Content Library
00:00 - 00:06
But let's start from the consumer's perspective when they’re experiencing, say, using a standard department store shampoo.
00:06 - 00:25
People have certain expectations on how even grocery store brand shampoo will feel, will come out of the bottle, how it will react to pressure, how it applies to the hair, how it feels on the skin, how it foams, there's based on the expectations on all those things.
00:25 - 00:37
And so something that suppliers like us take very seriously is what kind of functional ingredients can we create that has a material effect on the sensory and application outcomes for that consumer experience.
00:37 - 00:57
So a big trend that's been going on for many years now in the shampoo world, is moving away from sulfated surfactants. So you’ll see sulfate-free as a really popular claim on hundreds of different shampoo products out there right now because people are concerned that sulfated ingredients will cause more irritation on the skin.
00:57 - 01:14
With those types of surfactants and really quickly a surfactant is the stuff that makes your shampoo clean stuff off of your hair. It makes it that dirt and stuff. It allows it to be washed off properly when you rinse your hair out. So if you're moving from sulfated surfactants to sulfate-free surfactants, those have a completely different molecular structure.
01:14 - 01:36
And therefore how you make that shampoo is going to change. Some are easier to thicken, some are significantly more difficult to thicken. But the rule is, the more mild your surfactant’s going to be, the more difficult it will be to thicken your shampoo. Now, why is it important to have some level of viscosity of shampoo? No one wants to have a shampoo that comes out water thin.
01:36 - 01:52
It doesn't stay on the hand. It's difficult to apply to the hair. They need to have some level of viscosity for it to feel good and the right kind of texture when it is rubbed in hair and the right kind of sensory feel when it's being washed out at the end. So functional ingredients play a huge part in that kind of experience.
01:52 - 02:17
As people move from sulfated to sulfate-free surfactants, how do you create thickeners that work better with sulfate-free surfactants, especially the most difficult to thicken ones that people more and more people want to see on the ingredient label? Consumers are more savvy now than they've ever been before. All the information that was previously housed in the minds of, chemical experts and formulation experts are now more available on the Internet.
02:17 - 02:41
This is something that informs how we do new product development here at Applechem. And so one of the products that we had was how do we develop a thickener, a modern thickener that can thicken any kind of sulfate-free surfactant on the market today, either from the easiest to thicken ones to the most difficult to thicken ones, or once they're are a cocktail of three, four, five, six, seven different surfactant types in the world.
02:41 - 03:00
What is a universal thickener? Can a universal thickener be created. And so with that thesis that informs the initial research and development phase from the scientists in their laboratory, well, experts in polymer chemistry and so they start developing different types of polymer structures based on their existing knowledge of how these types of thickeners are made.
03:00 - 03:09
Tweaking the structure here and there, testing their performance and seeing can they thicken shampoos with different types of surfactant cocktails inside.
03:09 - 03:32
As that progresses, we start to narrow down the candidates that are giving you the best performance, and then you start to factoring in marketing, sales perspectives, the feedback from those departments, because they're your boots on the ground, they're aware of what trends are going out in the world, what ingredients are in favor, what ingredients are being blacklisted, what going into the future are ingredients that are trending downwards.
03:32 - 03:38
We don't want those ingredients to be inside of your product because you shorten the long term viability of your thickener in this case.
03:38 - 03:49
All that gets funneled into the new product commercialization process. Once you've identified a candidate, you know it's going to work. It works in a laboratory environment, then it's a whole new set of stakeholders involved.
03:49 - 04:11
Now, your manufacturing team is involved because you've got to figure out how do I make this not inside of a small beaker, but in large scale, how do I make it in really large scale? Each time you scale up to a different volume, it presents a different set of problems. So this is why chemical engineers have have jobs and production managers have jobs because trying to figure that stuff out can take months and months and months.
04:11 - 04:35
And sometimes you'll find out that things simply don't work at scale. Let's go right back to the drawing board again. And so the cycle starts over and over and over. Then as a new product gets closer to completion is also the regulatory compliance aspect to hopefully you've done your homework and you make sure that whatever components you've used in your new thickener is compliant with chemical inventories all around the world.
04:35 - 04:56
So you don't have any barriers to adoption. Then as you get closer to releasing the product to the market, making sure all that regulatory documentation is in place, all your marketing documentation is in place, your campaigns all set, your salespeople are prepped, your distributors are trained. So when the is finally ready to launch the product, everything sort takes care of itself.
04:56 - 04:58
So preparation is the name of the game.
How Applechem approaches product development and commercialization

Customers
Denis's experience with Unifize: Revolutionizing quality assurance systems
Quality expert Denis details his transformative journey with Unifize. He praises its efficient design, user-centric approach, and the system's ability to streamline data handling and accelerate time to market.
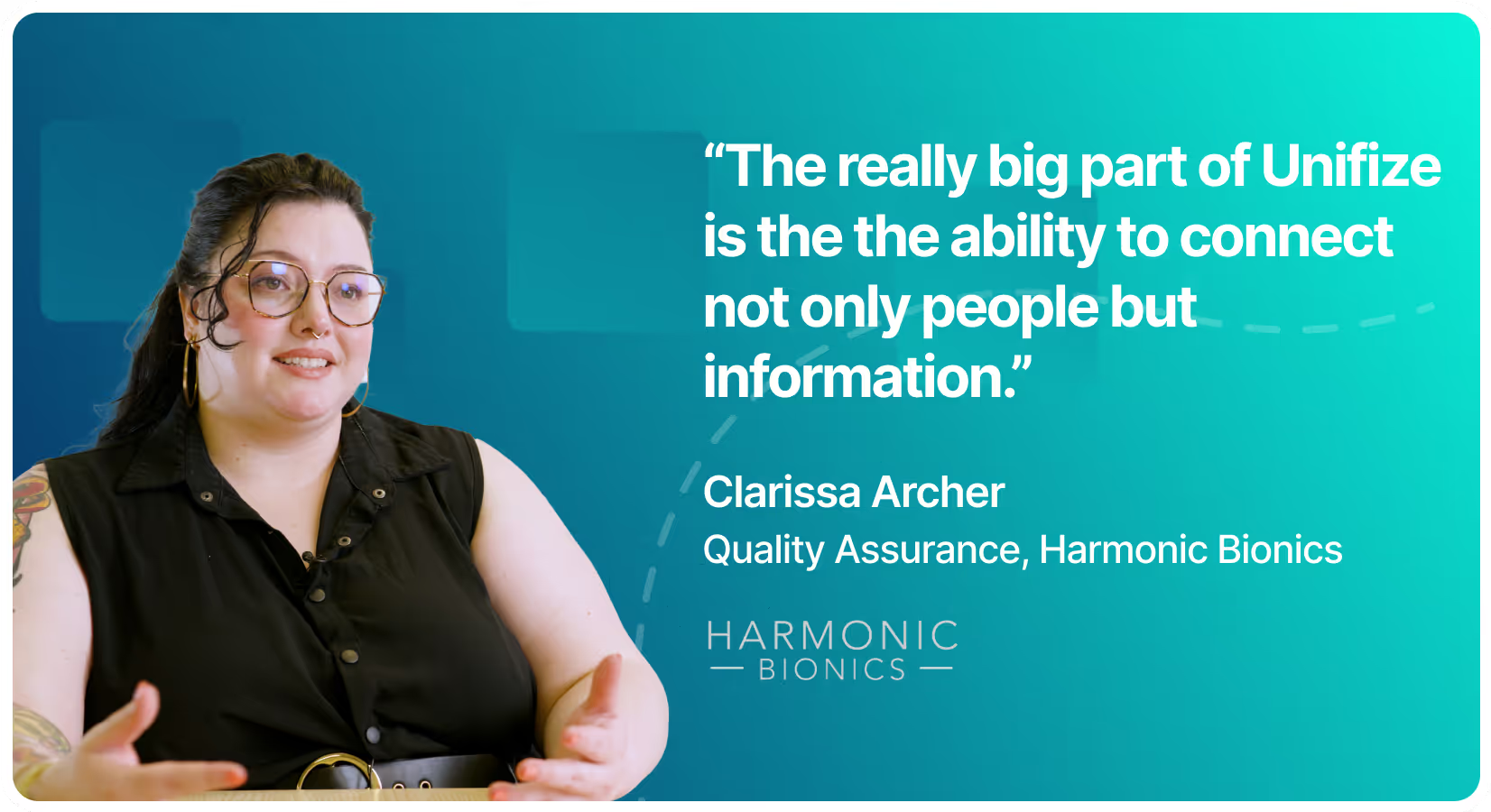
Customers
Harmonic Bionics and Unifize: A seamless transition to regulatory compliance
Clarissa Archer shares her experience integrating Unifize into Harmonic Bionics, underscoring its value in streamlining change control, facilitating communication, and ensuring robust documentation for regulatory compliance in the medical device sector.
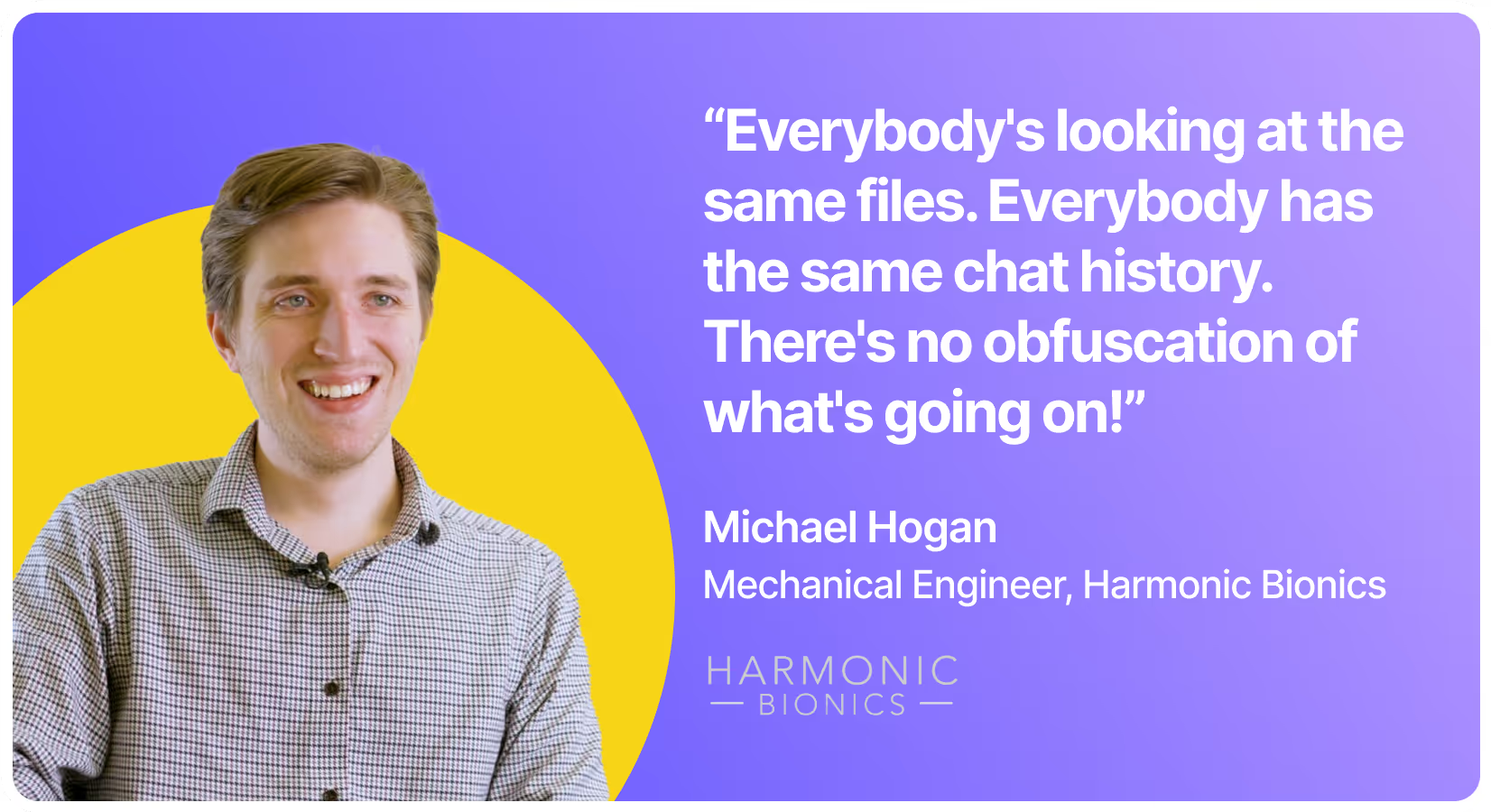
Customers
Engineering efficiency with Unifize: Michael Hogan's insights from Harmonic Bionics
Mechanical Engineer Michael Hogan elaborates on how the integration of Unifize at Harmonic Bionics has streamlined his engineering processes, promoting transparency and rapid turnaround in the medical device domain.
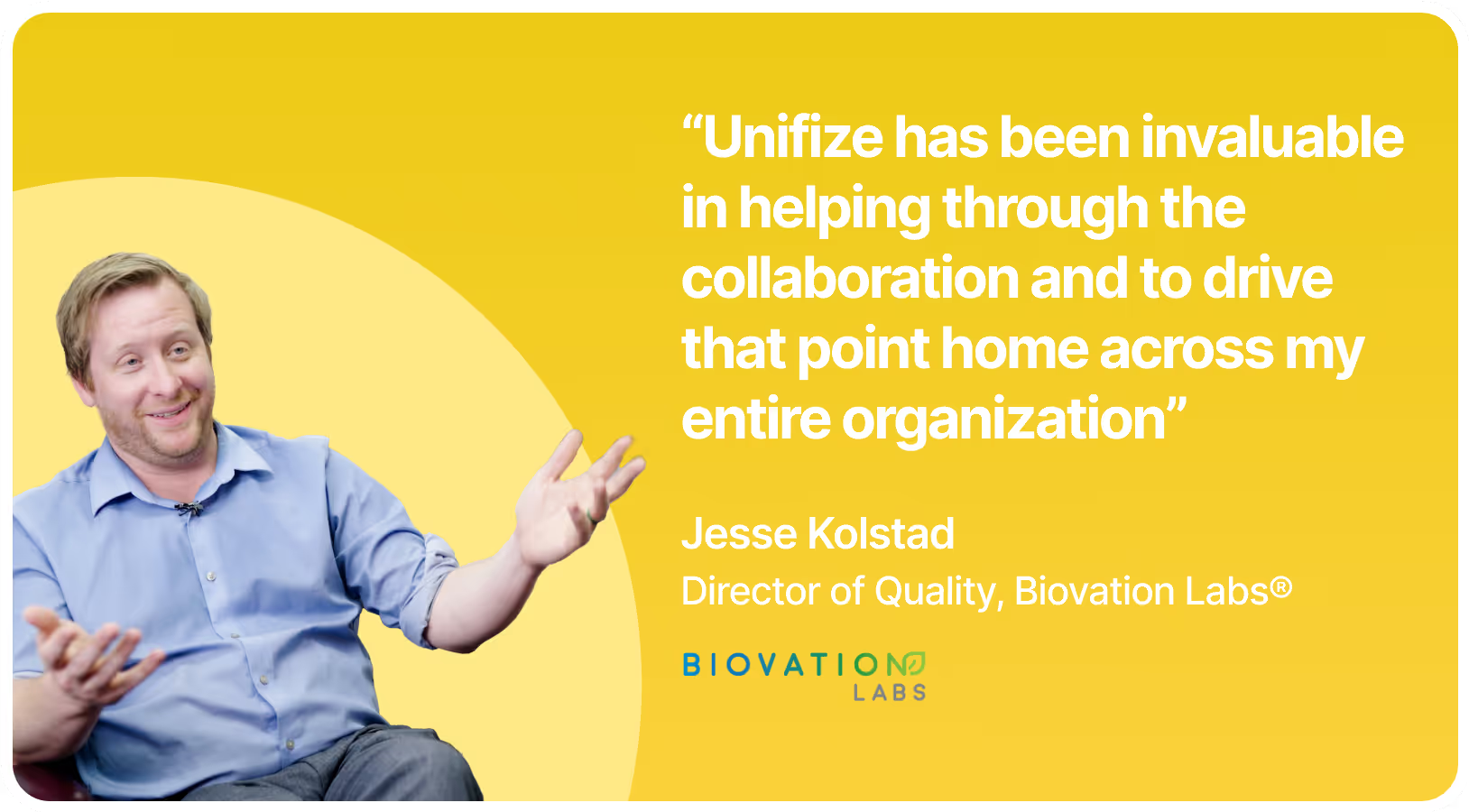
Customers
Here’s how Biovation Labs reduced testing costs from $146K to $65K in two months
Learn how and why Biovation Labs, an FDA regulated nutraceutical manufacturer based in Salt Lake City, took the decision to transition from MasterControl to Unifize for their product lifecycle (PLM) and quality management (QMS) processes.
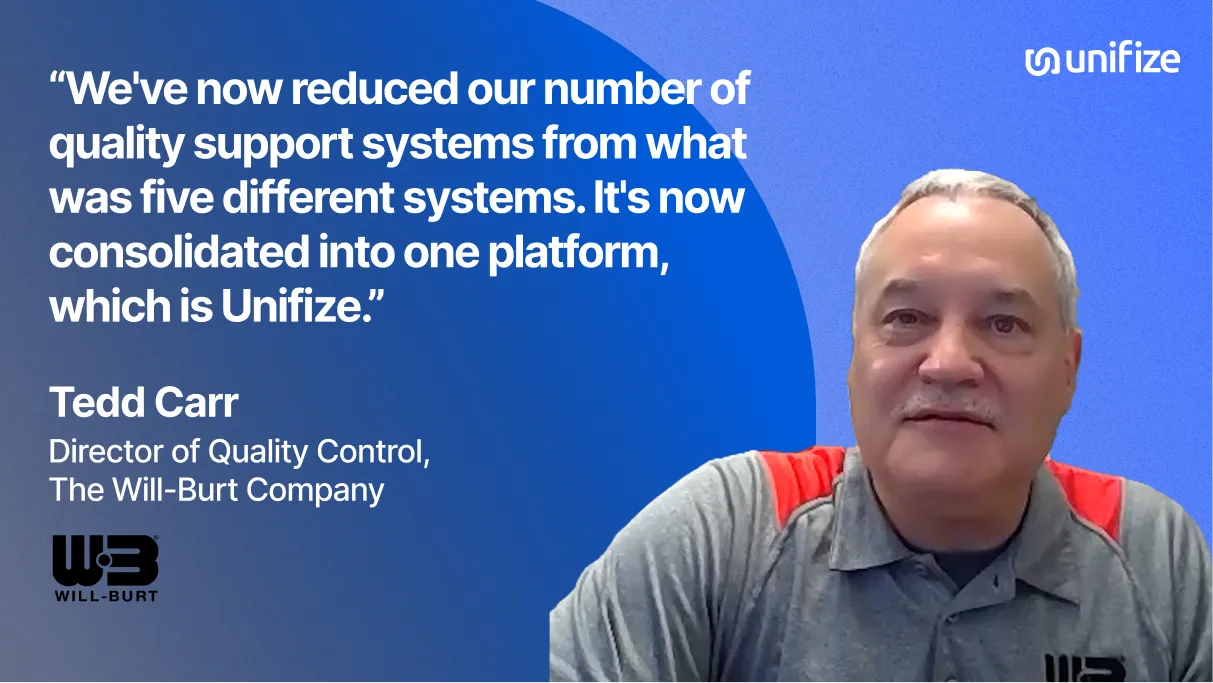
Customers
How a quality veteran from boosted issue closure time by 75% within the first month
Tedd Carr from The Will-Burt Company discusses overcoming their diverse and complex quality challenges across various sectors with Unifize. By consolidating five systems into one, they achieved clear accountability and reduced issue closure from months to days, demonstrating significant efficiency gains and faster decision-making in their quality processes.