Content Library
00:00 - 00:09
My name is Denis I'm a Quality Systems expert, if you can call it that way. Background is in chemistry and biology.
00:09 - 00:20
So I'm a scientist by training, by application. Um, I went to schools, Iowa State, graduated, I went to work in laboratories. So that was really where I started.
00:20 - 00:43
And then from laboratories I started implementing I.T Systems and from there I went into quality systems and started managing laboratories and then found out there was a requirement to do testing and qualifications of systems and from testing of systems ended up with regulations because I figured out how to qualify systems using less effort.
00:43 - 01:06
And by doing that, my manager at that point said, you're really good at this. Maybe you can help do more qualifications of systems in the laboratory. And after that, quality got a wind of what I'm able to do. And once they did that, I was called to do quality activities. Review became my supervisor in the lab and after that moved to a different company and went into quality activities.
01:06 - 01:29
And soon after that I started my own company doing this type of activities of qualifications. So qualifications was really how I got into the industry. And then when I started going into quality assurance activities, one of the things that I found was somebody who could be able to see what was happening and put that into words.
01:29 - 01:43
What I mean by that is there's a lot of activities that happen in a company and sometimes you need somebody. You can see the whole picture, the relationships between information, relationships between systems and data and access.
01:43 - 01:51
And really that drove my passion to understanding how everything supposed to work together. I was called in to be a quality systems analyst.
01:51 - 01:57
I became one of the people in the organization that was able to connect different systems, to be able to communicate.
01:57 - 02:20
And once I did that, the next activity after that was quality assurance, becoming a data driven person, making decisions, getting data. This could be data like CAPA data, this could be data that is used in the industry like Non-Conformances It could be data related to laboratory notebooks failures, aggregating some of that data so that good decisions could be made.
02:20 - 02:37
So once I became a data analyst, the rest is history. They put me into qualifications and putting quality systems together and implementing them through the organization because I understood with the information was located where and how to access that information and being able to present it.
02:37 - 02:54
I was a vice president for quality assurance and regulatory affairs for Harmonic Bionics out in Austin. For that organization, what I did is all things quality related to making decisions based on what information needed to be kept as part of our regulations.
02:54 - 03:13
I have worked in medical devices. I've worked in pharmaceuticals, I've worked in petrochemicals, oil and gas. I've also worked in combinatorial products and some of those industries of somewhat and not have a quality system and tobacco industry also. So I've worked in all those industries.
About Denis Machoka and his role as VP of Quality at Harmonic Bionics

Customers
Denis's experience with Unifize: Revolutionizing quality assurance systems
Quality expert Denis details his transformative journey with Unifize. He praises its efficient design, user-centric approach, and the system's ability to streamline data handling and accelerate time to market.
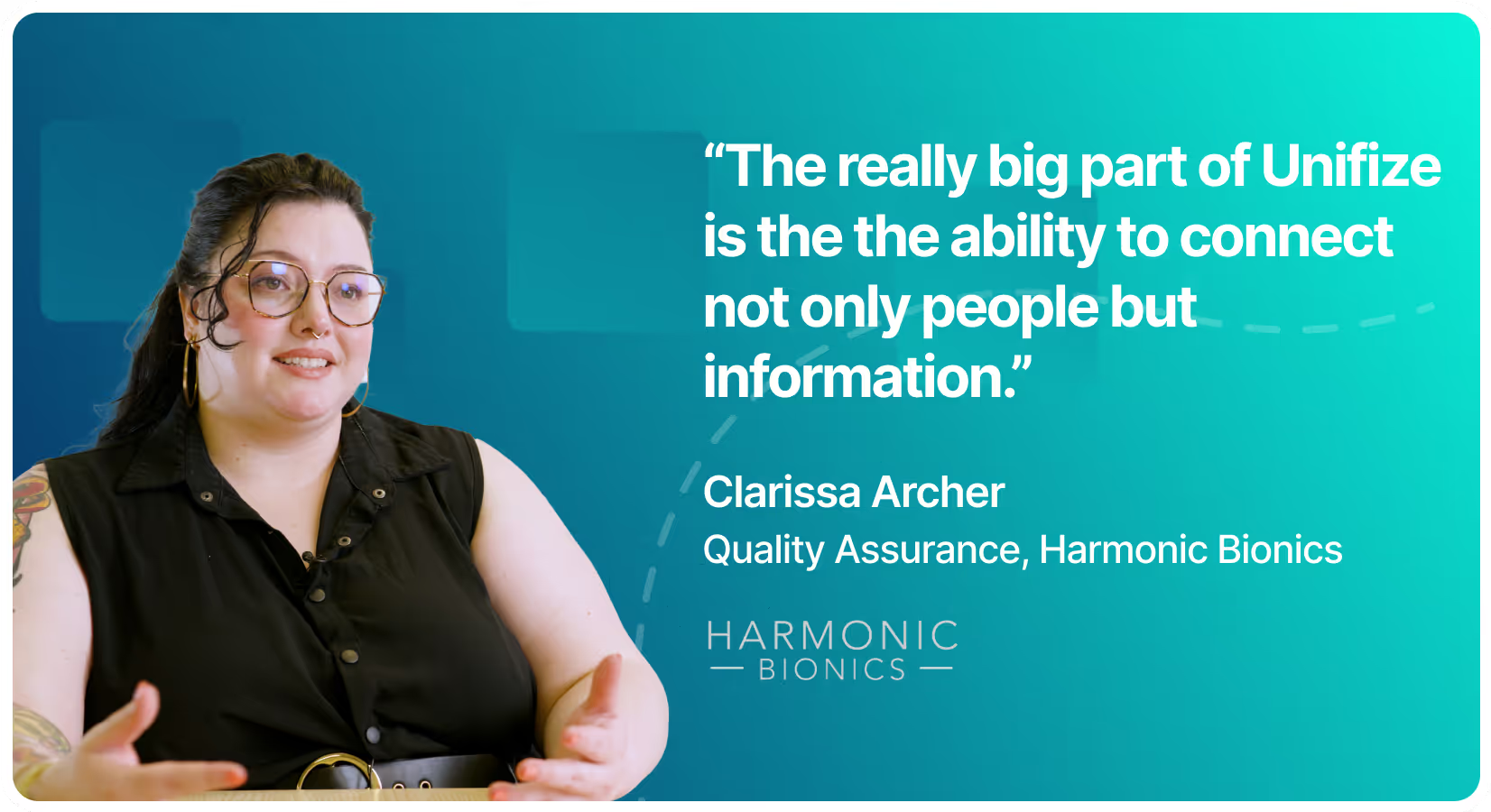
Customers
Harmonic Bionics and Unifize: A seamless transition to regulatory compliance
Clarissa Archer shares her experience integrating Unifize into Harmonic Bionics, underscoring its value in streamlining change control, facilitating communication, and ensuring robust documentation for regulatory compliance in the medical device sector.
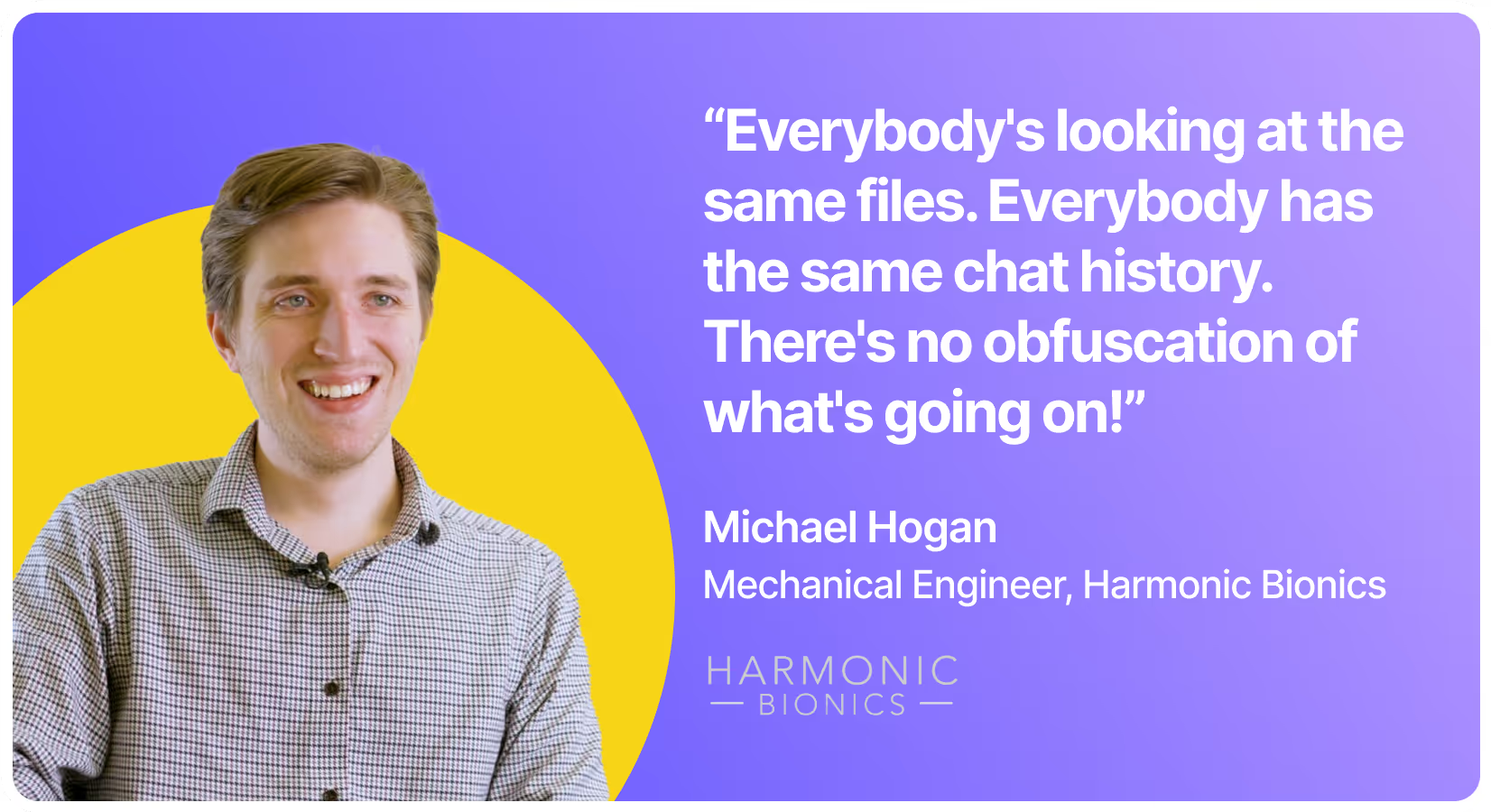
Customers
Engineering efficiency with Unifize: Michael Hogan's insights from Harmonic Bionics
Mechanical Engineer Michael Hogan elaborates on how the integration of Unifize at Harmonic Bionics has streamlined his engineering processes, promoting transparency and rapid turnaround in the medical device domain.
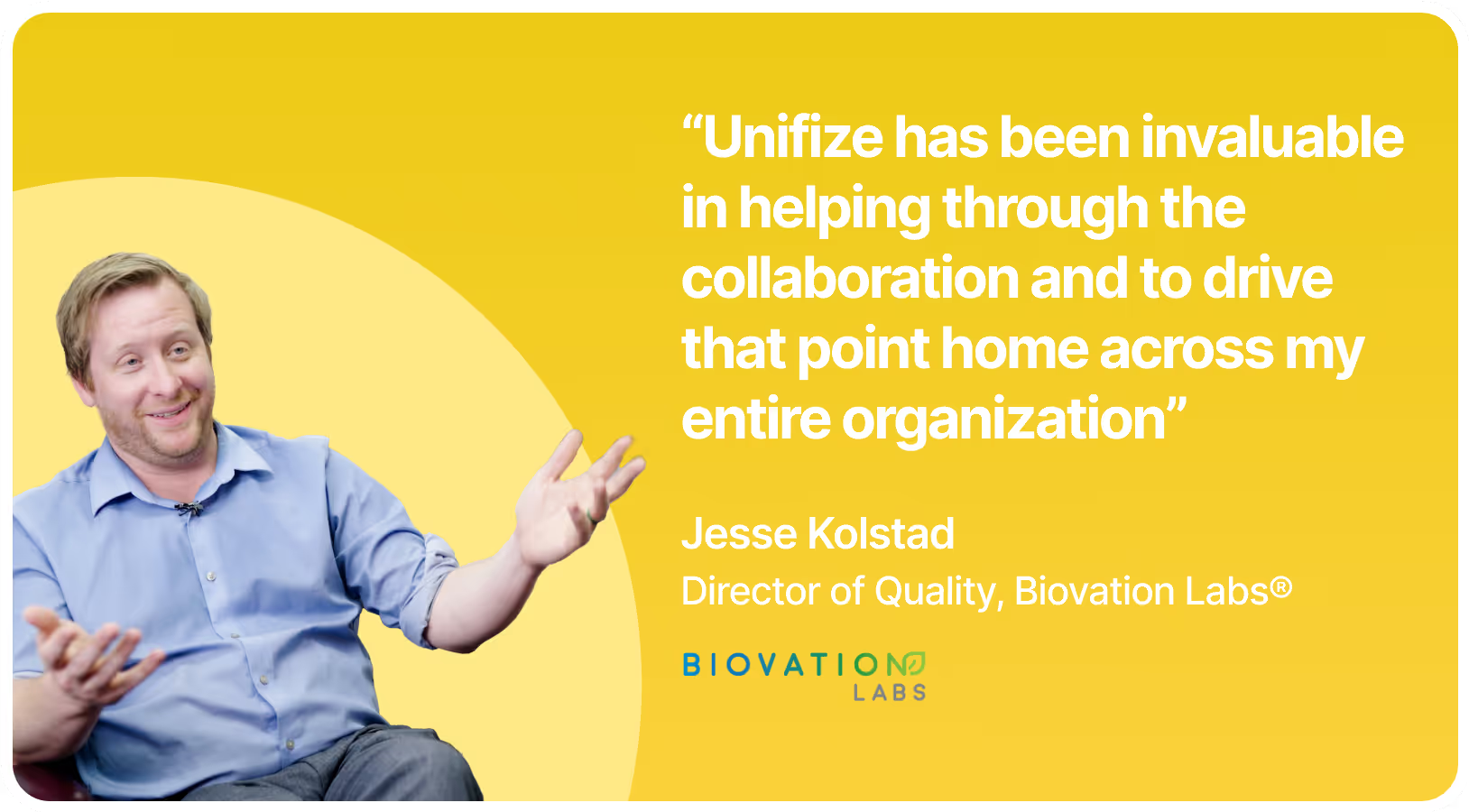
Customers
Here’s how Biovation Labs reduced testing costs from $146K to $65K in two months
Learn how and why Biovation Labs, an FDA regulated nutraceutical manufacturer based in Salt Lake City, took the decision to transition from MasterControl to Unifize for their product lifecycle (PLM) and quality management (QMS) processes.
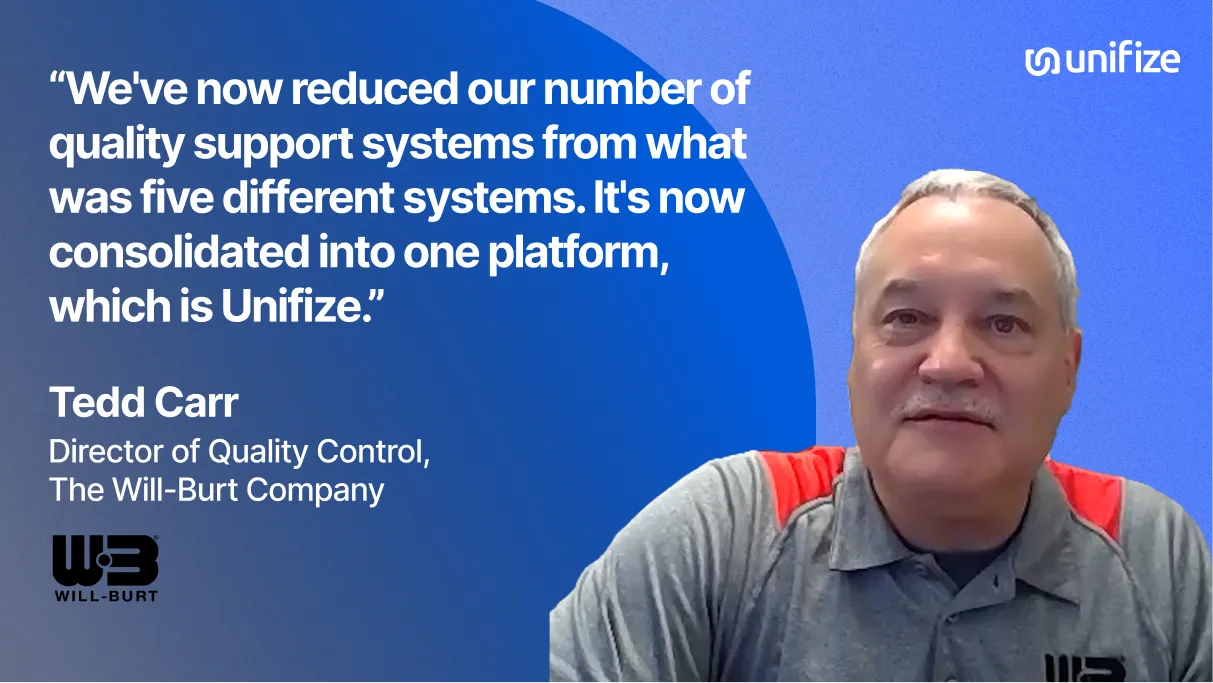
Customers
How a quality veteran from boosted issue closure time by 75% within the first month
Tedd Carr from The Will-Burt Company discusses overcoming their diverse and complex quality challenges across various sectors with Unifize. By consolidating five systems into one, they achieved clear accountability and reduced issue closure from months to days, demonstrating significant efficiency gains and faster decision-making in their quality processes.