Content Library
00:00 - 00:09
When you're operating a very manually intensive quality management system, change control was always a very big part of any obviously the fundamental aspect of any quality management system.
00:09 - 00:24
You need change control in order to ensure that whatever changes you're making to a process, a documented process, is being not just documented but also approved and in line with the requirements of your quality management system.
00:24 - 00:47
For us, utilizing Microsoft Word to try to make a functional change control system was always as the business grew and as more and more opportunities for improvement were identified, having to open up a template in Microsoft Word input all the changes into that document then find where the same SOP was.
00:47 - 00:57
I have net open tracking those changes in the SOP, trying to communicate what those changes actually looked like between the old and the new to the people with approval authority.
00:57 - 01:08
It became a big mess because you just hand say, department head here's the change control, here’s the list of 30 different changes are made to this operating process.
01:08 - 01:18
Here's the SOP document outlining all these changes with all these red lines and corrections that all throughout the document, you kind of have to figure it out.
01:18 - 01:27
Approver had to figure out what they were even looking at in the first place before they can even understand why the change was necessary and how can actually improve a process.
01:27 - 01:39
That was the way things worked before. And so because the process was so onerous, less and less people wanted to go through change control in order to document improvements to anything going with the core business process.
01:39 - 01:53
Now with Unifize, it makes it a lot easier because now the change on the Unifize platform, the change control, you could tie the doc to SOP from the document section module into the change control form itself.
01:53 - 02:09
So it's always tied together. So anytime you need to reference that when going back and forth, you can look at the correct revision of that document in relation to the change control and it's all there in a single place. It's not three, four, five, six, seven, several different files that you're trying to juggle in within a single change control.
02:09 - 02:31
So the fact that it's all tied in you can loop in everyone involved that gets affected by that change into the conversation next to the actual change control document and had the discussion right there and update the change control document as a conversation is occurring, and it makes the whole process significantly more efficient because you don't have to have the two or three requisite meetings to get people updated.
02:31 - 02:51
You don't have to explain to people why the change control is laid out in a certain way, why those changes, how those changes should be interpreted based on your writing style and your your understanding of the context. All that's all being done in the same place. And so change control now is just a lot more efficient and less of a headache for us because it's all right there.
02:51 - 02:59
And as a result, our team is more readily and willing to utilize a quality management system the way it's supposed to work.
02:59 - 03:07
Change control request sometimes just like any other document that requires an approval, sometimes can linger on because documents just fall through the cracks.
03:07 - 03:16
And we've had change control requests that would linger on for three to six months. Sometimes just because no one was actively managing that portion of the SOP.
03:16 - 03:34
And so we just remove that outcome from the quality management operation completely and have that reduced to just two weeks and having everyone informed about what was going on with that change control without having additional updates and meetings and emails has been a breath of fresh air for us.
Change control with Unifize

Customers
Denis's experience with Unifize: Revolutionizing quality assurance systems
Quality expert Denis details his transformative journey with Unifize. He praises its efficient design, user-centric approach, and the system's ability to streamline data handling and accelerate time to market.
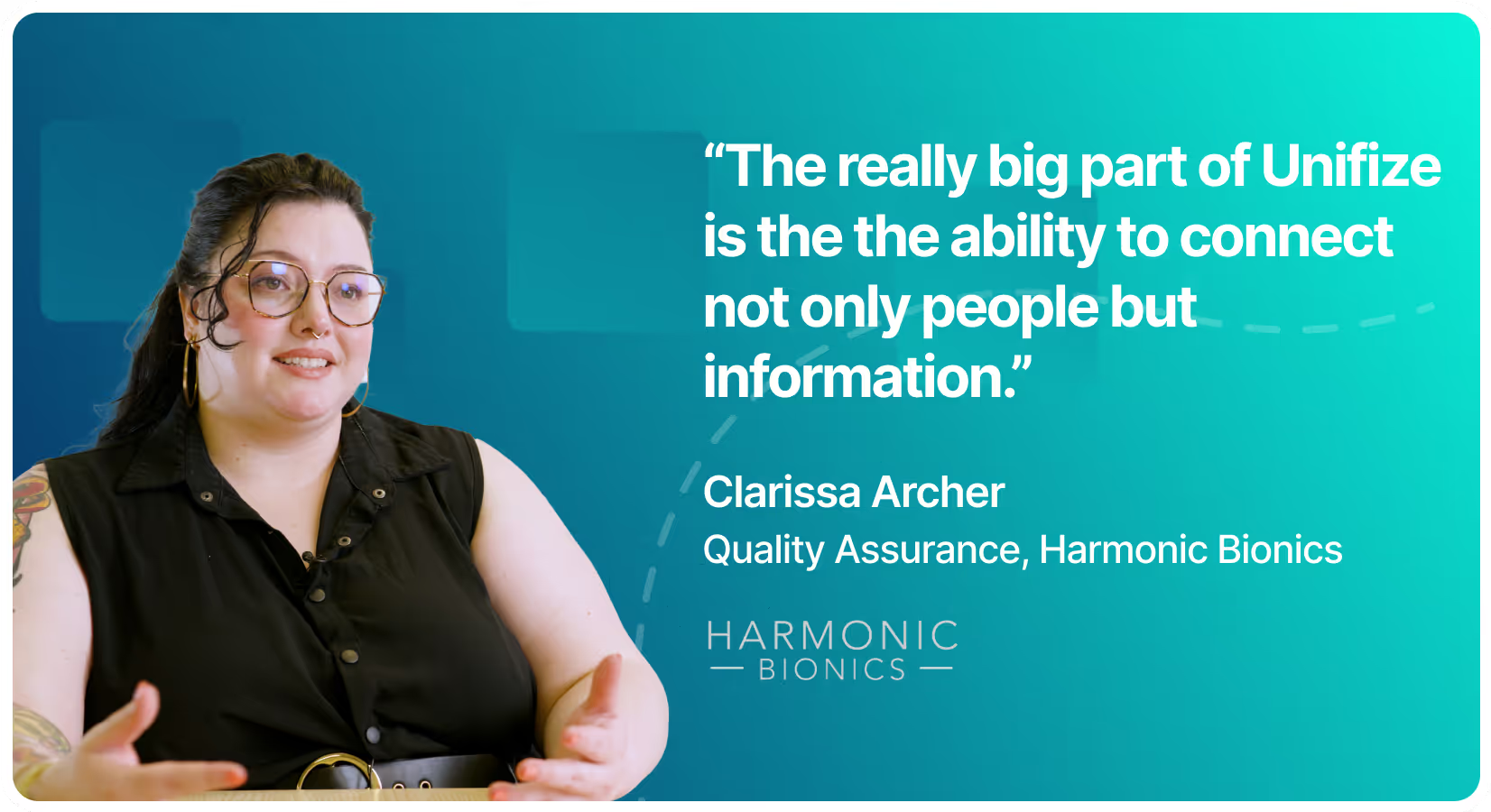
Customers
Harmonic Bionics and Unifize: A seamless transition to regulatory compliance
Clarissa Archer shares her experience integrating Unifize into Harmonic Bionics, underscoring its value in streamlining change control, facilitating communication, and ensuring robust documentation for regulatory compliance in the medical device sector.
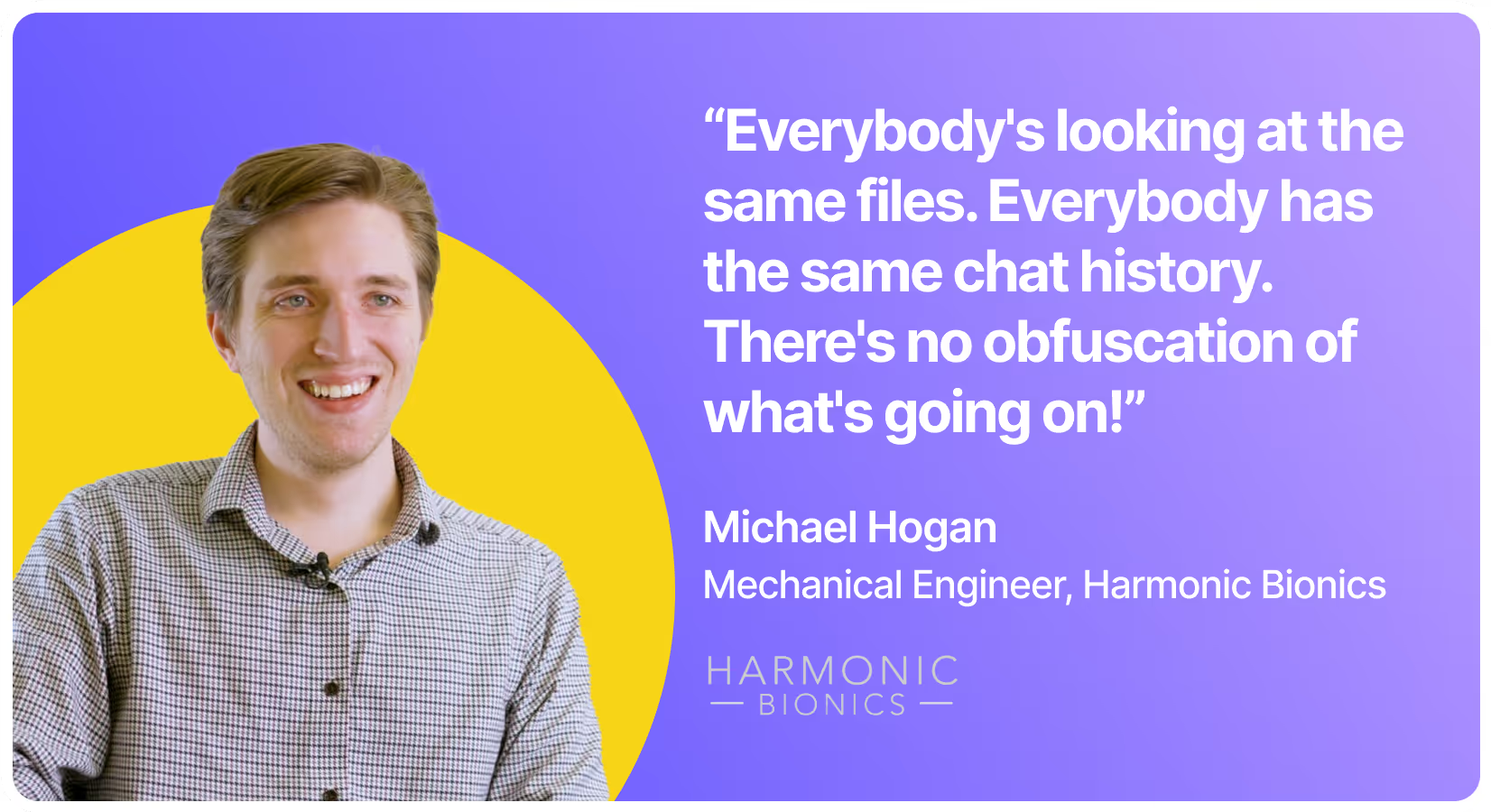
Customers
Engineering efficiency with Unifize: Michael Hogan's insights from Harmonic Bionics
Mechanical Engineer Michael Hogan elaborates on how the integration of Unifize at Harmonic Bionics has streamlined his engineering processes, promoting transparency and rapid turnaround in the medical device domain.
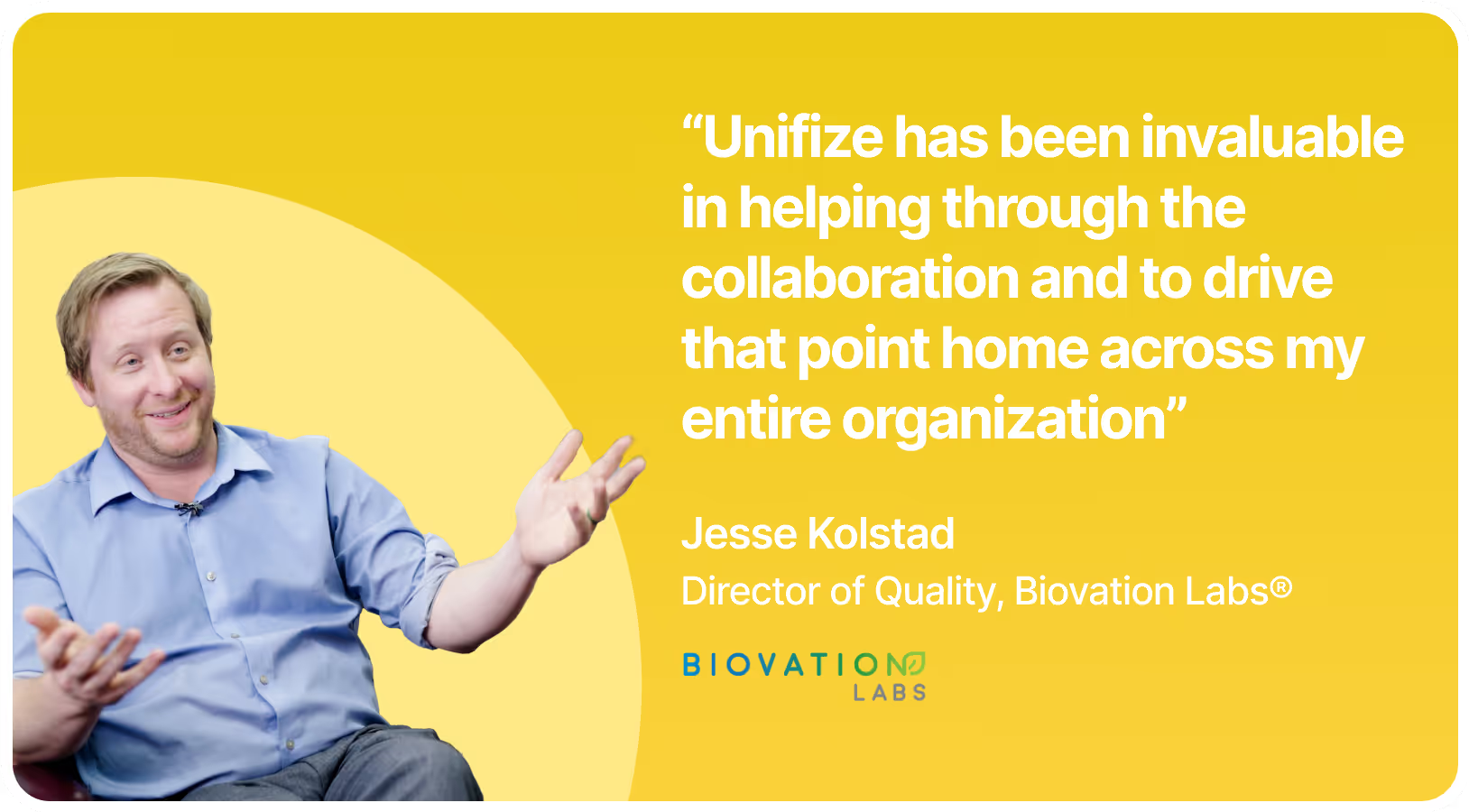
Customers
Here’s how Biovation Labs reduced testing costs from $146K to $65K in two months
Learn how and why Biovation Labs, an FDA regulated nutraceutical manufacturer based in Salt Lake City, took the decision to transition from MasterControl to Unifize for their product lifecycle (PLM) and quality management (QMS) processes.
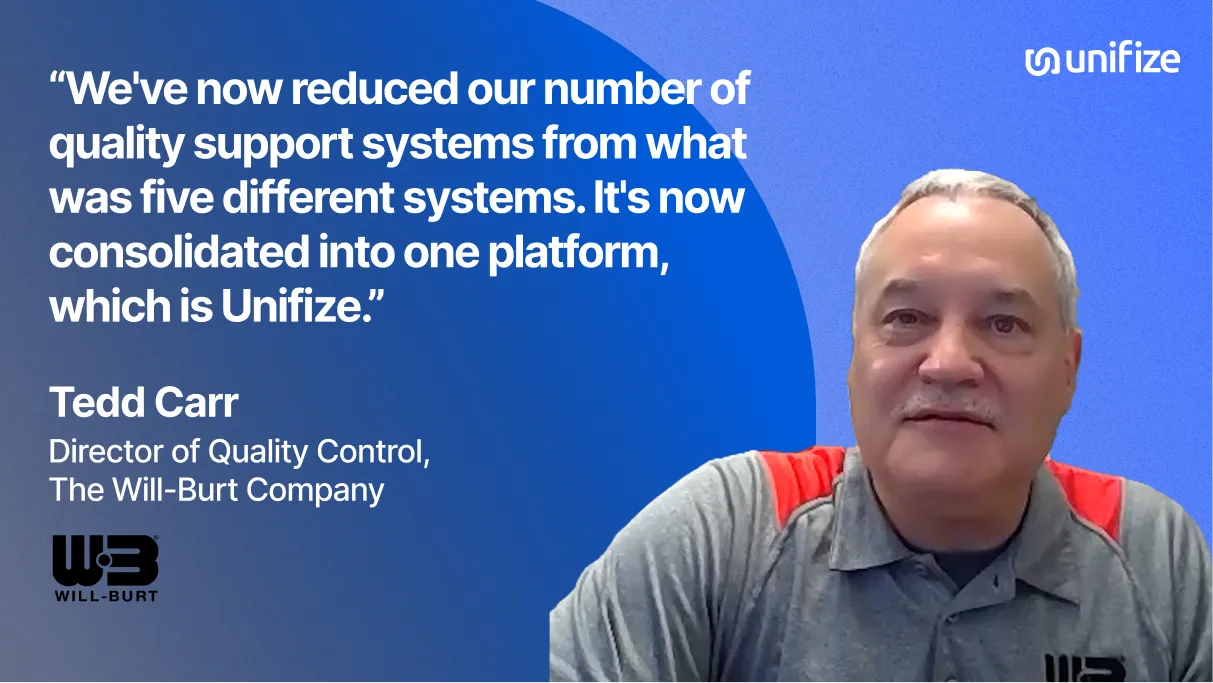
Customers
How a quality veteran from boosted issue closure time by 75% within the first month
Tedd Carr from The Will-Burt Company discusses overcoming their diverse and complex quality challenges across various sectors with Unifize. By consolidating five systems into one, they achieved clear accountability and reduced issue closure from months to days, demonstrating significant efficiency gains and faster decision-making in their quality processes.