Content Library
00:00 - 00:20
I'm a Six Sigma certified Six Sigma black belt. And because of my background or my training, what I do is transformational. I do a lot of transformation of companies. One of the things that I do and I typically try to do is look at an organization and determine what is the best way to achieve the results of the organization and to build that culture.
00:20 - 00:26
First of all, is to understand where the company is, what is the status of the company and where they want to go.
00:26 - 00:37
There are certain things that may work in one company, but may not work in another company. So I typically try to identify what that meant or the easiest way to communicate what the new transition ought to be.
00:38 - 00:53
Communicating that intent is really important. So methods of communication and how people relate culture basis is really going to determine that. The next thing that I try to do to build that culture is to have the tools that assist in building that culture.
00:53 - 00:59
If you want a culture of knowledge, you have to have tools that allow you to have access to that knowledge.
00:59 - 01:22
If you need a culture that allows for collaboration, then you need to build tools that allow for that type of collaboration. It's hard to build a culture if your tools are not supporting that. And so leverage what is available, you know, if you go to an organization, look at an organization and see what type of tools are available to allow you to build a culture that you try to build, the next thing is build, be deliberate.
01:22 - 01:38
A lot of companies look at cultural elements and how to build a quality organization is something that happens. It's deliberate. It needs to be deliberate. Most companies who have succeeded in building that do things deliberately to try and make it happen.
01:38 - 01:40
I tried to be deliberate as much as possible.
01:40 - 01:56
At Harmonic, one of the things that we did is create a culture of sharing information. We created a mission, a mission that specifically put the culture of improvement and the culture of thinking about quality forefront in everything that we wanted to do.
01:56 - 02:16
So we created a mission statement, a vision statement. Everybody participated in our Kaizen as we call it, and we decided that we are going to be deliberate about our actions. We did things that are human centric, things that allowed us to collaborate. We leverage tools that allowed for that collaboration.
02:16 - 02:24
We were also very deliberate in the items that we talked about. What were the things that drove the company forward?
02:24 - 02:50
What were the pain points? Those were brought up. We were willing to listen to feedback. That's really important. We wanted to get a feedback of how we were doing and we became the beacon of this is how we are going to do this. If the company can hold us accountable to all the things that we wanted to do on our mission vision statement and we stood in front of it being deliberate and saying, This is what we stand for.
02:50 - 03:17
One of the other things we did is increase the knowledge. We tried to improve our knowledge. When you improve the knowledge of the organization, you will find out that people start in giving back that feedback, understanding what the regulations needed, what we were doing about it, where our gaps were, and we deliberately started doing things that we needed to do as part of meeting that challenge.
03:17 - 03:34
At Harmonics, one of the challenges that we had is knowledge level. Harmonics is a startup company. It's a very young company, and as a result of that, there was a gap in terms of expectations, in terms of building that core knowledge that you would expect.
03:34 - 03:50
Most of these other companies, you see mature organizations having competent people, having people that have been in industry for many years. When you go to start up with small and medium size companies that are starting out or may need to go in, you have to argument that level of knowledge.
03:50 - 04:02
One of the things that we did was deliberate trainings. Kaizens sharing knowledge, expectations, talking about regulations, presenting all those activities. And that's what we did.
04:02 - 04:14
Unifize was a big part of this because Unifize was one of the tools that we use for collaboration, Unifize put everything together. It was easy to follow organizations, it was transparent.
04:14 - 04:36
Whenever you want to make change you need to know what the changes it needs to be transparent, it needs to be visible, and it is to be visible to the right people, right? So it's not just a matter of being visible too. We know a few that need to have it, but there are others who may be viewing that information and being influenced by what is happening in that level.
How Denis builds a quality culture in MedTech companies

Customers
Denis's experience with Unifize: Revolutionizing quality assurance systems
Quality expert Denis details his transformative journey with Unifize. He praises its efficient design, user-centric approach, and the system's ability to streamline data handling and accelerate time to market.
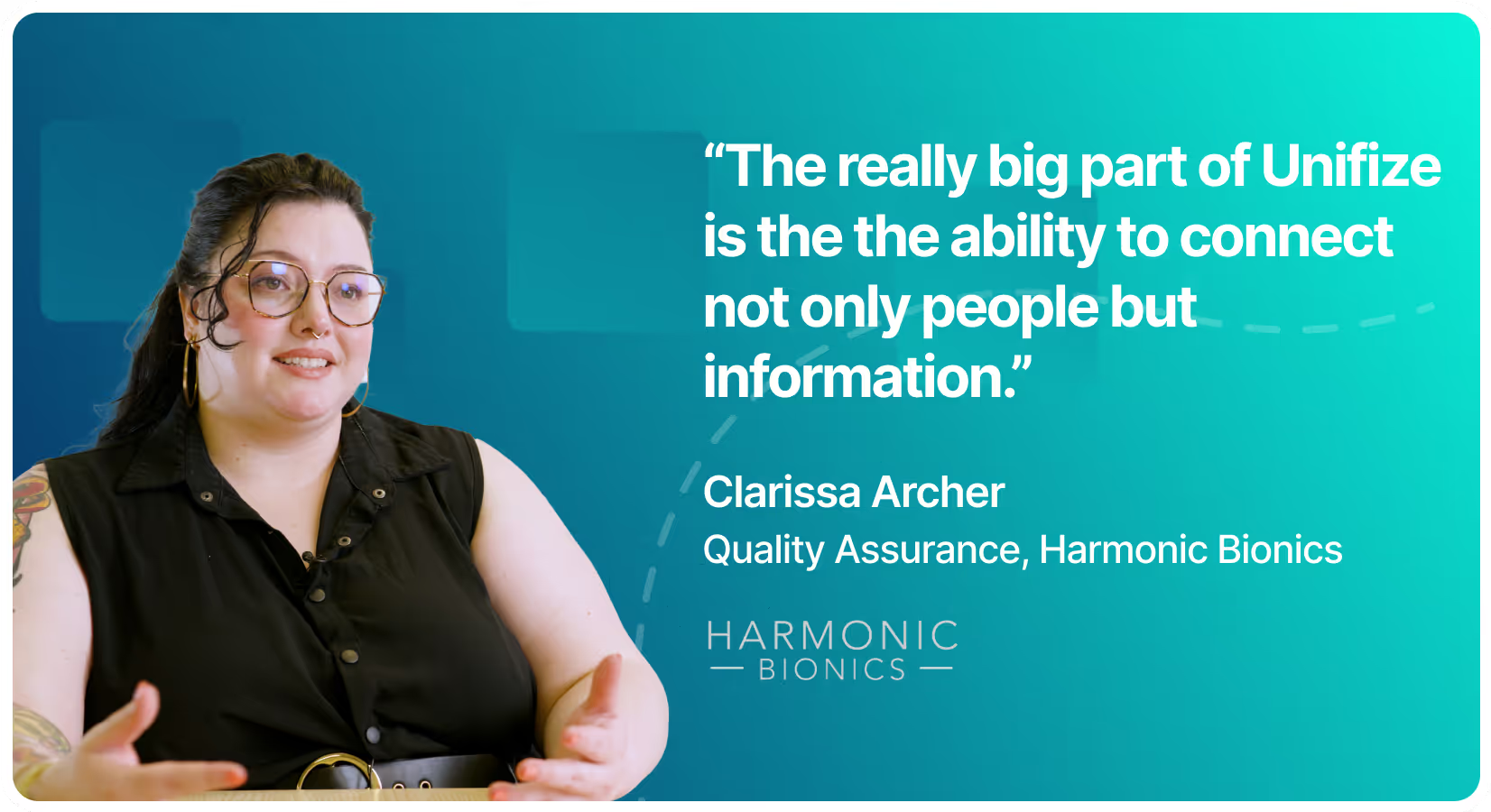
Customers
Harmonic Bionics and Unifize: A seamless transition to regulatory compliance
Clarissa Archer shares her experience integrating Unifize into Harmonic Bionics, underscoring its value in streamlining change control, facilitating communication, and ensuring robust documentation for regulatory compliance in the medical device sector.
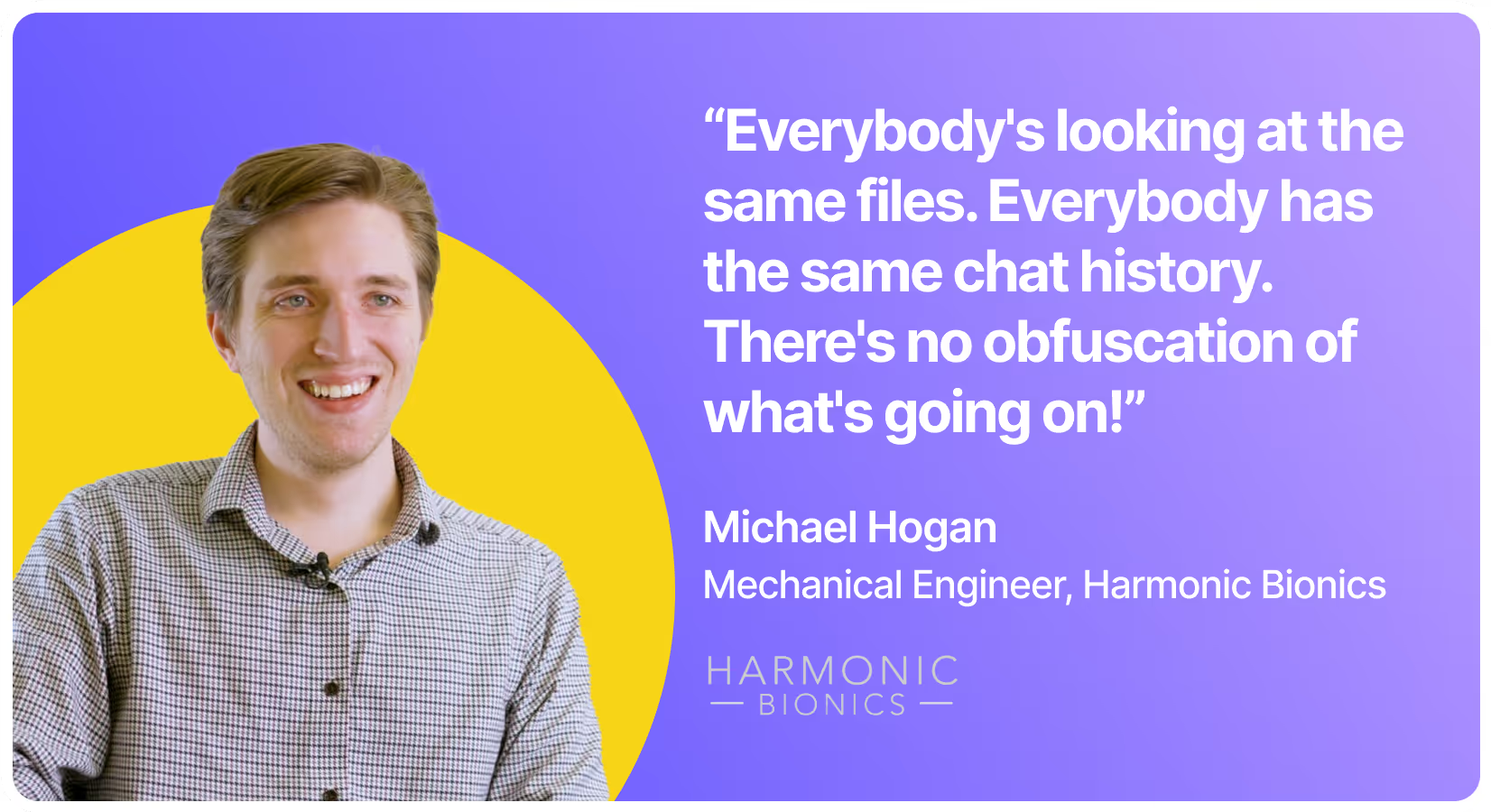
Customers
Engineering efficiency with Unifize: Michael Hogan's insights from Harmonic Bionics
Mechanical Engineer Michael Hogan elaborates on how the integration of Unifize at Harmonic Bionics has streamlined his engineering processes, promoting transparency and rapid turnaround in the medical device domain.
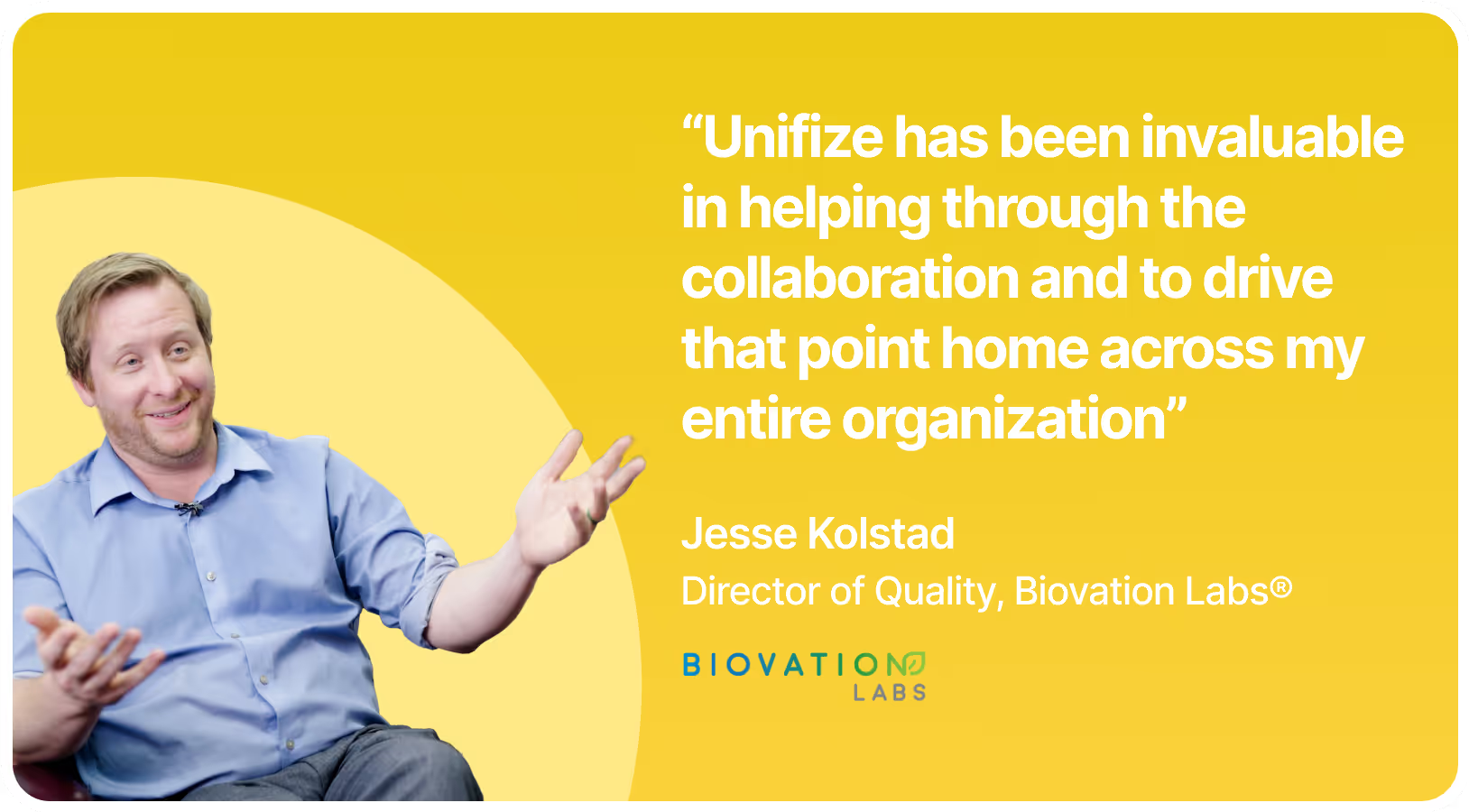
Customers
Here’s how Biovation Labs reduced testing costs from $146K to $65K in two months
Learn how and why Biovation Labs, an FDA regulated nutraceutical manufacturer based in Salt Lake City, took the decision to transition from MasterControl to Unifize for their product lifecycle (PLM) and quality management (QMS) processes.
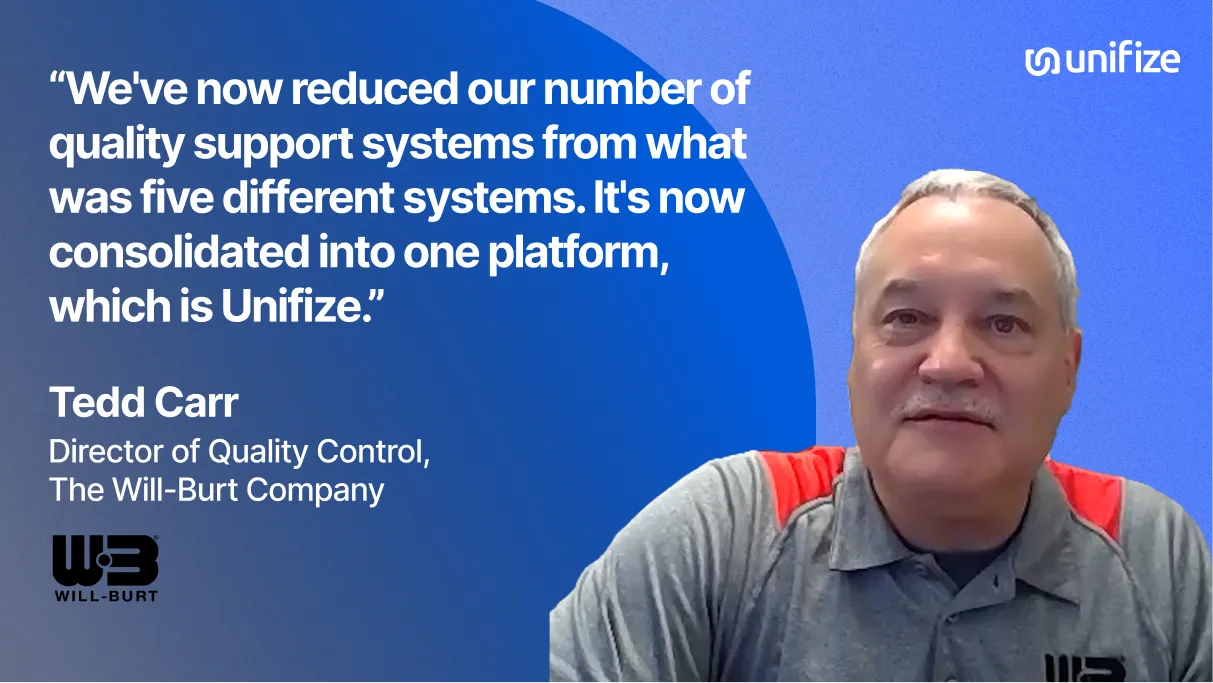
Customers
How a quality veteran from boosted issue closure time by 75% within the first month
Tedd Carr from The Will-Burt Company discusses overcoming their diverse and complex quality challenges across various sectors with Unifize. By consolidating five systems into one, they achieved clear accountability and reduced issue closure from months to days, demonstrating significant efficiency gains and faster decision-making in their quality processes.