Clarissa Archer, with a decade in medical device engineering, serves as a quality assurance engineer at Harmonic Bionics. Her expertise in regulatory compliance guides the transition from research to market-ready innovations, streamlining processes within cutting-edge robotic rehabilitation solutions.
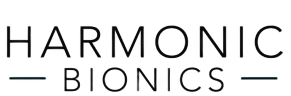
Overview
Clarissa Archer, a Quality Assurance Engineer at Harmonic Bionics, shares her insights on how Unifize has significantly streamlined compliance and documentation processes in the context of rigorous FDA standards.
Challenge
Joining a research-focused startup with a shift towards medical device compliance, Archer encountered the daunting task of bridging gaps in change control and documentation. The existing systems were cumbersome, involving lost documents, physical signatures, and inefficient communication that could not support the dynamic needs of a small, fast-paced company.
Solution
After evaluating several quality management systems (QMS), including paper-based and other digital solutions, Harmonic Bionics chose Unifize for its customizable nature and ability to handle comprehensive compliance needs such as electronic signatures in line with 21 CFR part 11.
Ease of Use
Unifize stood out for its user-friendly interface, allowing Archer and her team to configure the system to their specific needs rather than contorting their processes to fit the software. This flexibility was crucial in organizing Design History Files (DHF) and other critical documentation.
Communication and Collaboration
The platform revolutionized internal communication, centralizing discussions and feedback within Unifize, thus reducing the reliance on emails and informal chats that could lead to lost or forgotten information.
Documentation and Compliance
Unifize's ability to produce clean, comprehensive PDFs with complete audit trails empowered the team to present coherent and precise documentation during audits, displaying the rationale behind each decision and action taken.
Results
With Unifize, Harmonic Bionics experienced a transformation in how change requests and orders were managed, condensing weeks of work into mere days. The engineers quickly adopted the system, recognizing its potential to maintain compliance while still moving at the desired fast pace.
Professional Preparedness
The detailed record-keeping and history provided by Unifize allowed Archer and her colleagues to answer auditors' questions confidently and promptly, without the frantic scramble for information that was previously the norm.
Regulatory Alignment
Unifize not only streamlined FDA compliance but also aligned with ISO standards and IEC regulations relevant to the medical device industry, demonstrating its comprehensive applicability.
Conclusion
Unifize has become an indispensable tool at Harmonic Bionics, enhancing compliance, simplifying documentation, and ensuring that all team members are aligned and informed. The platform's adaptability and ease of use have made it a cornerstone in the company's shift towards regulatory focus, proving that speed and compliance can coexist in the fast-evolving world of medical robotics.
Yeah, when you have the big scary FDA people or whoever coming out, you have everything that you need and the whole source of truth right there in writing, you're able to say, “Here's why we made those choices and here's what those choices were”.
[00:14 - 00:33]
you have the ability to print it out on a PDF so you can show them, here's the final product. All the sins are hidden, but they're able to be there so that you remember, when you're being asked very specific questions that, two years from now when you're audited, it's really easy to forget why you made one specific choice.
[00:33 - 00:51]
And so being able to have that conversation there and that history is huge because then you present them with the nice PDF that Unifize makes for you with the whole audit trail, everything you need. And then you have like the less formal conversation that you can look back on and when they say, why did you make these choices?
[00:51 - 01:21]
And you kind of look and you're like, Oh yeah, of course I forgot about that, there was an error. There was, you know, a trending issue with some non conformance. And here's why we made those choices. And you can come off very professional prepared without having to say, let me look into that and furiously typing over at the people in the back room who are flipping through papers, freaking out. You have it all there.
[01:21 - 01:55]
So my name is Clarissa Archer. I am a quality assurance engineer at Harmonic Bionics, and I've been here for just under a year. But prior to that, I've worked at other medical device companies, and so I've been working in the medical device for about ten years now. Harmonic Bionics is a startup company that focuses on robotics, our primary robot is Harmony SHR, and that is to help people with either neurological impairments or muscular impairments rehab their shoulder.
[01:55 - 02:33]
And so we have to follow the FDA 21 CFR 820, it's not required by the FDA to follow ISO 13485 or 14971 or ISO 9001, but those are heavily recommended. And so we also try to follow compliance to those ISO standards. I think we also looking at IEC 60601 62304 from like a software and robotics side. Now, when Denis and I first started around the same time about a year ago, we were coming into an organization that was primarily research focused with not a lot of individuals who had medical device experience necessarily.
[02:33 - 02:54]
And so we noticed a lot of gaps in what would be needed in order to take our company from research focus to medical device compliance focused, regulatory focused. And so with that involved, noticing those gaps was, you know, there was a lot of focus on change control and documentation.
[02:54 - 03:35]
But there was difficulty in the communication of change control and actually documenting what changes were being made. And of course there is documentation being lost having to be rewritten because it was lost we had some individuals who were working remotely or from different areas who were in different states having to come down and physically sign something or use DocuSign or something like that, that was a big pain point for us. in looking for a new QMS, you know, we looked at several options, one of which was paper based still, using SharePoint, using paper and revamping that whole system
[03:35 - 04:08]
when we just decided pretty immediately that that wasn't going to work, especially with such a small company wanting to be able to collaborate better. You know, we looked at several other systems and primarily we looked at what modules were available. Were they able to handle change control? Were they able to handle product lifecycle management? 21 CFR part 11 So electronic signatures, that cut out a few options that we had originally looked at because we needed something that was compliant to electronic signatures,
[04:08 - 04:44]
So we looked at different companies such as Master Control, ETQ, Greenlight Guru, and they all kind of had the same sort of package that we were looking for, but there was something quite missing from them. you know, we also wanted to look at ease of use, the user interface that was really important to myself, being able to organize like a DHF within a program, from my prior company. I had previously used Agile and, you know, with a lot of different systems that aren't really configurable, you have to kind of work against the machine to create what you need.
[04:44 - 05:05]
What I really enjoyed about Unifize is the fact that we could configure the program to be what we needed it to be rather than trying to work against a program to make it fit into what, for example, we'd want a Design History File to look like we were able to configure Unifize to design it, how we needed it and how we wanted it.
[05:05 - 05:27]
Being able to communicate with others via Unifize was really useful because, you know, in other programs and other companies, there's a lot of emails, watercooler chats, messages, and there's a lot of stuff that can kind of get lost or, Oh, hey, I wanted you to add this, that and the other, or you know, sending feedback.
[05:27 - 05:40]
And then when it comes, you know, two weeks later when that feedback is done and I'm re-reviewing a document and I'm trying to go okay what did I tell them to do in the first place. I'm constantly working on several different projects at a time
[05:40 - 06:00]
and so being able to go into Unifize and see that and see the conversation and say, Oh yeah, I wanted them to add this detail here or change this up, that is so useful in order to be able to not only keep track of everything that's going on per item, but to make sure that we're all on the same page.
[06:00 - 06:43]
Having the Unifize team discuss and show the engineers how to use it, they really adopted it pretty quickly and were able to notice like, Oh wait, previously I had to do a change request and then a change order and all of this. And it would take three weeks to implement, from beginning to end. Now it can take a couple of days. that really helped with the adoption and the understanding that, yes, we can still move fast, but we need to move fast in a compliant way. And so making it easier to document changes and to document these things, I think really took out a lot of the pain of having to document it in the first place.
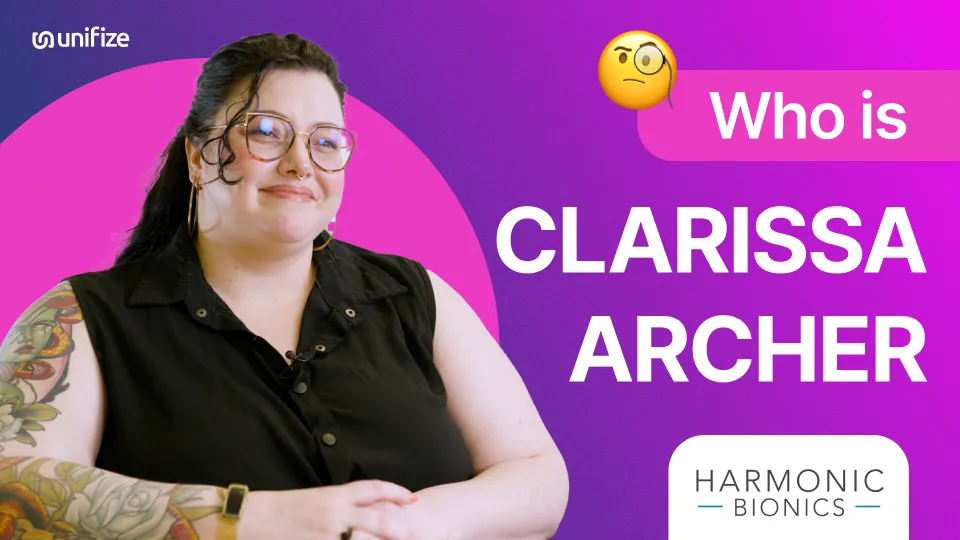

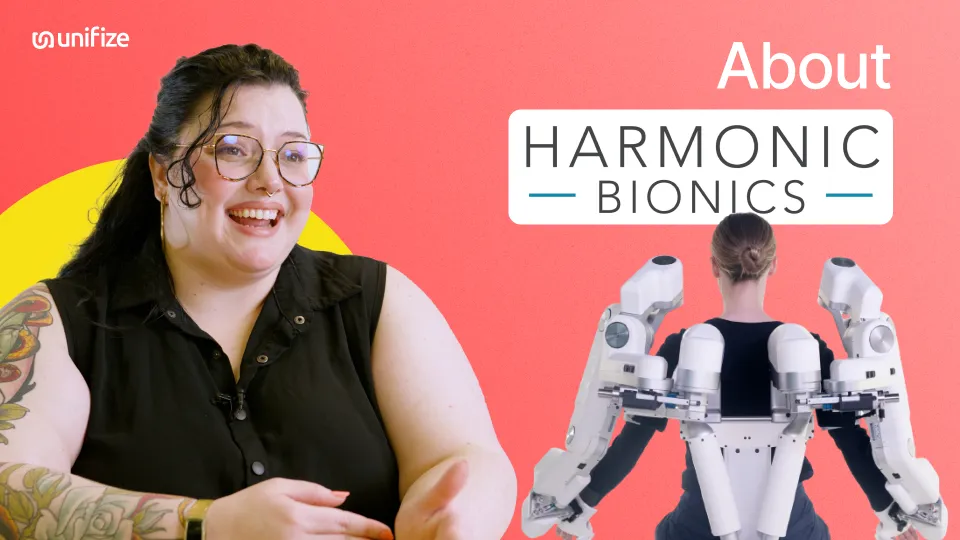

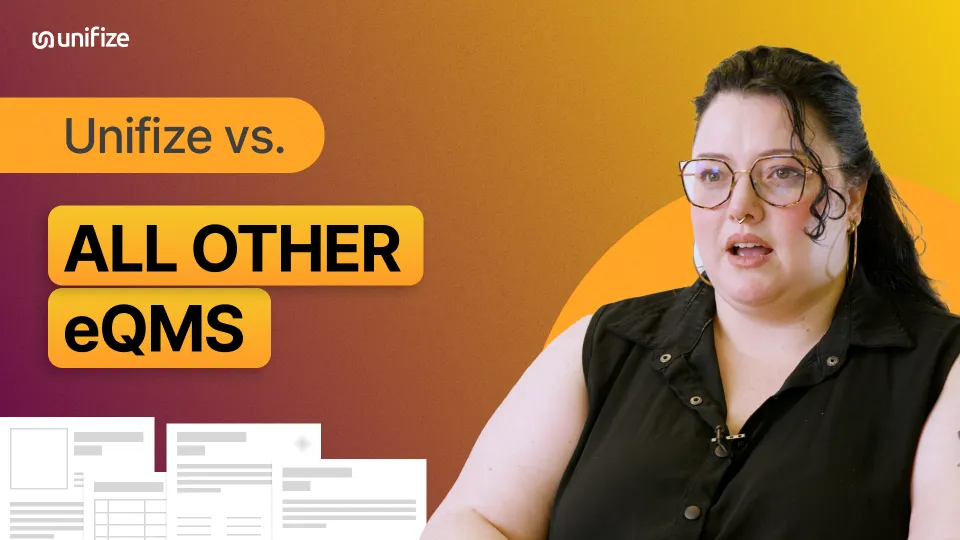

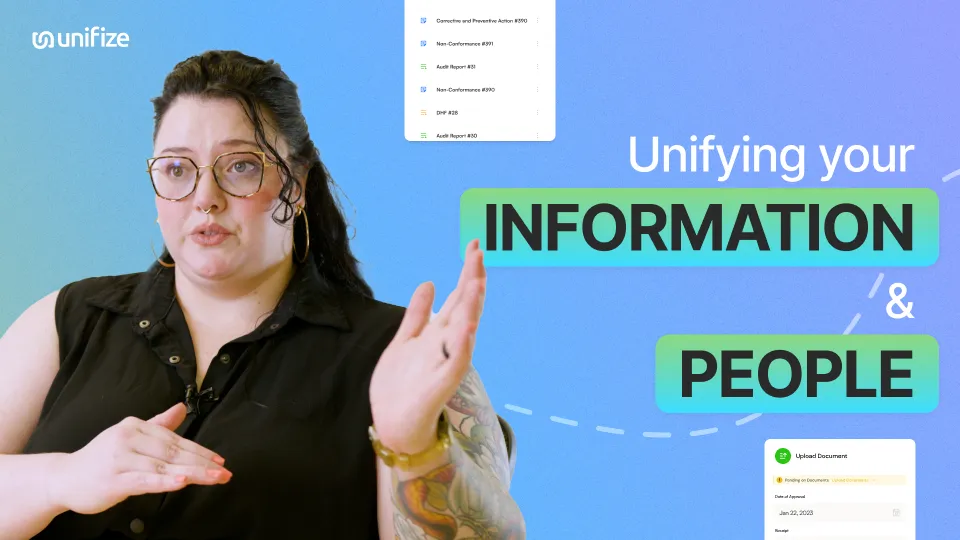

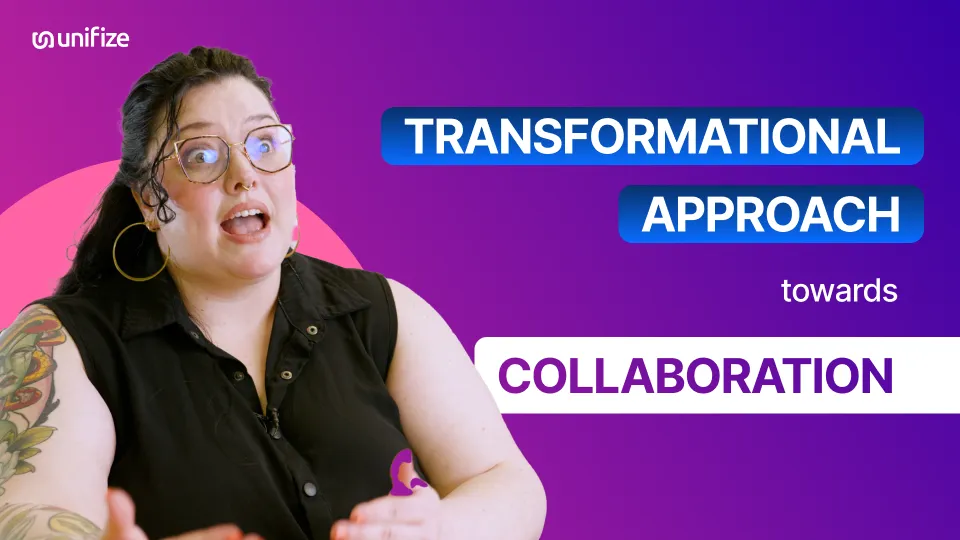

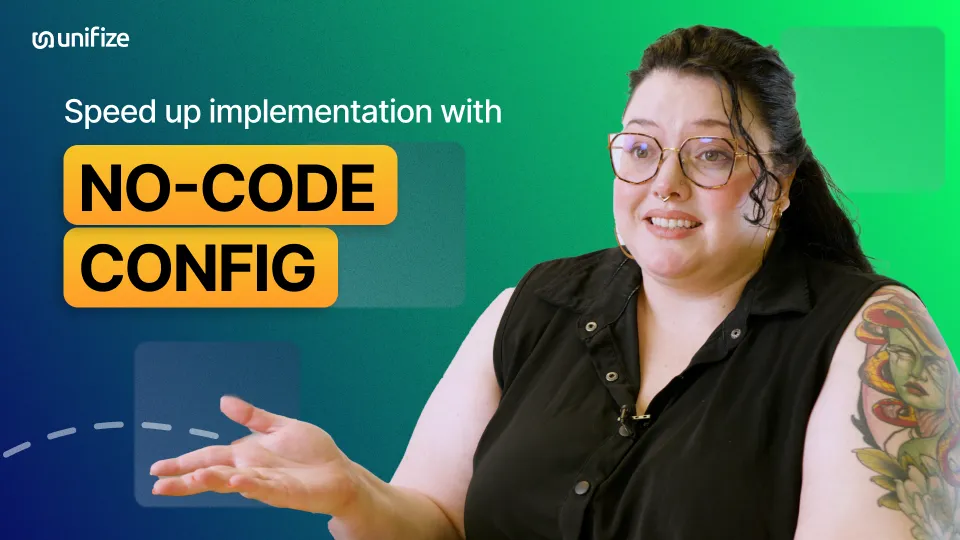



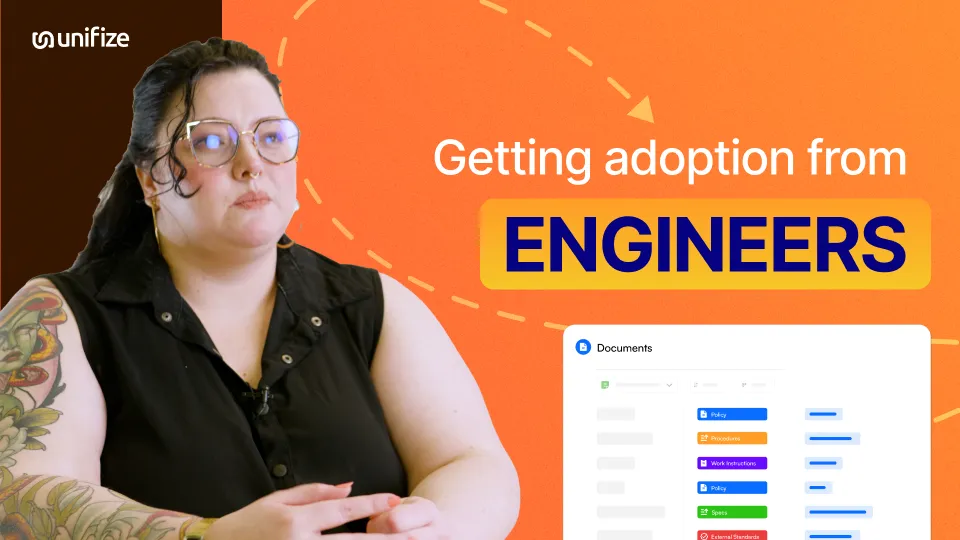

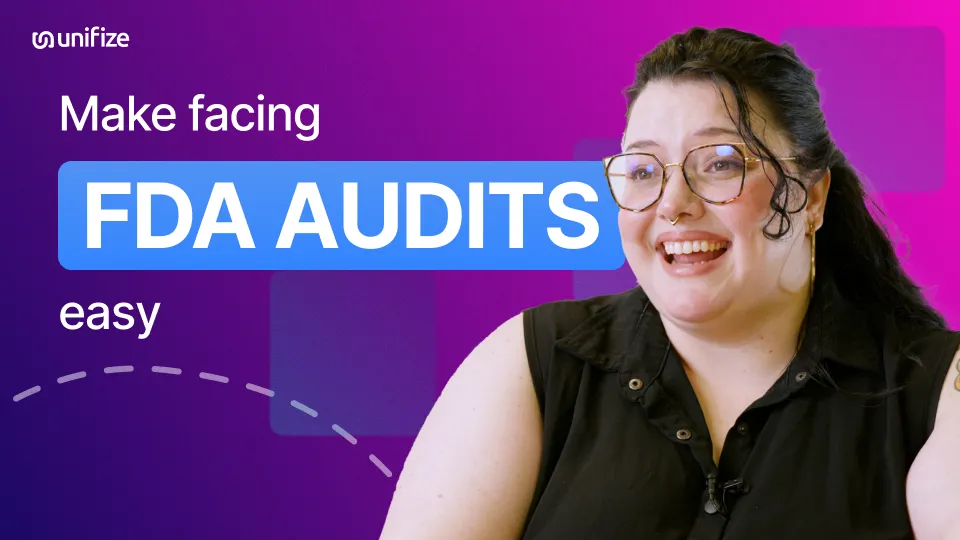

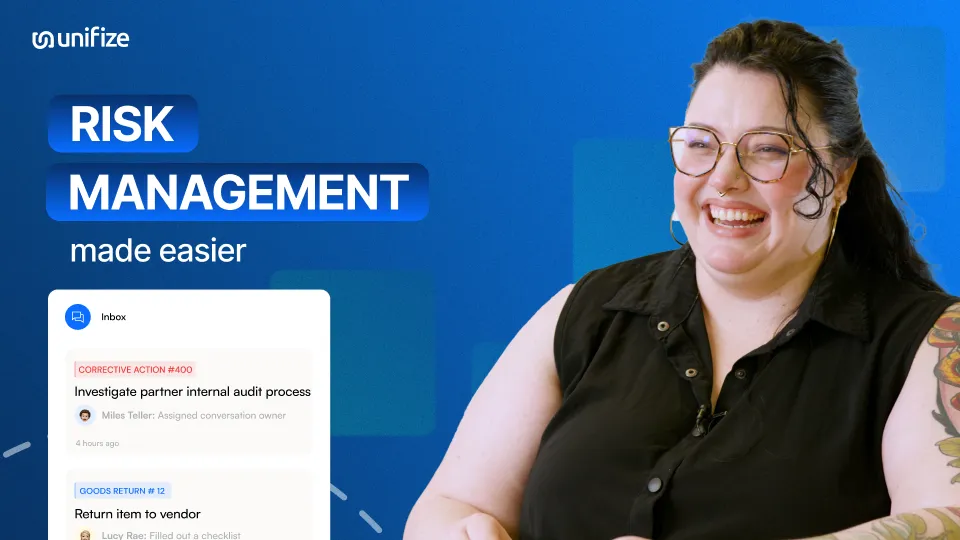

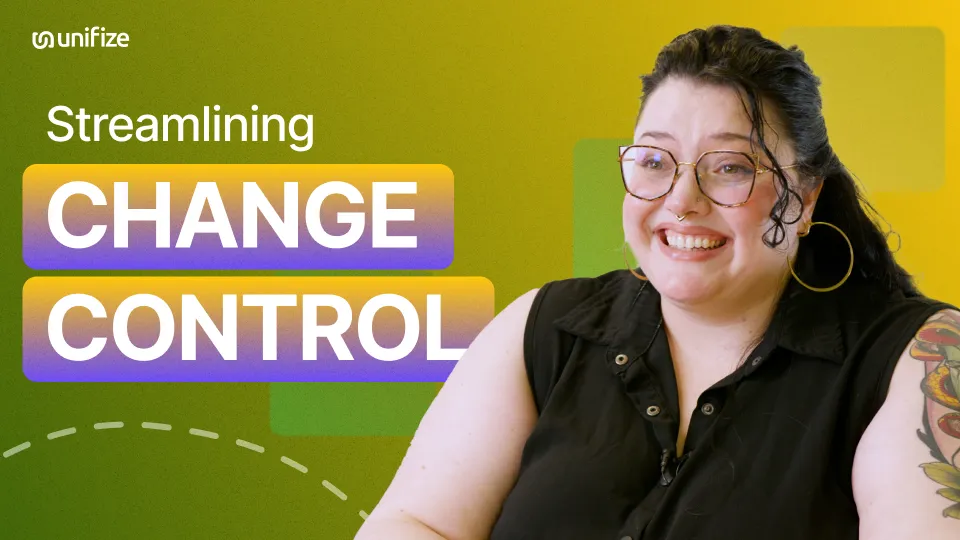

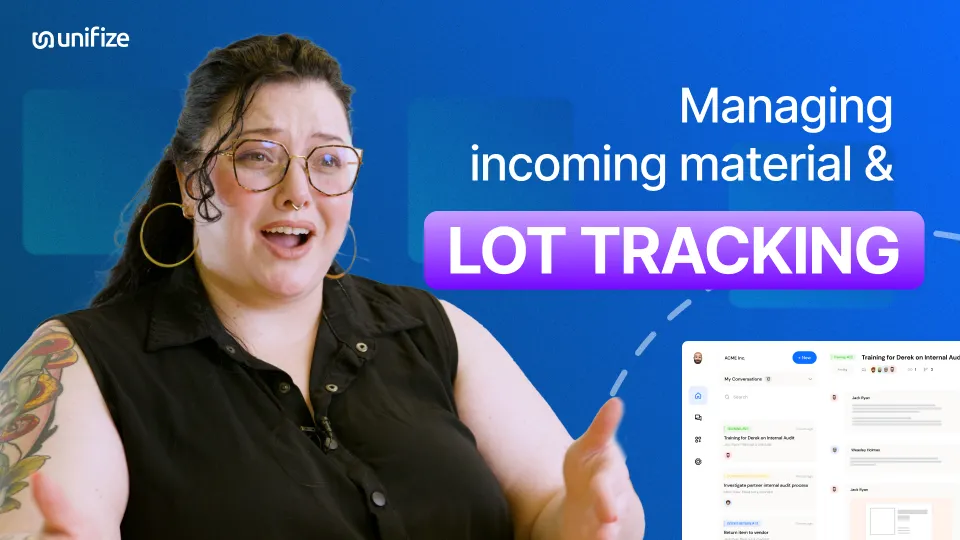

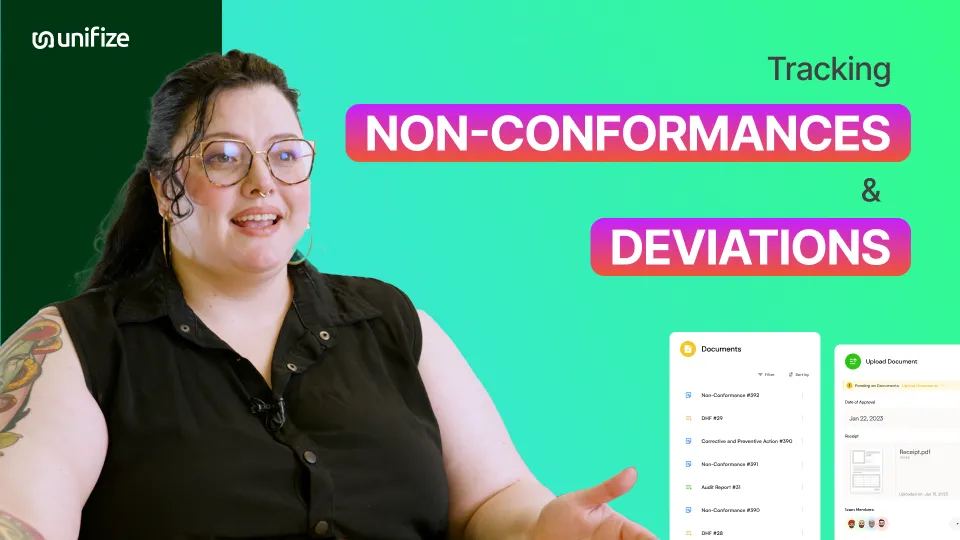

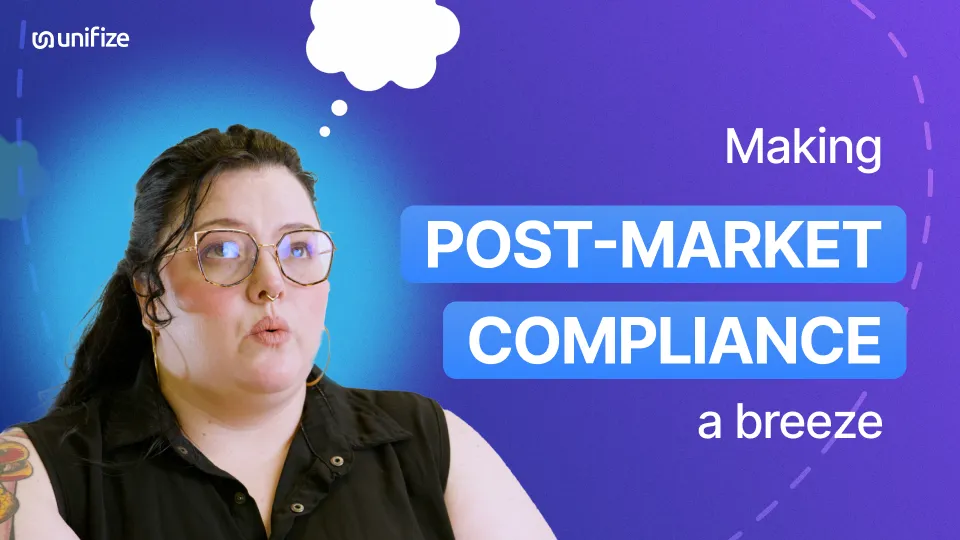

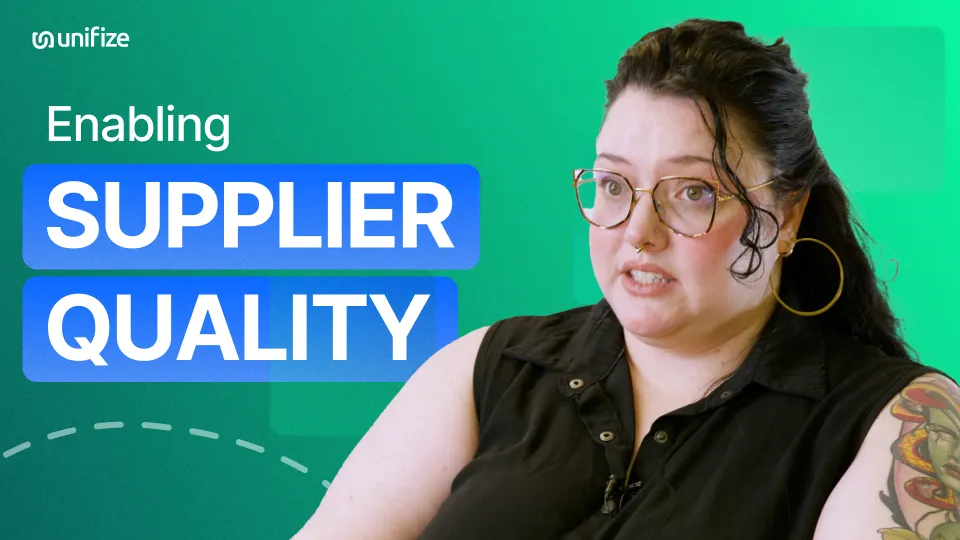

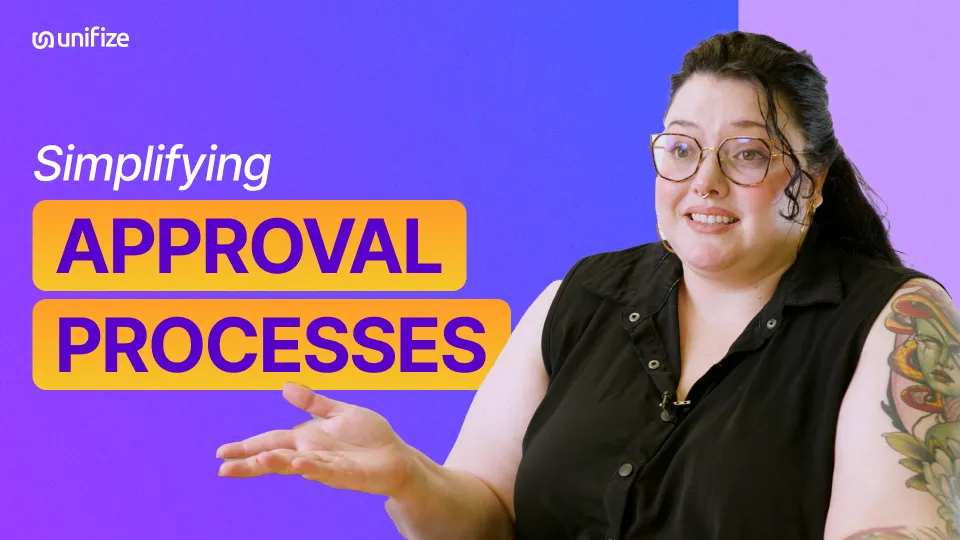

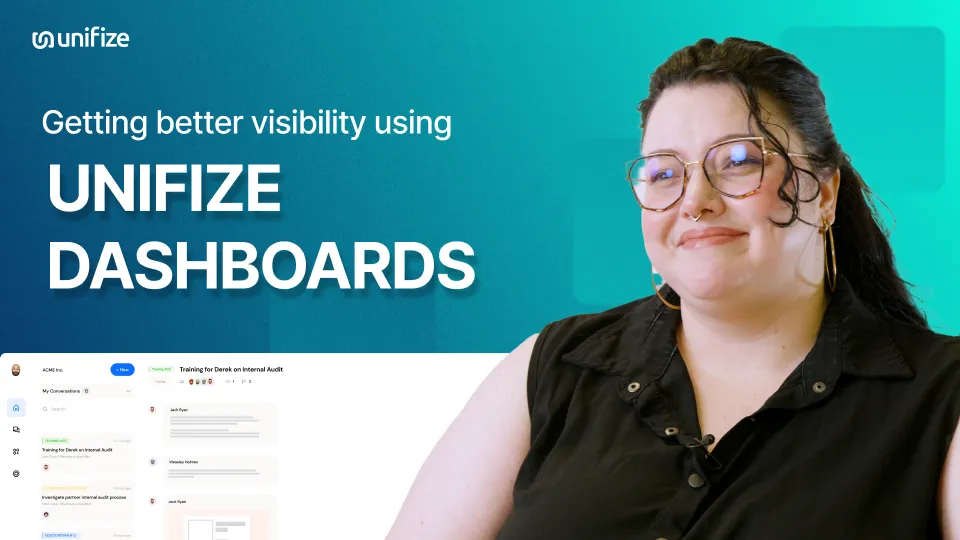

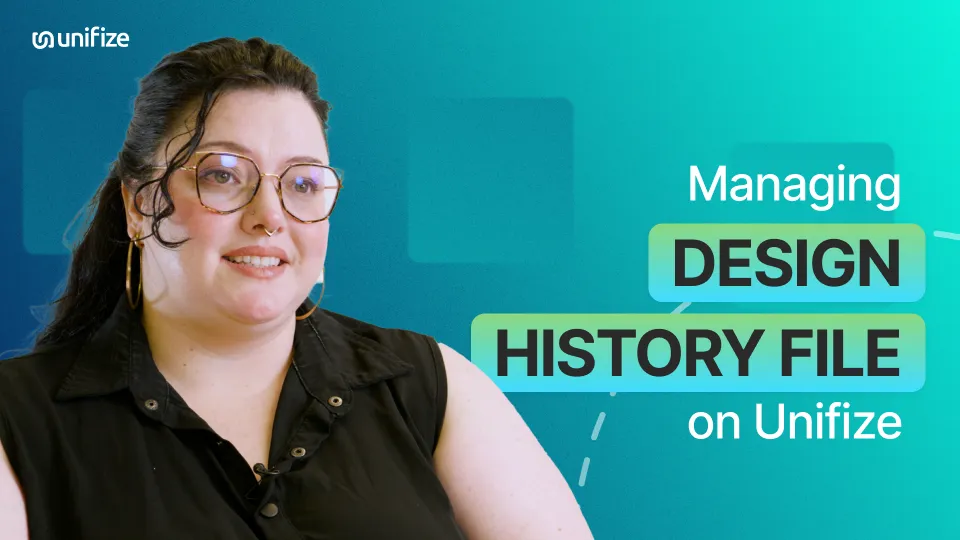

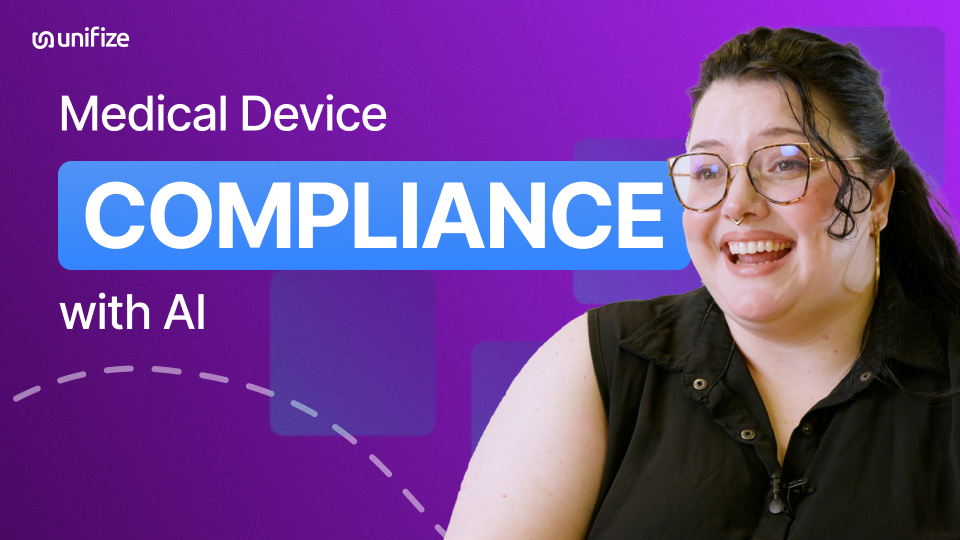

More from Clarissa Archer
Unifize Results
Speed to compliance
Faster time-to-market
Fewer meetings