Content Library
00:00 - 00:14
The thing about working at a small company is that it's the you know, it's about relationships, both with your coworkers, but with your suppliers, with your customers.
00:14 - 00:40
Right. When you have your people, the importance of people over systems becomes much more important. There's always there's always that balance, right? You can work for these huge 80,000, 80,000 person companies like Raytheon, where you have a very clearly defined role. It's very rigidly boxed. You only know the information for your particular project that you need to know.
00:40 - 01:07
I mean, literally your design inputs don't tell you anything about what you're actually working on in some cases for for good reasons. At a startup, it is it is very much about, you know, what is my what is my working relationship with my quality engineer, what is my working relationship with my suppliers? Right. Because at the end of the day, for a small company they live and die on, on relationships.
01:07 - 01:44
As far as the that ties into compliance, I mean, the thing is that everybody has to hold everybody accountable, right? We don't have the overhead or the or the systems that accrue over time that a rigidly enforce a set of standards as determined by the company. Right. And, you know, regulations are written from, at least in my opinion, from the sense that if you're doing everything right, everything that you should be doing, if you're doing a good job, you know, you will be very close.
01:44 - 02:07
If not already compliant with most standards. There was very few gotchas I've seen there in a tripped up. But the key thing is, is that you need to communicate right? I don't have a walking corpus of, you know, ISO 60601 in my head, right? I can't know everything about it, but between all the people at this company we do.
02:07 - 02:32
And so being able to communicate clearly with each other and being able to have information in a way that's easily accessible, that is flexible processes, is it is the strategy that you need to maintain, Right? If you try to enforce a rigid system on a start, it's just not going to work. There's no way, right?
02:32 - 02:40
You you know, there are days where I'll put on more of a quality engineering hat and maybe I'll go audit suppliers.
02:40 - 03:17
There are days where, you know, in the old days I'd literally was building robots in back. I was the technician. So I think that, you know, tying it back to regulation and I guess to Unifize is that the system that we have with Unifize reflects the scale and size of our company and the fact that it's so adaptive and we've changed it several times over already as we've learned more how to use the system and as we grow as the company is, that's really, you know, what we need as a company
Building a knowledge base in a startup with Unifize

Customers
Denis's experience with Unifize: Revolutionizing quality assurance systems
Quality expert Denis details his transformative journey with Unifize. He praises its efficient design, user-centric approach, and the system's ability to streamline data handling and accelerate time to market.
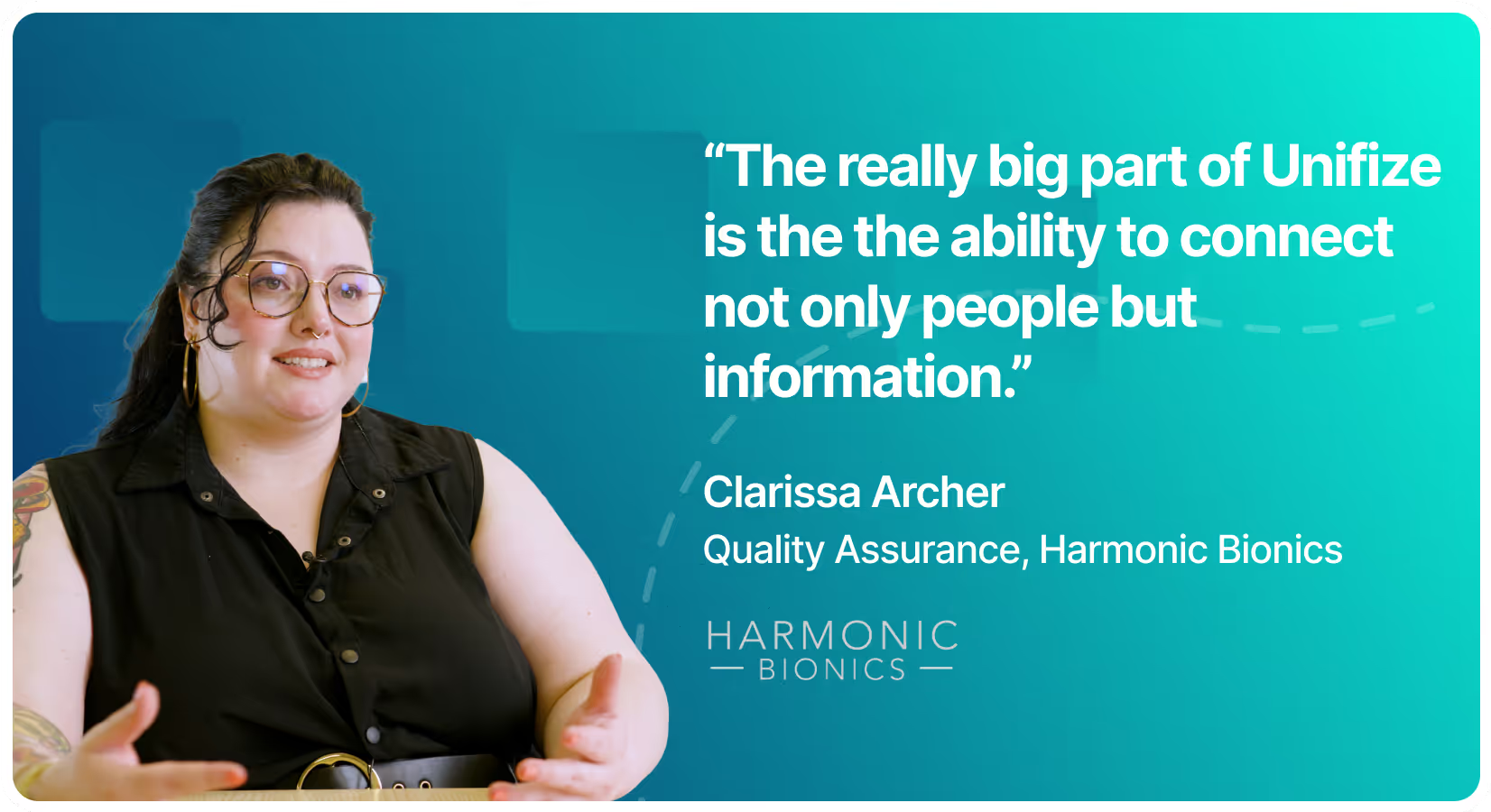
Customers
Harmonic Bionics and Unifize: A seamless transition to regulatory compliance
Clarissa Archer shares her experience integrating Unifize into Harmonic Bionics, underscoring its value in streamlining change control, facilitating communication, and ensuring robust documentation for regulatory compliance in the medical device sector.
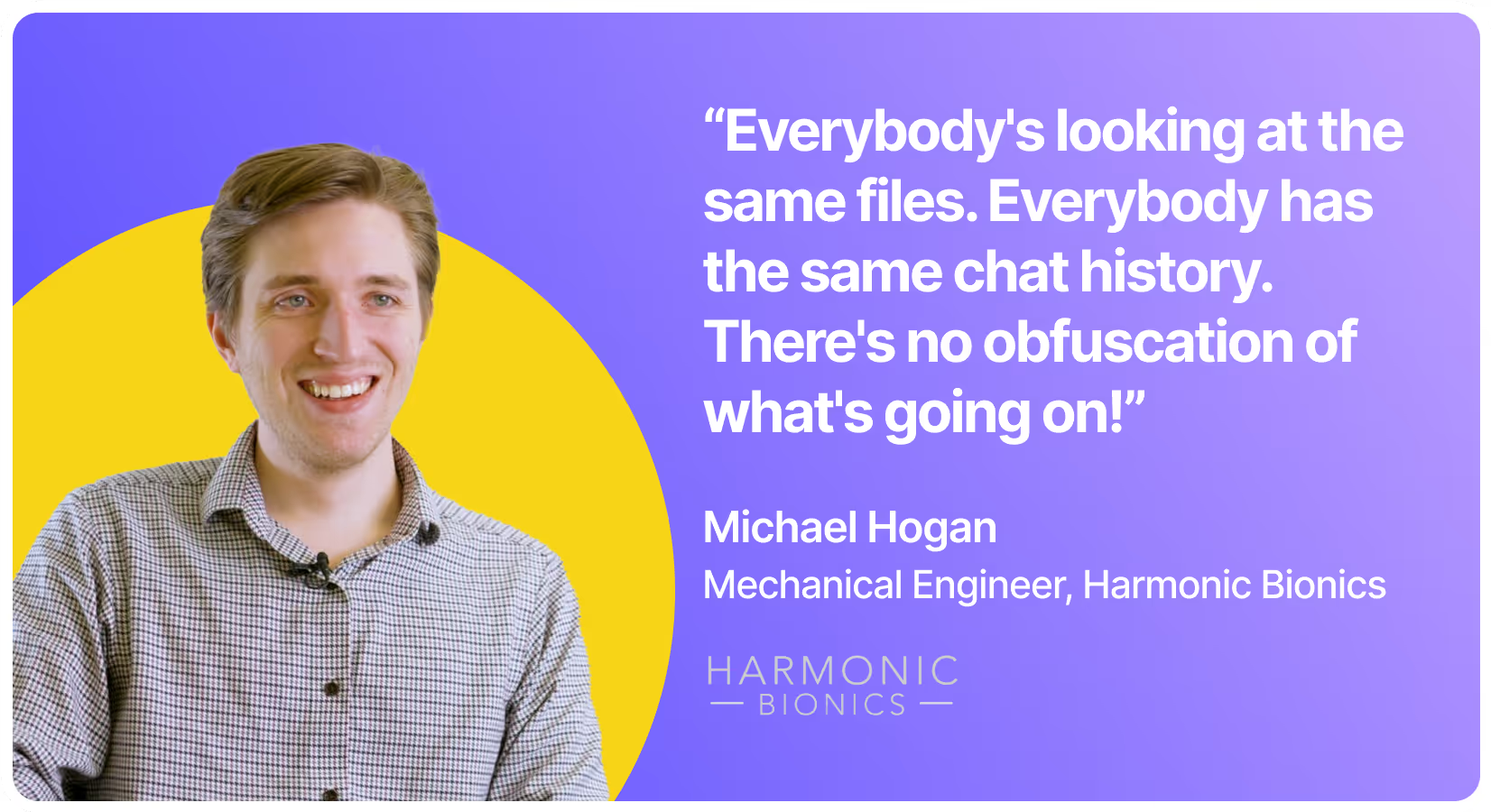
Customers
Engineering efficiency with Unifize: Michael Hogan's insights from Harmonic Bionics
Mechanical Engineer Michael Hogan elaborates on how the integration of Unifize at Harmonic Bionics has streamlined his engineering processes, promoting transparency and rapid turnaround in the medical device domain.
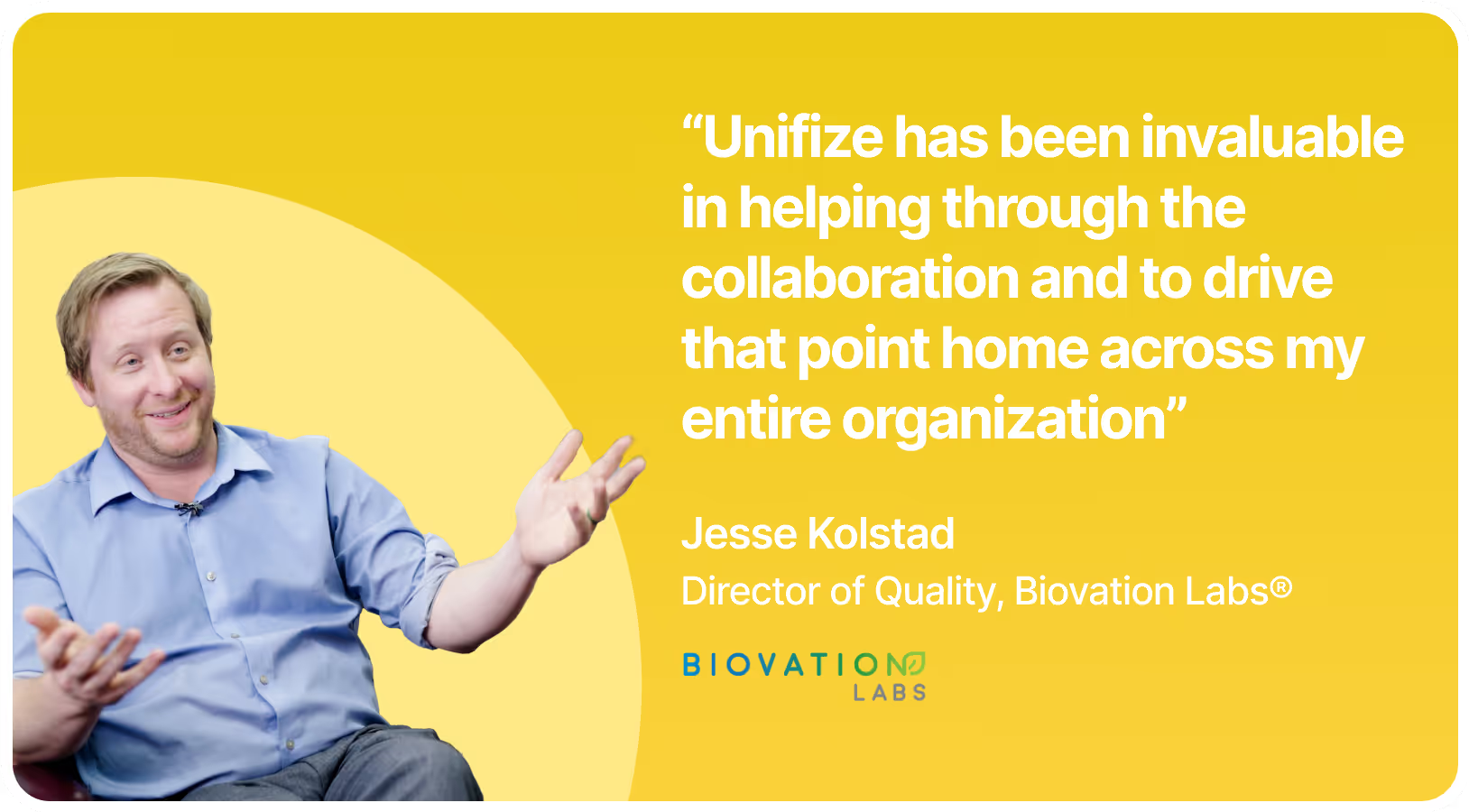
Customers
Here’s how Biovation Labs reduced testing costs from $146K to $65K in two months
Learn how and why Biovation Labs, an FDA regulated nutraceutical manufacturer based in Salt Lake City, took the decision to transition from MasterControl to Unifize for their product lifecycle (PLM) and quality management (QMS) processes.
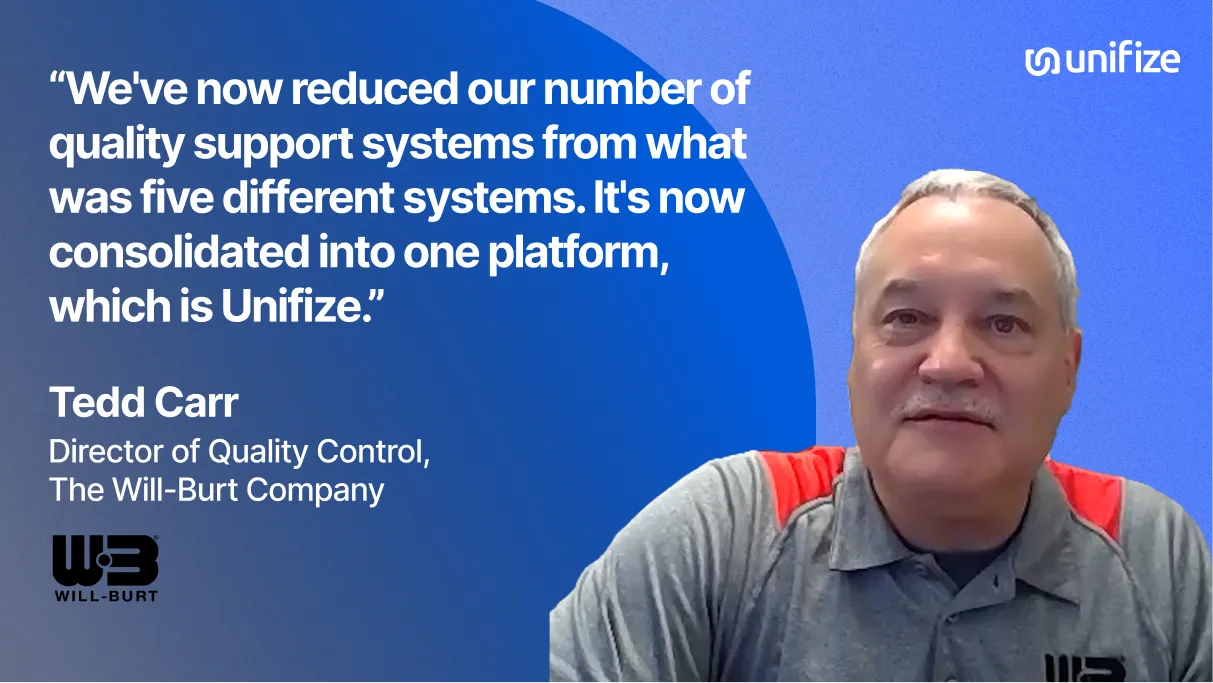
Customers
How a quality veteran from boosted issue closure time by 75% within the first month
Tedd Carr from The Will-Burt Company discusses overcoming their diverse and complex quality challenges across various sectors with Unifize. By consolidating five systems into one, they achieved clear accountability and reduced issue closure from months to days, demonstrating significant efficiency gains and faster decision-making in their quality processes.