Content Library
00:00 - 00:18
Unifize itself is not a solution to having bad processes. But if you have good processes in place, but the way you execute those processes is too resource intensive, and you're having issues with keeping everyone on the same page, a platform like Unifize can solve a lot of those issues.
00:18 - 00:32
People hate to admit it, of course, but, you know, sometimes you just don't pay attention to it until you know that an auditor is coming in. But then if you're going to wait till that point, then you're not you're not running a quality management system the way it was originally intended.
00:32 - 00:46
So, you know, being able to use Unifize and saying that we are trying to reduce the friction between documentation and compliance with what is actually going on your work day, every single day.
00:46 - 00:48
That's the option that Unifize opens up to us.
00:48 - 00:55
I'd say it's mainly a big quality of life improvement in how that process works.
00:55 - 00:59
Unifize ended up being the right choice for us. I would absolutely recommend it.
01:04 - 01:19
My name is Wilson Lin, I wear many different hats here at Applechem. I've been with the company for almost 18 years now, and so I handle marketing, regulatory, compliance as well as managing the quality assurance department here, here at the company.
01:19 - 01:30
So Applechem is a research and development technology company that creates and manufactures functional ingredients for the personal care and cosmetics space.
01:30 - 01:40
So we are in charge of making, you know, the thickeners, rheology modifiers, pigment dispersants, the stuff that makes the formulations tick inside of the consumer products that people enjoy every day.
01:40 - 01:52
Applechem has 18 employees right now. We're located in Parsipanny, New Jersey. Our facility here is designed for foreign office administration, R&D activities, as well as manufacturing and warehousing.
01:52 - 02:06
We've got customers all over the place, so anywhere from small indie brands starting out with the Nuon skincare or Suncare lines all the way to the larger multinationals like Estee Lauder and Chanel.
02:06 - 02:15
As a manufacturer of ingredients for cosmetics, we of course have to comply with the FDA, CFR 21, you know, the Food and Drug and Cosmetics Act.
02:15 - 02:26
But there's also in order to give customers the confidence that what we're making is of high is, is high quality product. We need to make sure that we're adhearing to the good manufacturing processes as well.
02:26 - 02:44
Between the ISO 9001, the ICH Q7, CGMP Standards for quality for active pharmaceutical ingredients, we have a lot of different regulatory and quality standards that we have to be in compliance with to to manufacture our products.
02:48 - 03:23
We weren't leveraging our quality management system to its fullest potential to help improve how we do our day to day business operations. And that's the whole point of having a quality management system in the first place is to be able to identify, control, document, and then create improvements in how those core business practices affect the quality output of your product, how that entire system works, and if the mechanics of how that quality management system operate are so difficult to work with in the first place, or so resource intensive, then it becomes a self-defeating prophecy.
03:23 - 03:32
Unifize from what I was reading was designed to solve that. I don't think businesses can be competitive when departments are working in data silos.
03:32 - 03:39
I think in the modern world now, especially as companies grow larger and they are more being merged with other companies.
03:39 - 03:54
And so the ability to transfer information back and forth and have everyone in different parts of the world looking at the exact same info at a single source of truth becomes more and more important for collaboration to work effectively in the modern world.
03:54 - 04:21
Collaboration for me now is the ability for all stakeholders involved in the development of a business or operation of a business process to be looking at a single source of truth so that any conversations, any data input or updates, all that is going to a centralized place. And there's no inefficiencies involved in keeping everyone talking about the same things with the same framework, with the same context.
04:24 - 04:28
The biggest improvements are around visibility and accountability for us.
04:28 - 04:42
We didn't have to ask if a certain document had been sent out to a supplier or if it had been sent back and filled out correctly. We didn't had to ask if certain coding documentation was already in place before we moved to another stage in the validation process.
04:42 - 04:51
We can see that it's already been done and so those questions, those conversations didn't need to happen again. It didn't need to happen in the first place.
04:51 - 05:11
Just being a central repository for all these discussions in line with a checklist of all the necessary stages, all the necessary documents, all the necessary tasks required for launching a new product makes it a lot easier to keep everyone together and talking. And this has also reduced the amount of time spent on meetings.
05:11 - 05:23
Every meeting, subsequent meeting is reiterating the same information all the way up to the managing director. And that point you spent how many hours talking about the exact same thing and there's no resolution in sight.
05:23 - 05:36
So being able to eliminate 90% of that discussion and go straight to having all that information in a single place with the ability to enter all the information into the process on Unifize so that everyone can see it at the exact same time.
05:36 - 05:42
That level of transparency has been invaluable to us. It's a very much a quality of life improvement.
05:42 - 05:49
You know, we're glad that we were able to find a system like Unifize because it takes a huge burden off that the active management part.
How this cosmetric ingredients manufacturer used Unifize to eliminate redundancies and collaborate efficiently

Customers
Denis's experience with Unifize: Revolutionizing quality assurance systems
Quality expert Denis details his transformative journey with Unifize. He praises its efficient design, user-centric approach, and the system's ability to streamline data handling and accelerate time to market.
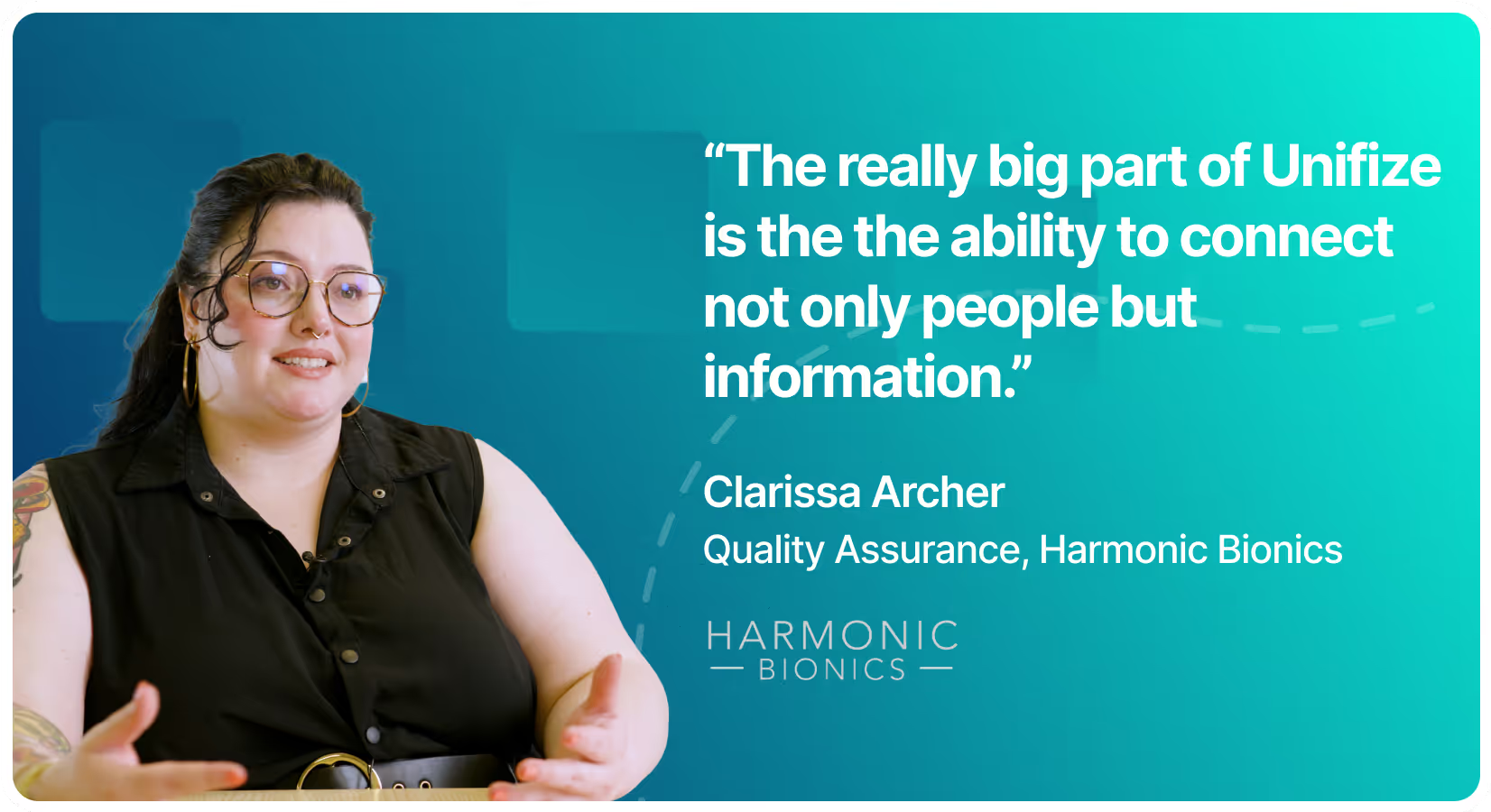
Customers
Harmonic Bionics and Unifize: A seamless transition to regulatory compliance
Clarissa Archer shares her experience integrating Unifize into Harmonic Bionics, underscoring its value in streamlining change control, facilitating communication, and ensuring robust documentation for regulatory compliance in the medical device sector.
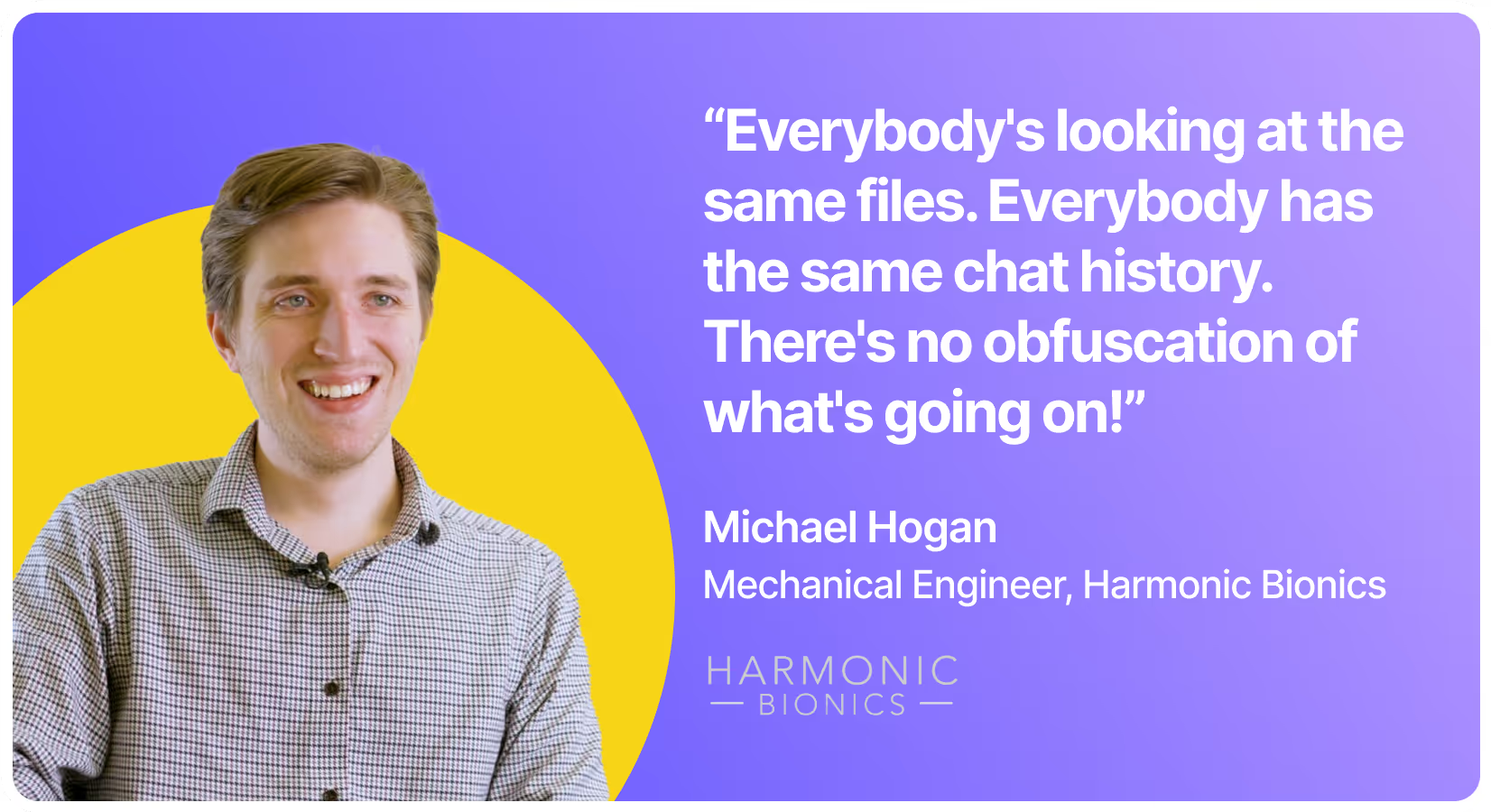
Customers
Engineering efficiency with Unifize: Michael Hogan's insights from Harmonic Bionics
Mechanical Engineer Michael Hogan elaborates on how the integration of Unifize at Harmonic Bionics has streamlined his engineering processes, promoting transparency and rapid turnaround in the medical device domain.
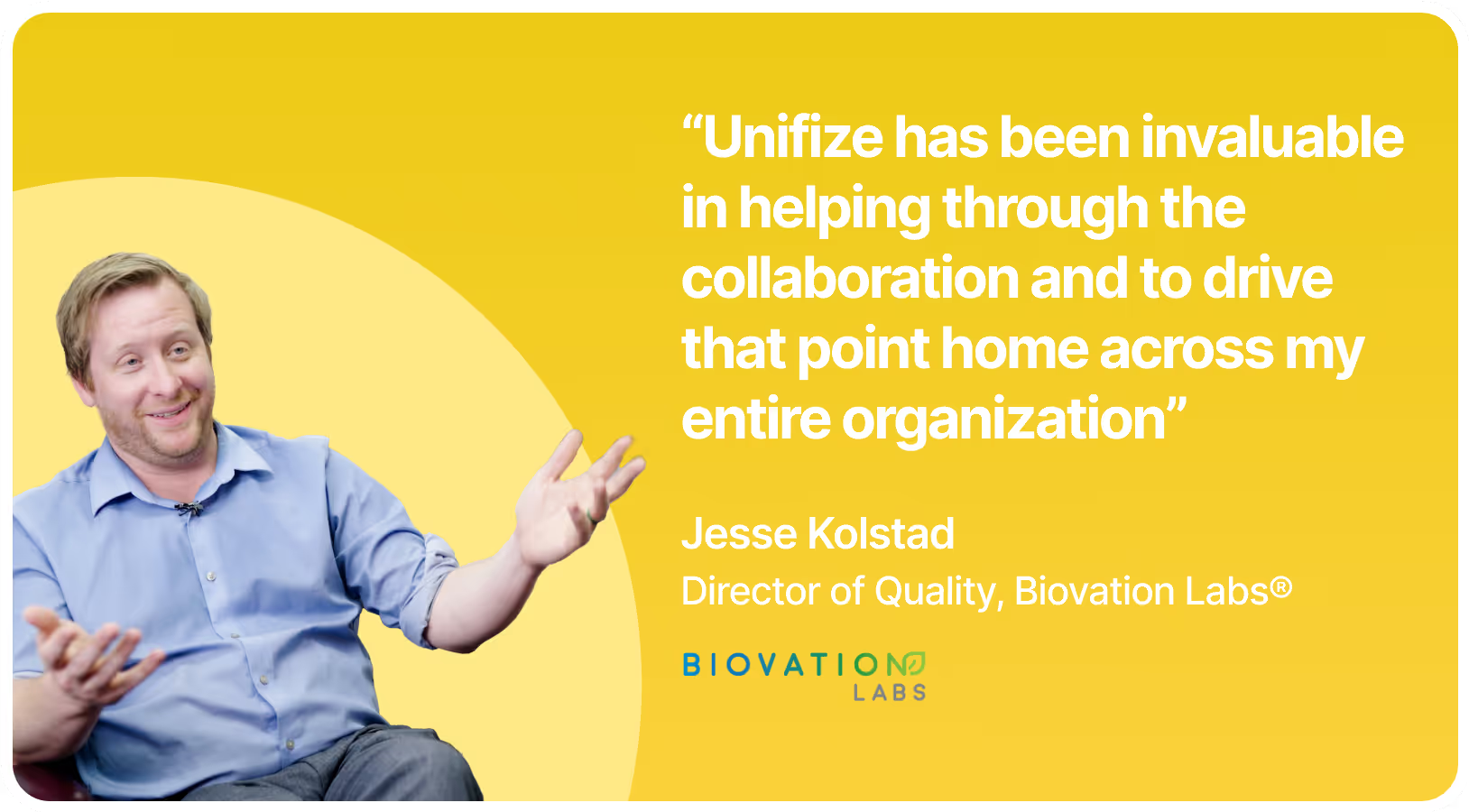
Customers
Here’s how Biovation Labs reduced testing costs from $146K to $65K in two months
Learn how and why Biovation Labs, an FDA regulated nutraceutical manufacturer based in Salt Lake City, took the decision to transition from MasterControl to Unifize for their product lifecycle (PLM) and quality management (QMS) processes.
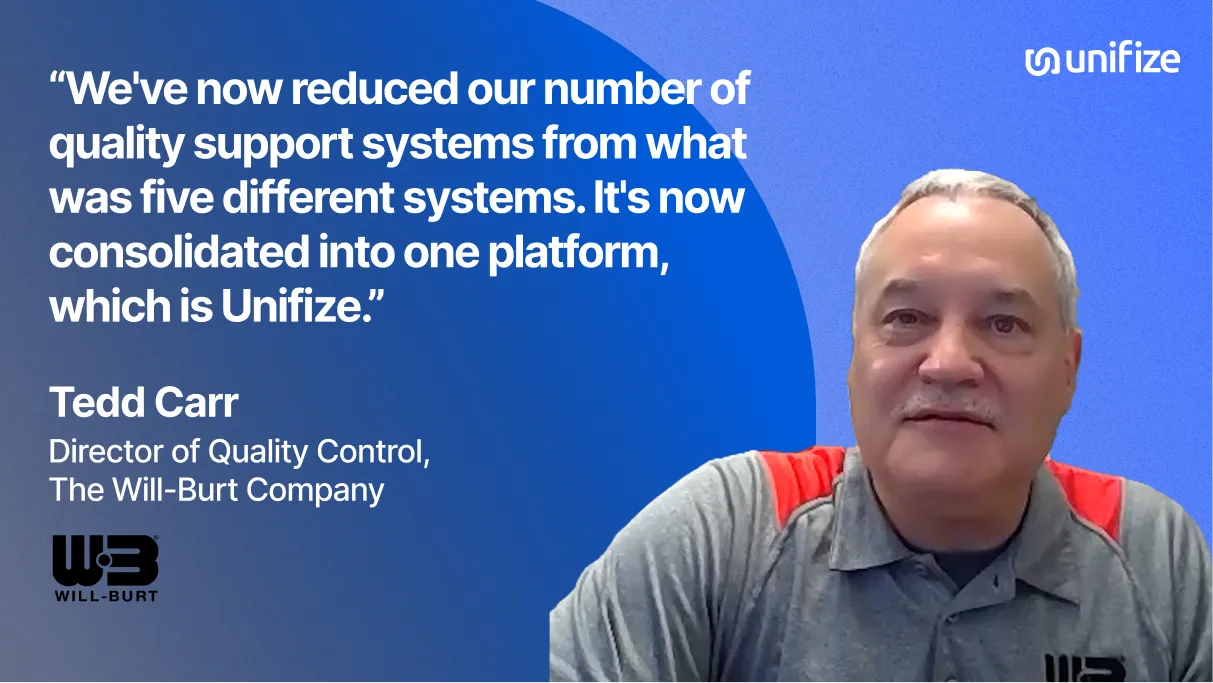
Customers
How a quality veteran from boosted issue closure time by 75% within the first month
Tedd Carr from The Will-Burt Company discusses overcoming their diverse and complex quality challenges across various sectors with Unifize. By consolidating five systems into one, they achieved clear accountability and reduced issue closure from months to days, demonstrating significant efficiency gains and faster decision-making in their quality processes.