Content Library
[00:00 - 00:24]
You know, the really big part of Unifize and the important part that I really keep coming back to the ability to connect not only people but information. And honestly, that is been one of the biggest benefits because, for example, you know, if we're still going down the nonperformance or deviation example, at prior companies with prior systems, it's really easy to miss out on some context.
[00:24 - 00:31]
And so having the ability to, see everything in an online accessible platform is huge.
[00:31 - 00:49]
Non-conformances at other places or even various types of change control and change order at different places, that is never really connected. And so, you know, you have to do a lot more digging and investigating and research into figuring out what is even going on.
[00:49 - 01:14]
And I think that's one of the biggest benefits of Unifize, is to be able to have those connections really easily available. For example, if you have a report or something like that or, you know, any kind of document that relates to a process or to a lot or a work order or those sorts of things, usually at other companies you have to go from, okay, I know this number.
[01:14 - 01:34]
Let me figure out how it's called in this other program or go into here and all of the information is very disorganized and disconnected, you know, and that's been one of the difficulties. And oh, well, only the manufacturing engineer has access to this information on this program like Oracle or something.
[01:34 - 01:42]
And, you know, oh, the product development engineer only has access to this information and the quality engineer has access to yet another source of information.
[01:42 - 01:59]
And so being able to have Unifize really unify all the information and get the collaboration, You're able to say, this is our single source of truth and this is where you have, you know, all the information that you need.
[01:59 - 02:10]
So you don't need to physically go in onto the manufacturing floor and say, okay, what's going on with this part? Because somebody didn't fully document it or have the information that you needed on hand.
[02:10 - 02:20]
The information is either, on paper in a cardboard box, on a huge manufacturing floor somewhere, or, you know, in various other places on somebody's desk.
[02:20 - 02:29]
That's happened so many times. So just being able to have the whole source of truth and everything in one place, that's really huge.
[02:29 - 02:55]
And to be able to collaborate amongst that place as well, the reasons why we chose Unifize in that we would choose Unifize again is because you have that connection and the collaboration that is really huge, especially when you're dealing with complex medical devices and you need to make sure that you understand the history behind each device, each choice, each change you're making, you know, Unifize is really huge.
[02:55 - 03:03]
To be able to collaborate with others and to keep track of what history has been going on with those devices.
[03:03 - 03:18]
Tribal knowledge is really difficult to combat and having the history of conversations and the history of changes and the history of all these connected things that go into making a medical device is huge and really important.
[03:18 - 03:40]
You know, we were missing that from a lot of other options that we looked at. You know, yes, you have change control here and deviations and non conformance and all of these different things that other other products treat as completely separate entities when in reality, you know, a deviation is going to go into and flow into a change order.
[03:40 - 03:56]
And so being able to have the history right at your hands and to be able to quickly see and connect everything that's going on really paints a truer picture and a connected picture of what all is going on within your change management system, within your quality management system.
[03:56 - 04:37]
I think one of the strongest things that really brought us to Unifize was the fact that you have this collaborative environment and this connected environment that really brings everything together so that, you know, as a quality engineer, you know, anytime we mention in a document or in a change that something else is related, okay, I have to now go from here and do a bunch of research and a bunch of digging to make sure that what we say here is correct to what we're connecting it to and Unifize just makes that so much more simple, because right at a click of a button, I can go instantly to what we're referring to and double check it and make sure we're compliant.
[04:37 - 04:54]
And you can add in processes. You know, one of the things that we like to do is create forms within Unifize, which again is super easy. And so you're able to add in, you know, connections to apart and say, okay, is the connection of, okay, I want to make this change.
[04:54 - 05:00]
I want to pull this process into here. And from there you can also see.
[05:00 - 05:17]
You can see that process. And you can also say, Oh yeah, you know, from a document, I also want to include the revision or the description or these other things. And so within Unifize, you can say that yes, I want to connect this process into a change order to deviation to whatever.
[05:17 - 05:45]
And here's the information from that other process that I want to include, because it's important for this process, and that's huge so that you don't have to click and open it and go through everything you can choose. Here are the things that are important. When I'm looking at this particular process that I want to be able to see every time without necessarily opening a new window, So traceability is often a very big pain point within other within other companies, any company.
[05:45 - 06:08]
And so the traceability of being able to say, okay, I have this lot of this part connected to the traceability of the lot and the part and the non conformance is or tracing that into different assemblies, you know, we're able to create work orders that says, you know, this device is created of these different parts from these different lots.
[06:08 - 06:24]
And so when you have a huge robot, you know, you can easily see the different parts that went into it and trace through and see the inspection data for every single part that goes into that one product. And you're able to do that on a serialized level as well.
What it really means to Unifize your information and people

Customers
Denis's experience with Unifize: Revolutionizing quality assurance systems
Quality expert Denis details his transformative journey with Unifize. He praises its efficient design, user-centric approach, and the system's ability to streamline data handling and accelerate time to market.
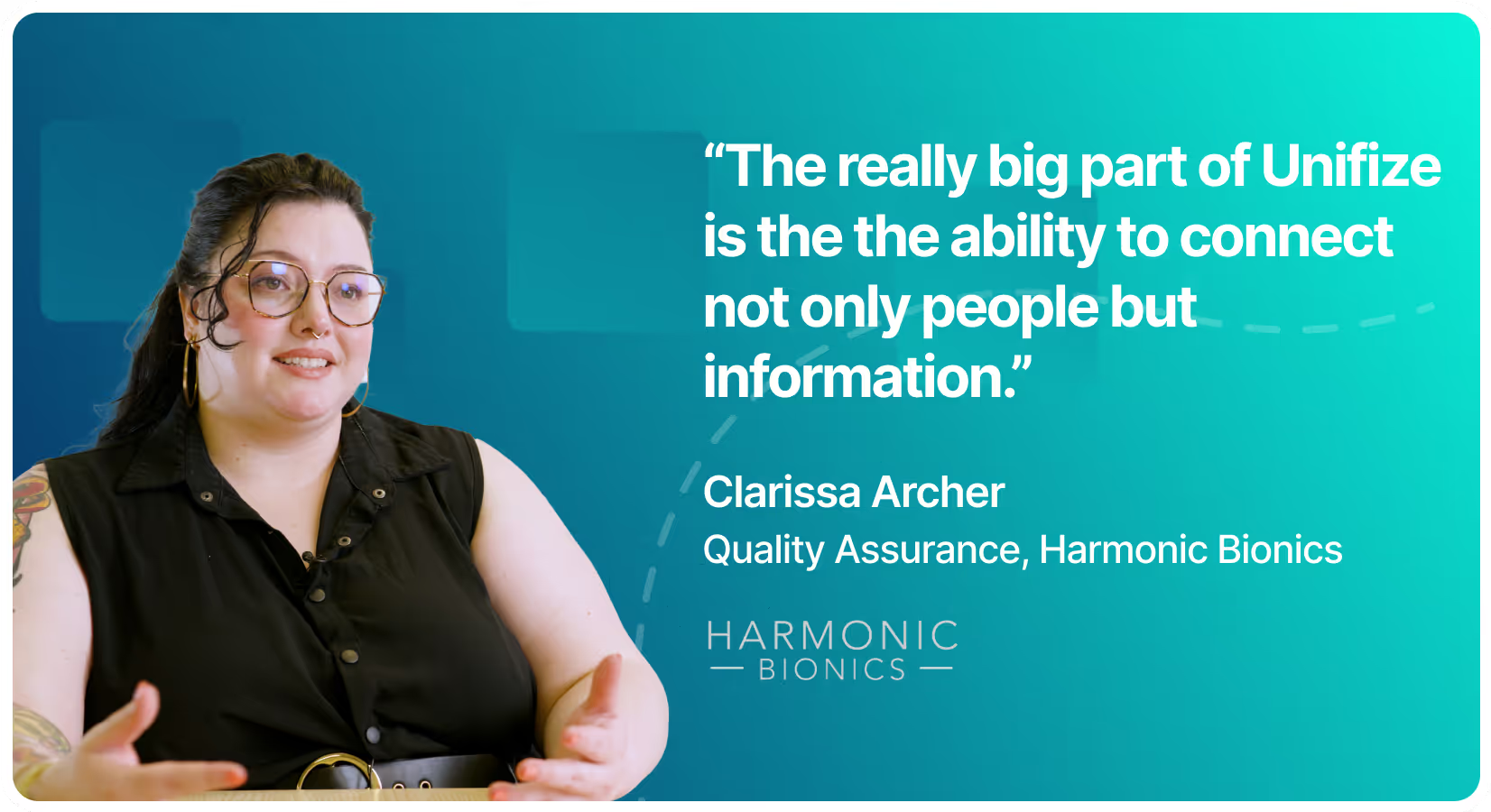
Customers
Harmonic Bionics and Unifize: A seamless transition to regulatory compliance
Clarissa Archer shares her experience integrating Unifize into Harmonic Bionics, underscoring its value in streamlining change control, facilitating communication, and ensuring robust documentation for regulatory compliance in the medical device sector.
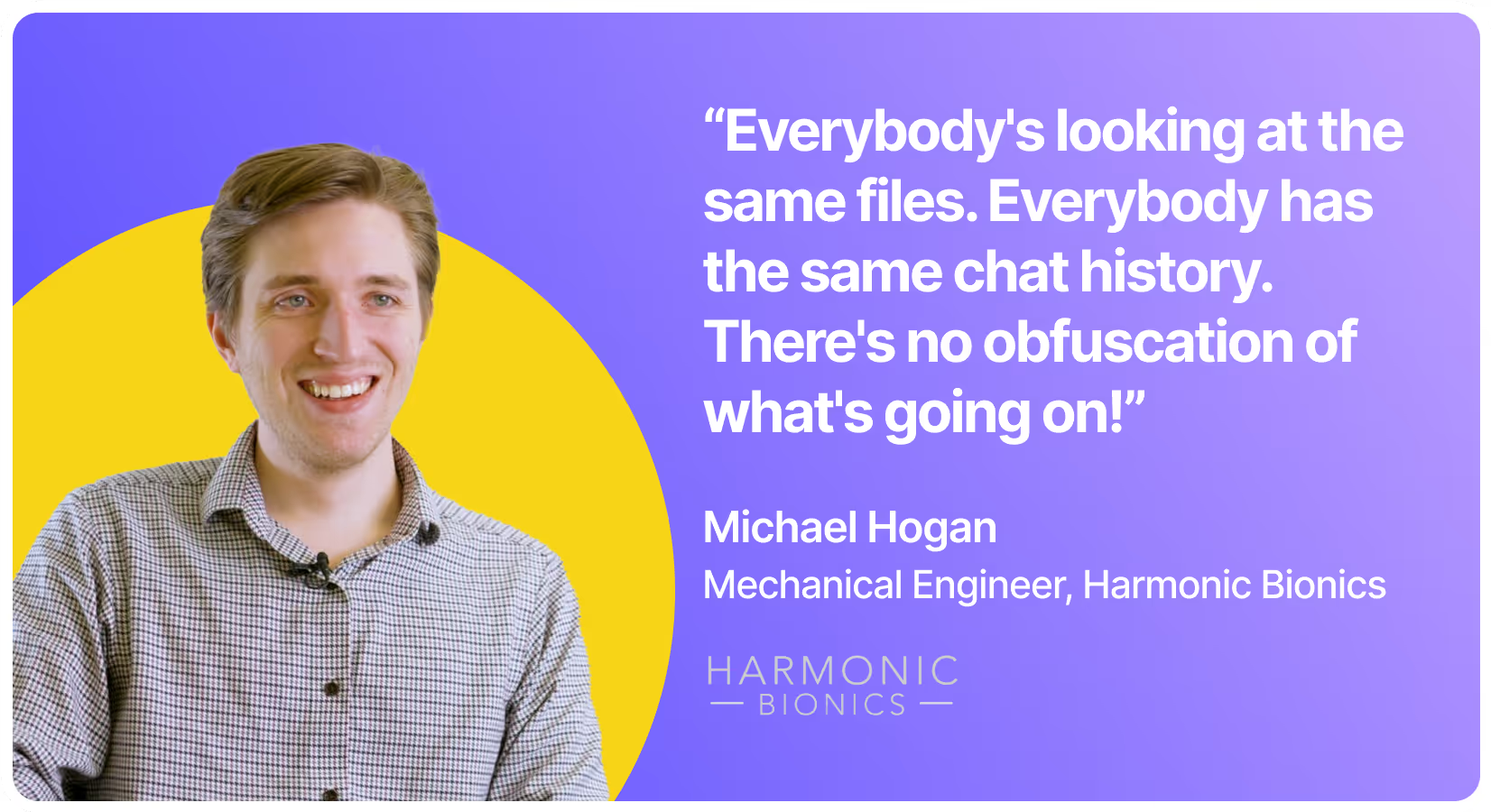
Customers
Engineering efficiency with Unifize: Michael Hogan's insights from Harmonic Bionics
Mechanical Engineer Michael Hogan elaborates on how the integration of Unifize at Harmonic Bionics has streamlined his engineering processes, promoting transparency and rapid turnaround in the medical device domain.
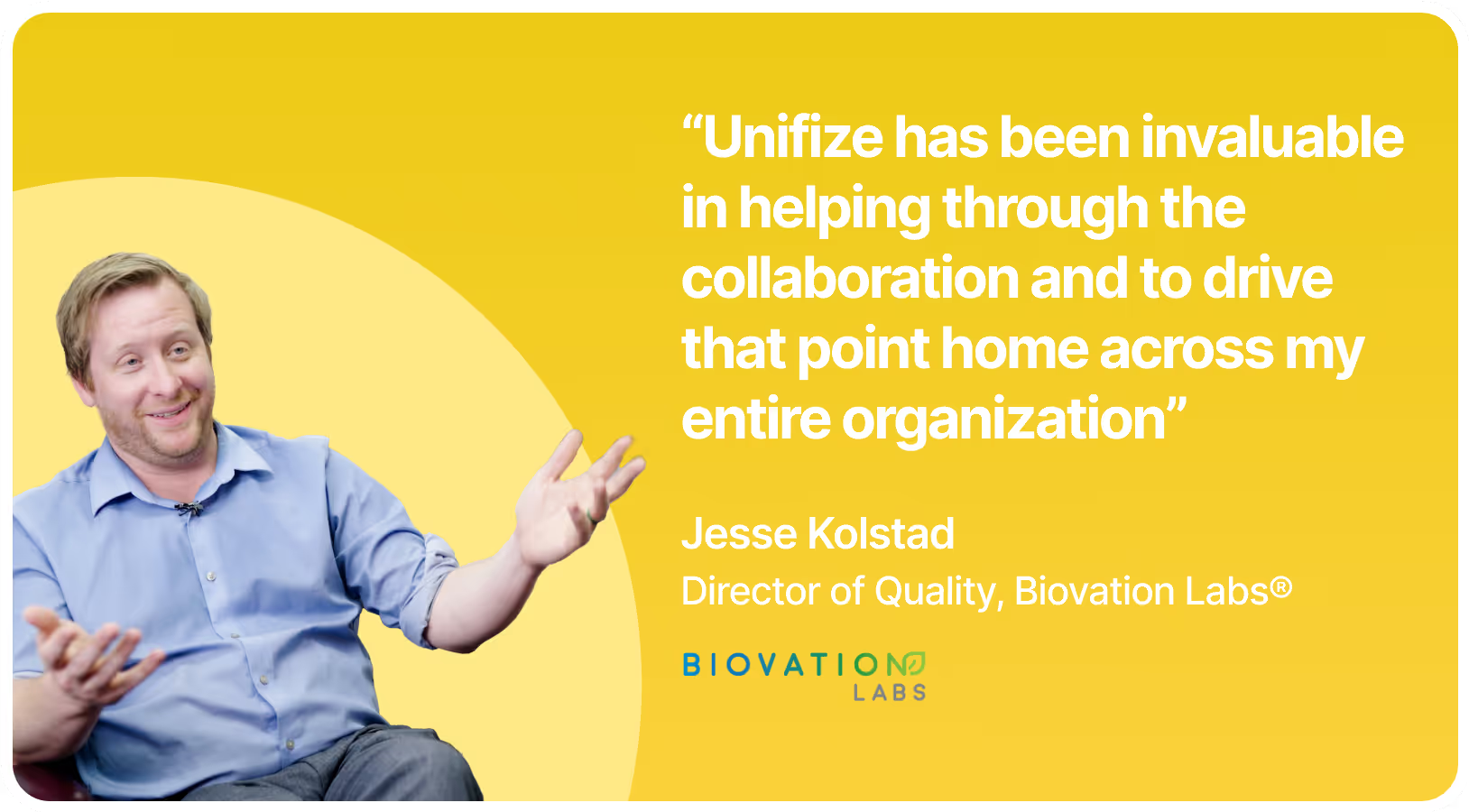
Customers
Here’s how Biovation Labs reduced testing costs from $146K to $65K in two months
Learn how and why Biovation Labs, an FDA regulated nutraceutical manufacturer based in Salt Lake City, took the decision to transition from MasterControl to Unifize for their product lifecycle (PLM) and quality management (QMS) processes.
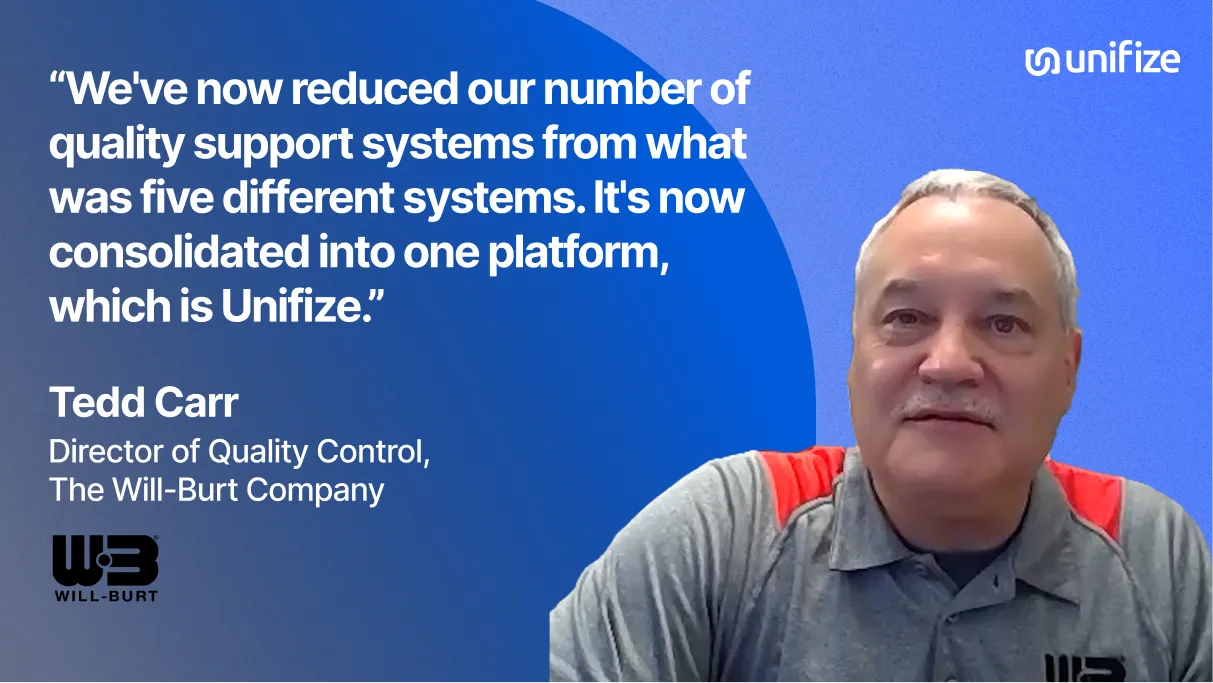
Customers
How a quality veteran from boosted issue closure time by 75% within the first month
Tedd Carr from The Will-Burt Company discusses overcoming their diverse and complex quality challenges across various sectors with Unifize. By consolidating five systems into one, they achieved clear accountability and reduced issue closure from months to days, demonstrating significant efficiency gains and faster decision-making in their quality processes.