Content Library
00:00 - 00:11
So when Harmony started, it was several grad students at the Renew Robotics Lab working on Robot designs in their spare time.
00:11 - 00:45
You know, it started as a company out of a house, you know, in a neighborhood somewhere in Austin. It was it was a very small team of essentially college students designing what would become the medical device robot. And as we grew, I joined on about two and a half years ago. It became very apparent that we needed a better way of doing documentation, of controlling records, of managing our device requirements and how that traces through to our design outputs.
00:45 - 01:09
In the medical device space. We have a product lifecycle that we need to go through. We need to clearly define our user needs. We need to define our requirements, the outputs that we need to test to and validate. And that's something that, you know, if you're a couple of guys in a college robotics lab, it's just not something that you're thinking about when you're putting together this thing that's never been made before.
01:09 - 01:14
So as we grew as a company, we got more serious about launch and we knew that something had to change.
01:14 - 01:27
What we started with was literally a pen and paper quality system. So like word documents that you'd print out and somebody would be signing pen on paper when let's say a part comes in, it needs to be inspected.
01:27 - 01:43
It was very tedious. There was no way of tracing the documentation when it was generated. There was no way to link anything. Somebody would have to literally sit down and go through a file cabinet to figure out what had what had gone on. It was just non workable, especially for a company that had at the time like seven people.
01:43 - 02:12
Like, what are you going to do, have three of your employees looking at a file cabinet? All that and it just wasn't going to happen. The so where Unifize came in and and we we did go from pen and paper to Unifize was that it procedure realized all of our processes right you know you can if you just have a pen and paper you can kind of and a you know, skip your way through a bunch of stuff that becomes tedious but Unifize it.
02:12 - 02:31
You are specifying a process that you have to follow every time. And that consistency helps, right? Whenever I'm looking back on something that's been done, if I'm looking at, say, our receiving inspector's comments on our material that we have, I know that it's going to be in the same format every time, which is it's nice. It's good to be able to go back and look at that.
02:31 - 02:58
The other thing is that the ability to link different quality system activities together helps tell the story of our product as it's being made. And so I can go back and look at the history of, you know, if we're trying to diagnose the root cause of some process issue, I can look through and find where that was. You know, it's like we have a virtual router that follows our parts and our device around until it gets into the field.
02:58 - 03:12
I think that that's something that's really invaluable about Unifize. And I think that it's probably the biggest benefit over our old system, which was once again, pen and paper.
Managing Product Lifecycle with Unifize

Customers
Denis's experience with Unifize: Revolutionizing quality assurance systems
Quality expert Denis details his transformative journey with Unifize. He praises its efficient design, user-centric approach, and the system's ability to streamline data handling and accelerate time to market.
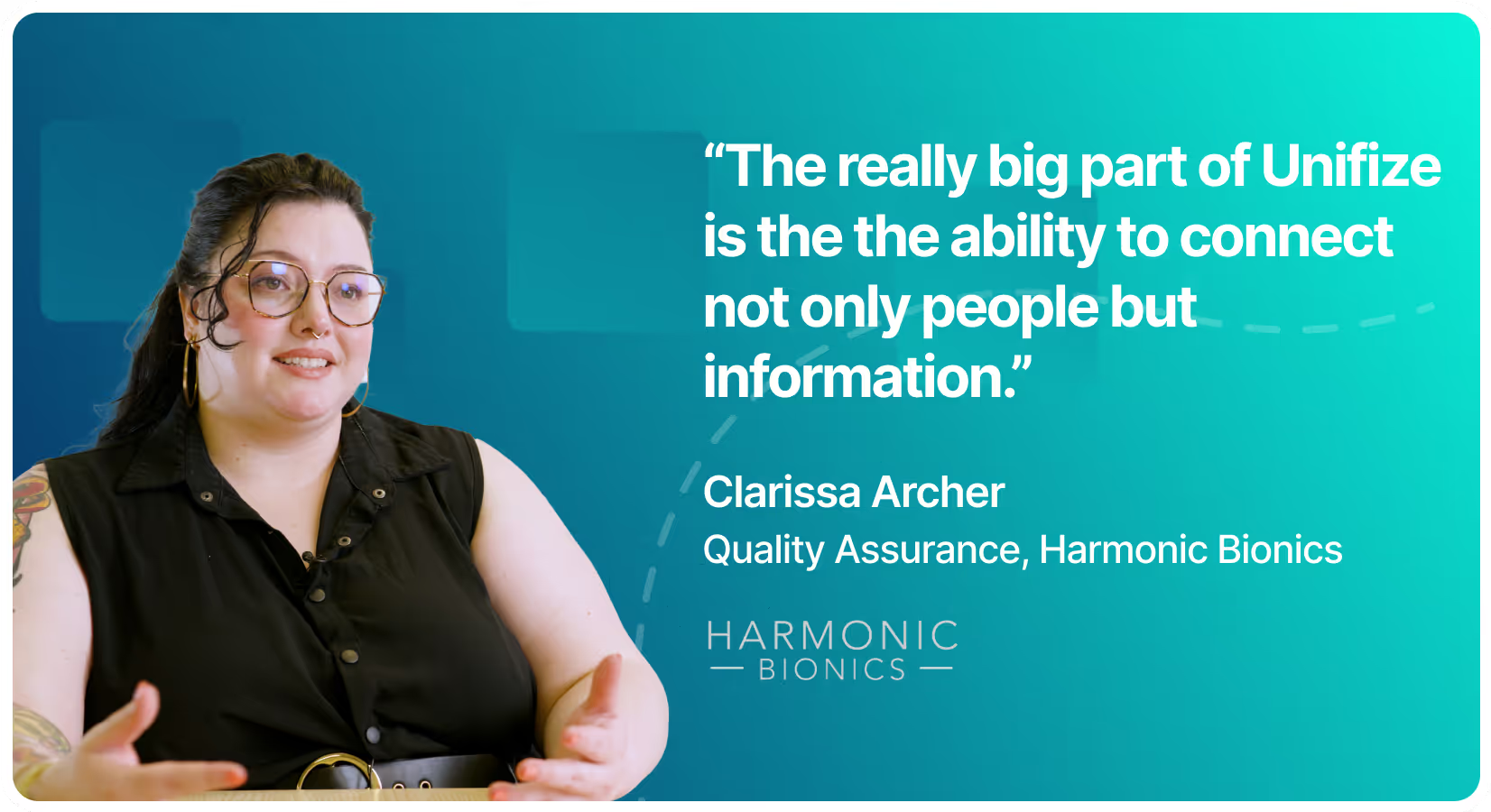
Customers
Harmonic Bionics and Unifize: A seamless transition to regulatory compliance
Clarissa Archer shares her experience integrating Unifize into Harmonic Bionics, underscoring its value in streamlining change control, facilitating communication, and ensuring robust documentation for regulatory compliance in the medical device sector.
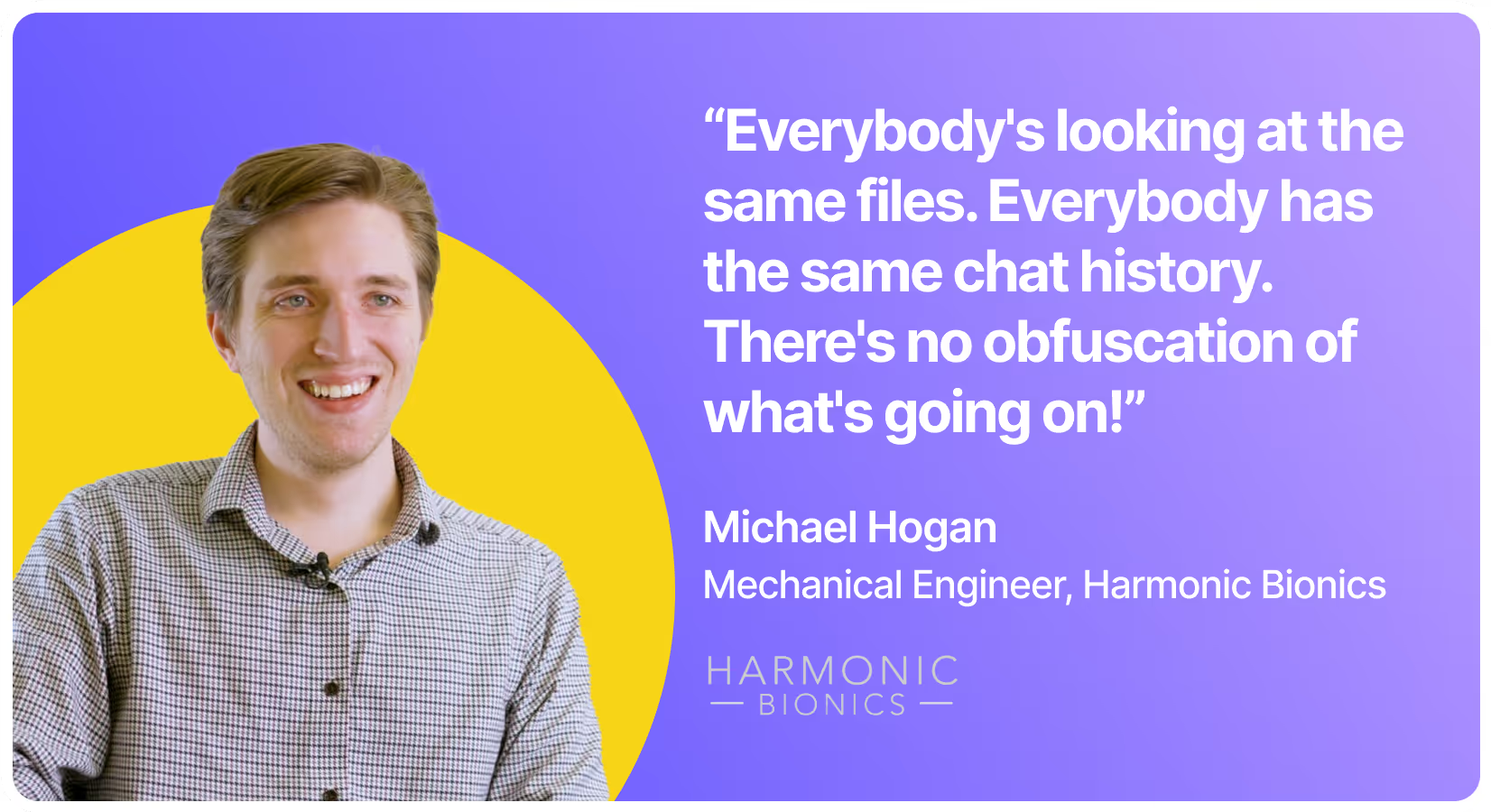
Customers
Engineering efficiency with Unifize: Michael Hogan's insights from Harmonic Bionics
Mechanical Engineer Michael Hogan elaborates on how the integration of Unifize at Harmonic Bionics has streamlined his engineering processes, promoting transparency and rapid turnaround in the medical device domain.
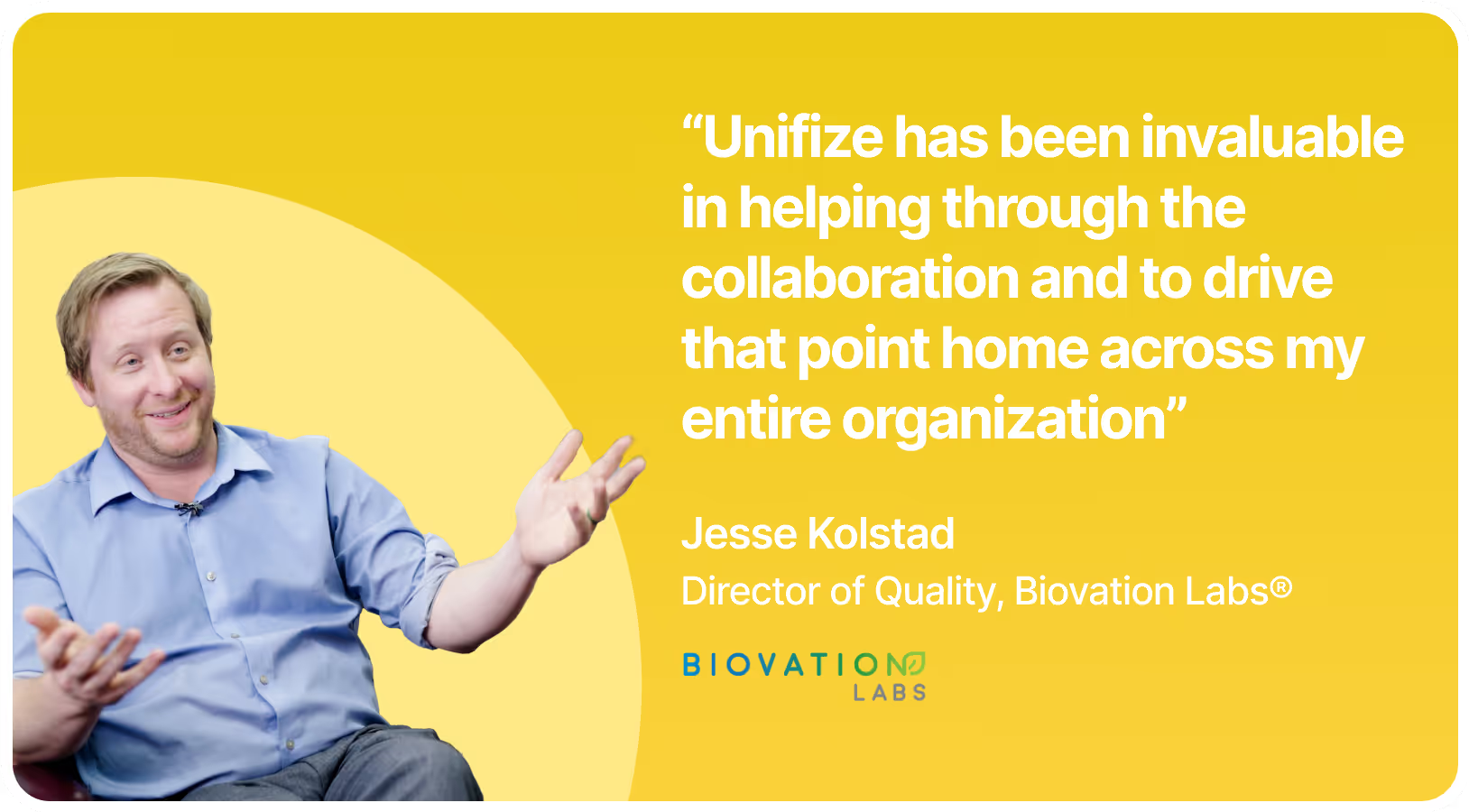
Customers
Here’s how Biovation Labs reduced testing costs from $146K to $65K in two months
Learn how and why Biovation Labs, an FDA regulated nutraceutical manufacturer based in Salt Lake City, took the decision to transition from MasterControl to Unifize for their product lifecycle (PLM) and quality management (QMS) processes.
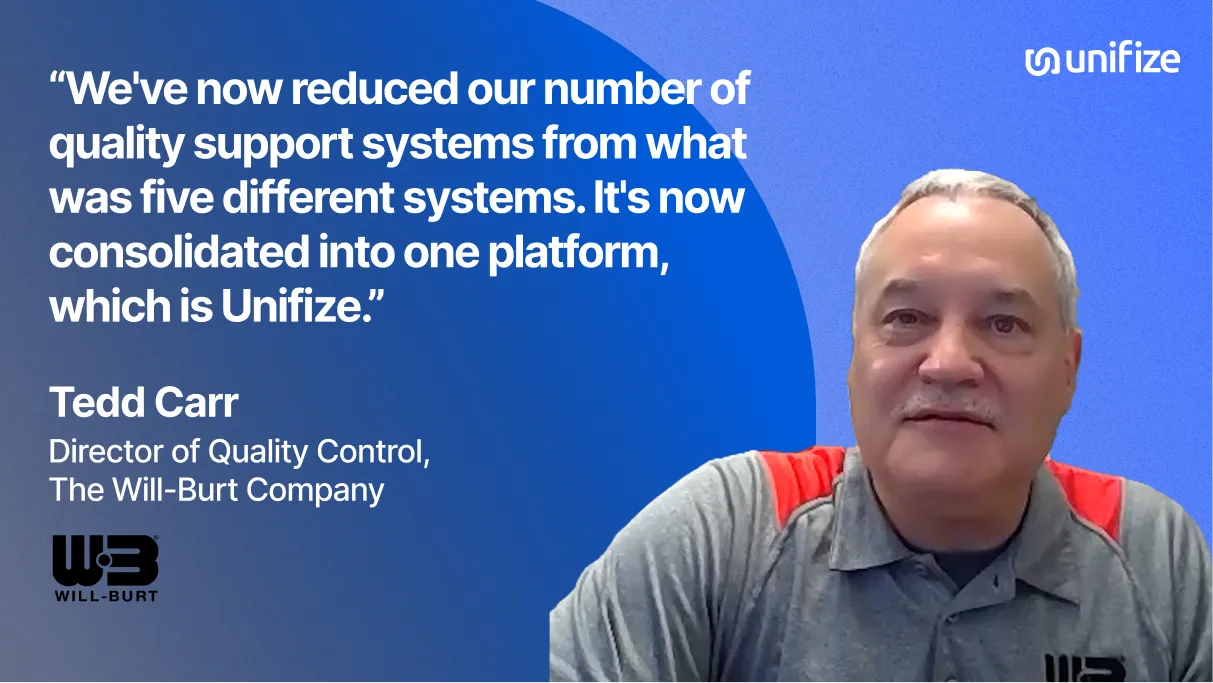
Customers
How a quality veteran from boosted issue closure time by 75% within the first month
Tedd Carr from The Will-Burt Company discusses overcoming their diverse and complex quality challenges across various sectors with Unifize. By consolidating five systems into one, they achieved clear accountability and reduced issue closure from months to days, demonstrating significant efficiency gains and faster decision-making in their quality processes.