Content Library
00:00 - 00:43
You know, I think it really, right now for us where Unifize has shined in that respect is not so much on the raw material approval side. It has been on the corrective action side. The initial investigation, what went wrong and why, and especially if it involves external parties, third party contract manufacturers, other raw material vendors and suppliers, the ability for Unifize to be able to bring those outside parties into the conversation within your internal platform without a single person pinging emails back and forth, “Hey, this lot number didn't work. We found this and that one, this QC person over in this company said this, but they're cute to him. Their quality assurance manager said that.”
00:43 - 01:08
Trying to keep track of all those things and then being, having to be the point person that informs the rest of your internal team of what those conversations look like. Being able to have Unifize just be a natural part of that investigative process when you're trying to inform all the parties involved of what the current status is of an open deviation and why we think that occured, possible sources of the quality issue and so on, so forth.
01:08 - 01:37
That's where I've seen the immediate benefit. You know, when we have a quality issue that arises, say, with the third party contractor, I could just loop that their quality person directly in to the open carrot we have on Unifize itself. They can see the conversation we've had so far about potential sources of the quality issue in the first place, and then they could provide their feedback and then we can just update the counter form right there instead of waiting till weeks afterwards.
01:37 - 02:03
What sometimes happens is you can have these emails, you can have these conversations on the phone, you have these meetings with these external providers. But then when it comes time to actually updating your corrective action documentation, you have to go back and remember what you guys talked about. If you're not doing it right then, then it becomes much more difficult one week, two weeks, three weeks later on the process to be able to accurately recall and input all the potential solutions that you've discussed.
02:04 - 02:26
You're relying on memory and bits and pieces of information in different emails to piece together in order to recreate that information to put into your quality management system. And with Unifize, you don't you're not forced to do that, or the possibility of that occurring is reduced because you could just tap it in right there, as a conversation is happening.
02:26 - 02:36
When it comes to documentation and compliance, it's not a linear process where everyone is looking at the same thing at the same time all the time.
02:36 - 02:42
People are in their day to day workflow, are doing so many different things at once.
02:42 - 02:59
That information isn't synchronized in any way. So the more you're able to build in your compliance process, your documentation process into that day to day activity without increasing the resources required to execute the process, Unifize gives us the option to actually do that.
02:59 - 03:06
And right now it's really shown itself for us in being able to execute corrective actions for for the company.
Investigating deviations with Unifize

Customers
Denis's experience with Unifize: Revolutionizing quality assurance systems
Quality expert Denis details his transformative journey with Unifize. He praises its efficient design, user-centric approach, and the system's ability to streamline data handling and accelerate time to market.
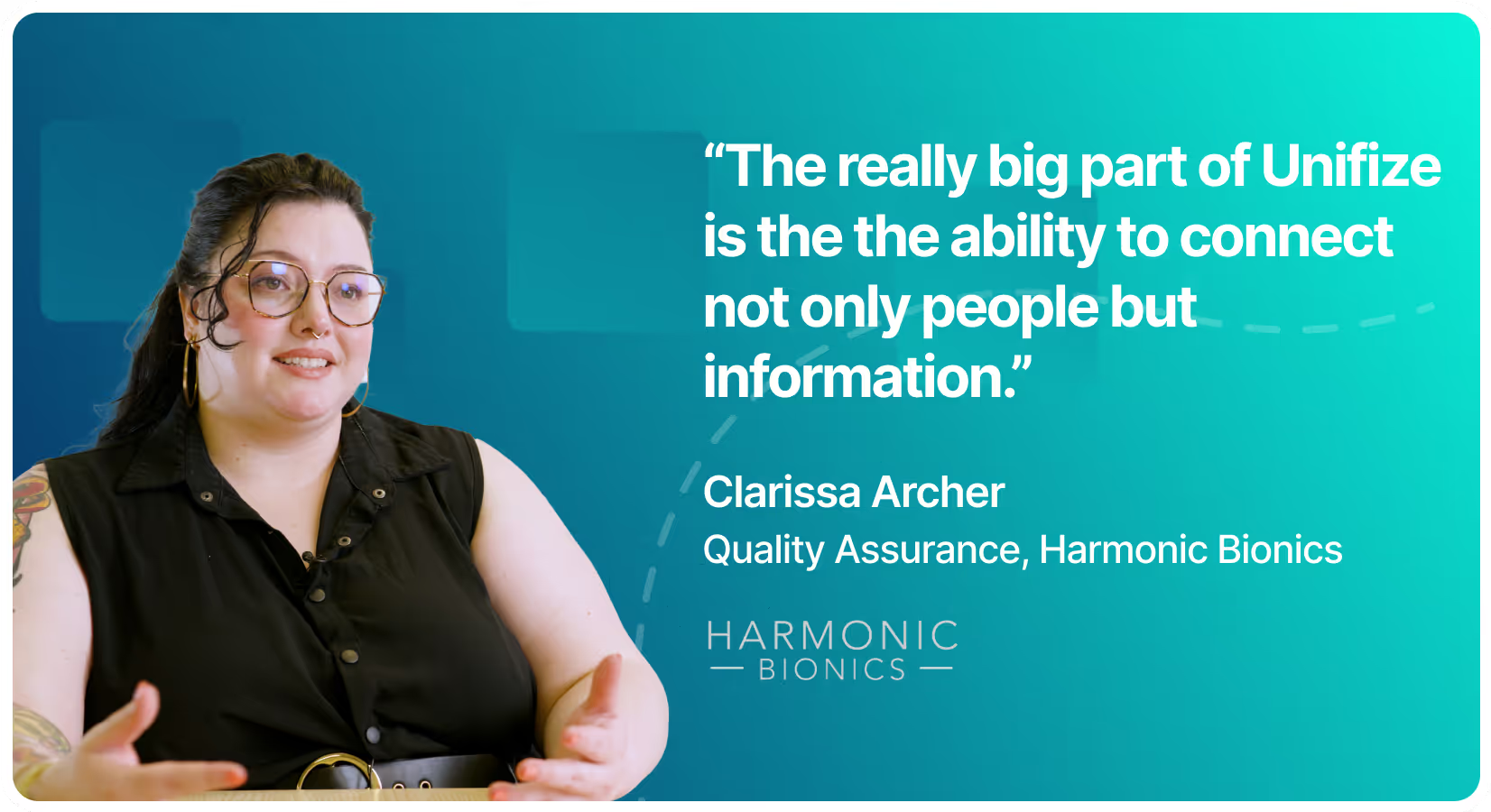
Customers
Harmonic Bionics and Unifize: A seamless transition to regulatory compliance
Clarissa Archer shares her experience integrating Unifize into Harmonic Bionics, underscoring its value in streamlining change control, facilitating communication, and ensuring robust documentation for regulatory compliance in the medical device sector.
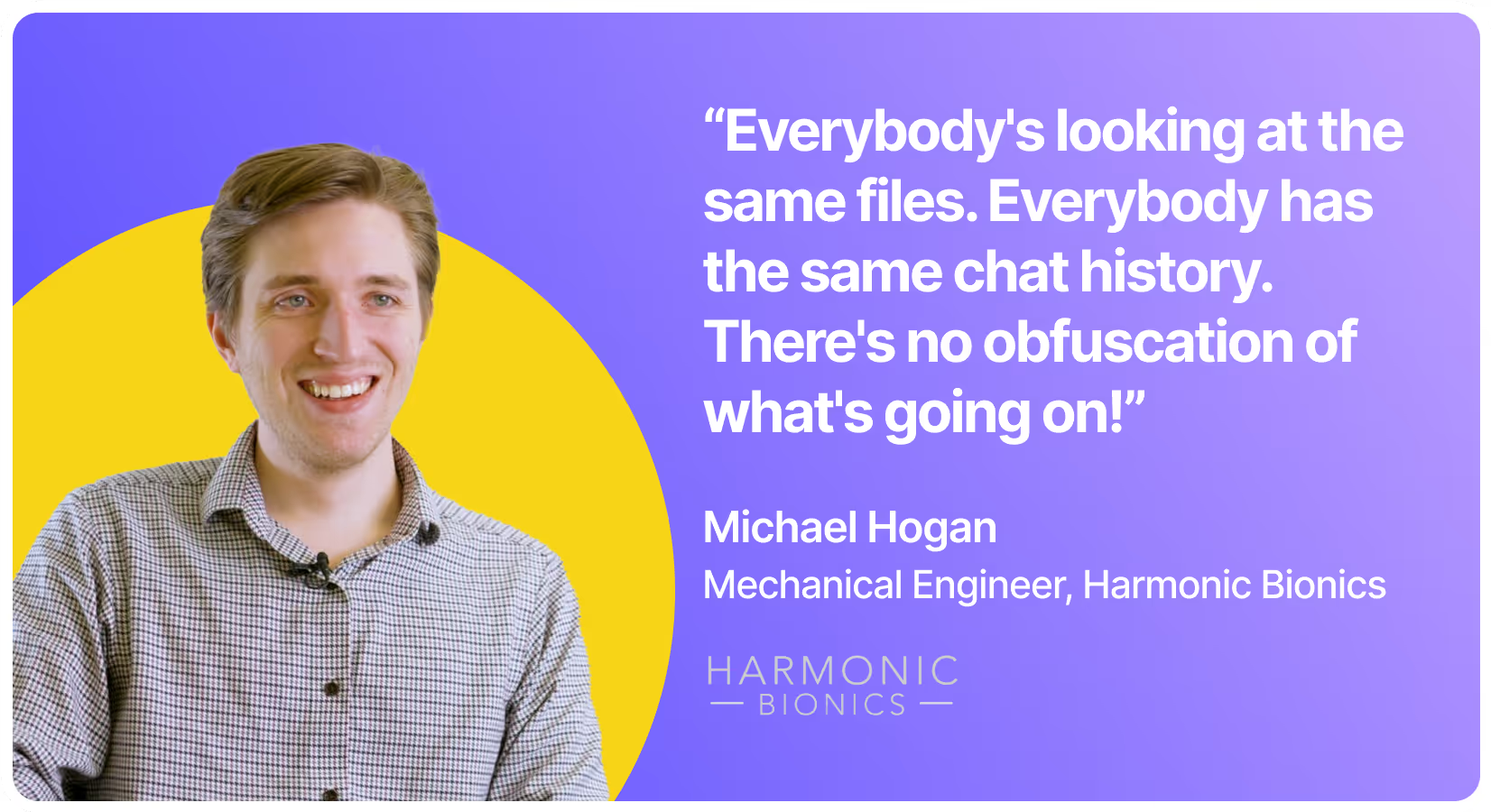
Customers
Engineering efficiency with Unifize: Michael Hogan's insights from Harmonic Bionics
Mechanical Engineer Michael Hogan elaborates on how the integration of Unifize at Harmonic Bionics has streamlined his engineering processes, promoting transparency and rapid turnaround in the medical device domain.
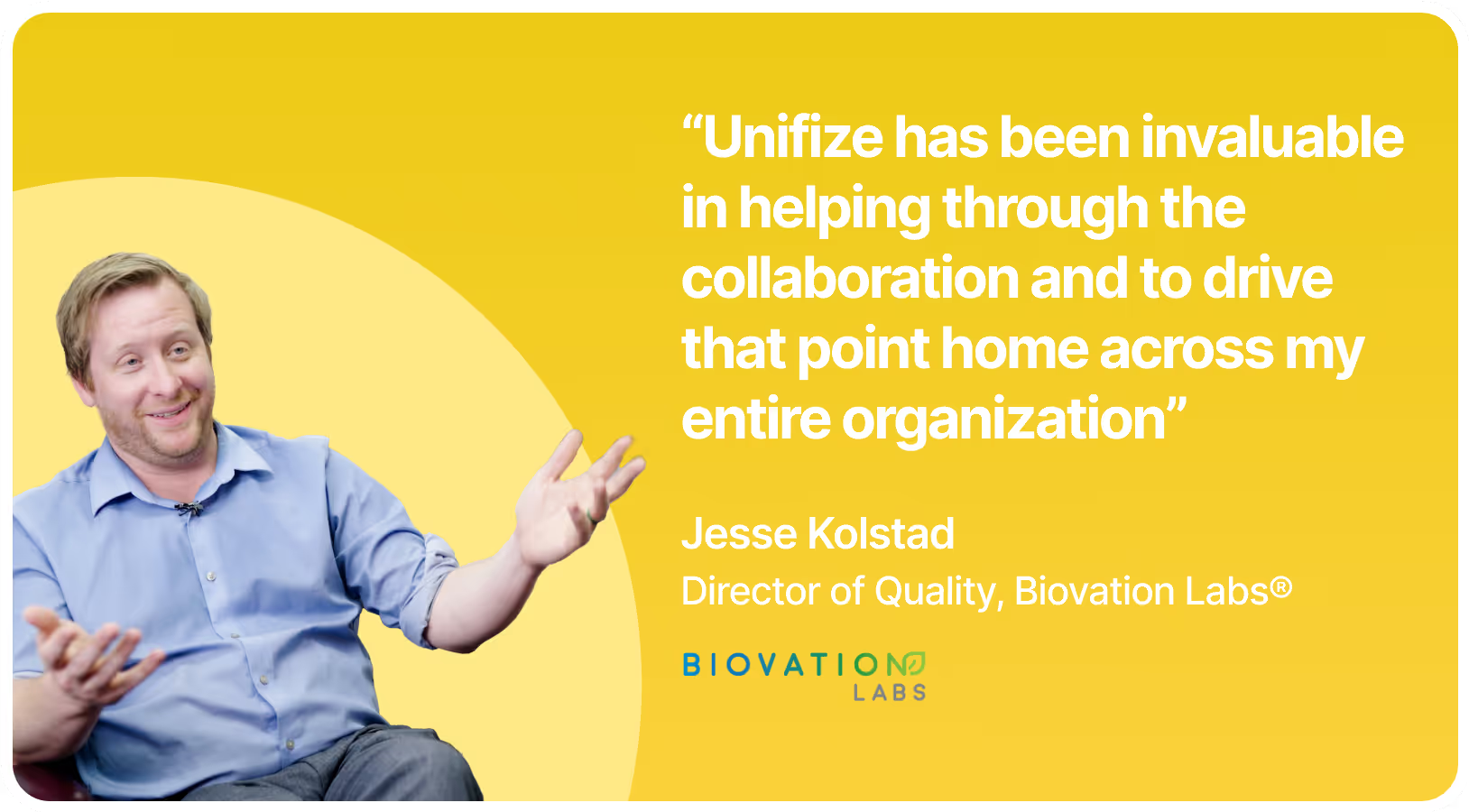
Customers
Here’s how Biovation Labs reduced testing costs from $146K to $65K in two months
Learn how and why Biovation Labs, an FDA regulated nutraceutical manufacturer based in Salt Lake City, took the decision to transition from MasterControl to Unifize for their product lifecycle (PLM) and quality management (QMS) processes.
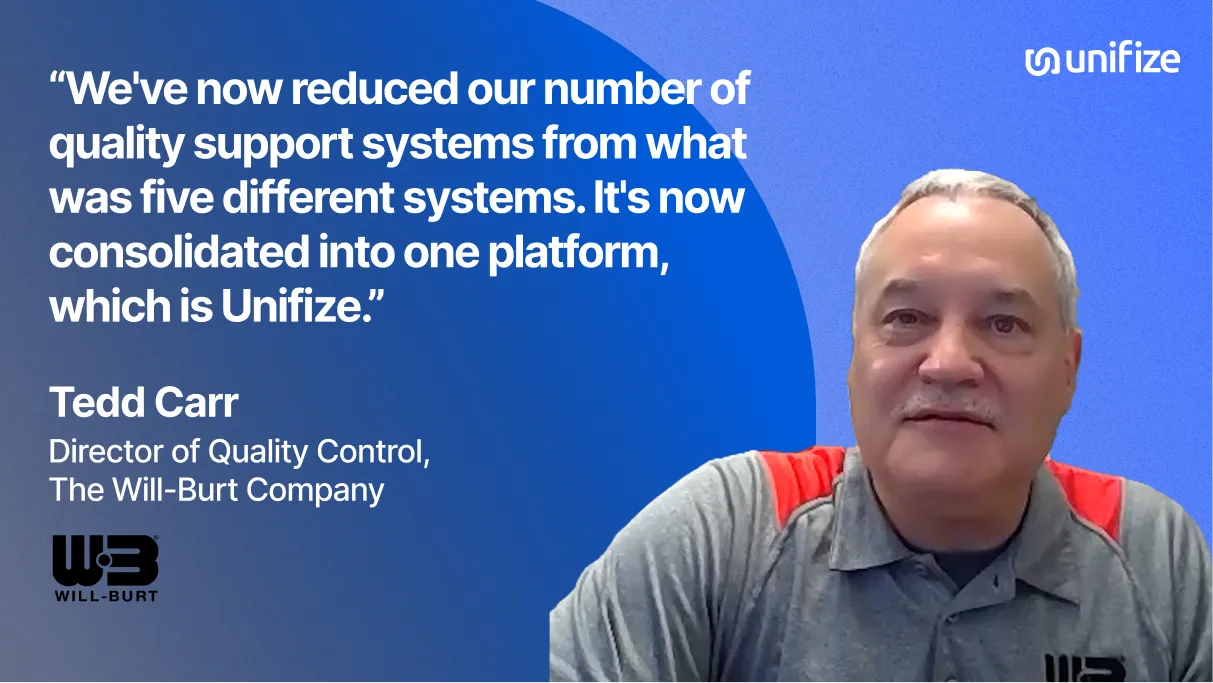
Customers
How a quality veteran from boosted issue closure time by 75% within the first month
Tedd Carr from The Will-Burt Company discusses overcoming their diverse and complex quality challenges across various sectors with Unifize. By consolidating five systems into one, they achieved clear accountability and reduced issue closure from months to days, demonstrating significant efficiency gains and faster decision-making in their quality processes.