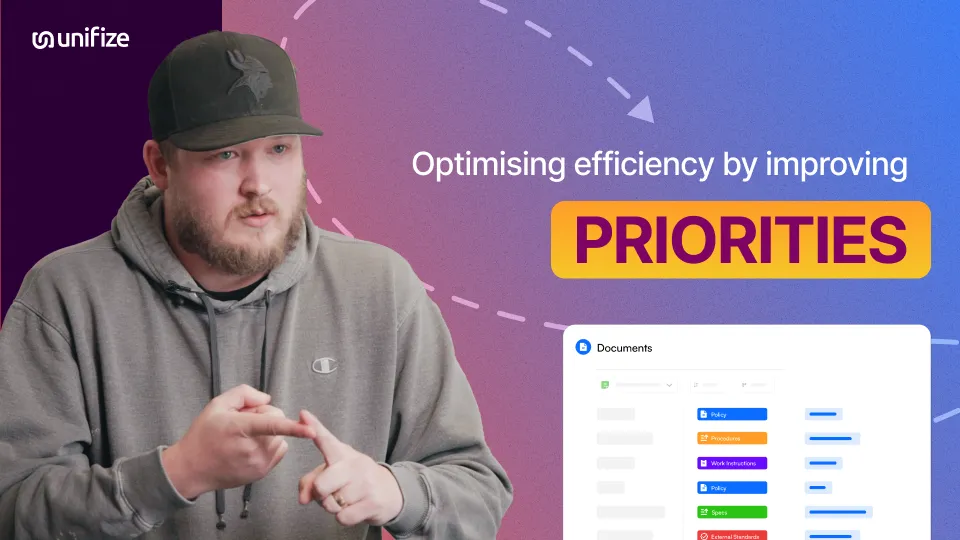

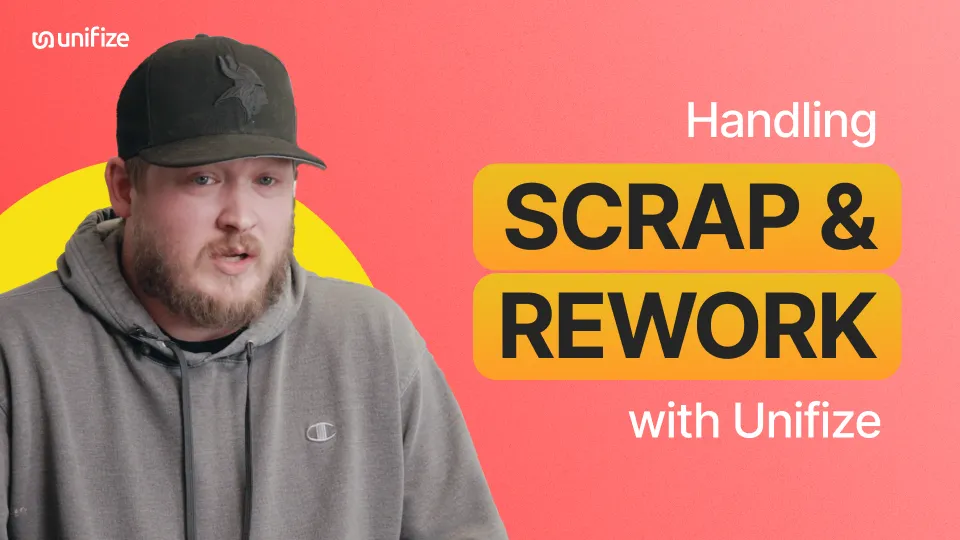

More from Seth Bozman
Unifize Results
Speed to compliance
Faster time-to-market
Fewer meetings